What is Stainless Steel?
A Brief History of Stainless Steel
The birth of steel goes back about 4000 years when iron-based weapons began to take the place of bronze due to their increased strengths. For thousands of years, the basis of steel was used without really knowing why it was better than its alternatives. Big breakthroughs came in the late 19th and early 20th century, as steel began to be commercially produced. In 1856, Henry Bessemer came up with a new way to reduce carbon content by introducing oxygen into molten iron. This led to a variety of developments in steel, and the U.S Steel corporation was born in 1901. In 1904, a French scientist, Leon Gillet, developed a mix of alloys that made up stainless steel. In 1913, Harry Brearley documented this process, noting the corrosion resistance, and patenting the first martensitic. Enter: Stainless Steel:
Originally coined “rustless steel,” stainless steel soon began to make waves in marketplaces due to its shiny surface and tremendous strength. It was a true marvel of technology and has really modernized industries like transportation and medicine. Its vast benefits make everyday life easier in ways we don’t even think about.
Most people hear the word stainless or the term stainless steel and their mind jumps to the new fridge or kitchen appliance they were just checking out in a catalog. Stainless Steel, however, is used in thousands of different applications in markets from aerospace to medical and is used for very specific reasons. So, what is it?
Stainless Steel = Iron + Chromium (> 10.5%) + some other stuff
The above equation forms the basis of a stainless steel alloy, but all sorts of elements are used to form different grades of stainless. These different grades have different properties and capabilities and are therefore used for different purposes in many cases. Most of the production for stainless steel is within a group of 10 alloys, but there are over 250 stainless steel alloys that can currently be produced.
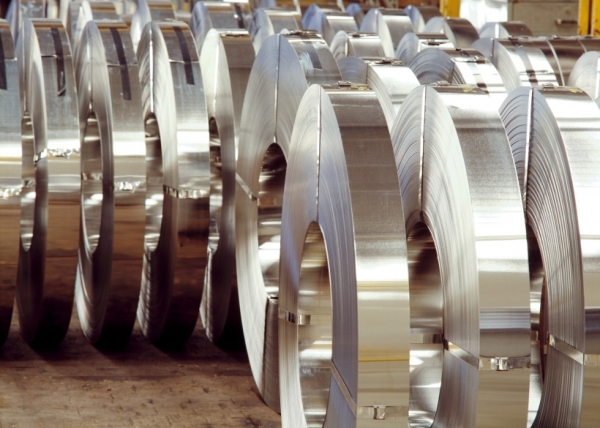
Why is Stainless Steel So Popular in Manufacturing?
So, what makes stainless steel so great as opposed to other metals? Well, everything. It is more corrosion resistant (doesn’t rust), has higher heat and oxidation resistance than other metals, and has higher strength at both room and high temperatures than alternative options. In addition to these characteristics, the unique properties of stainless steel, its appearance, and its low need for maintenance all make it a strong choice for many applications.
Let’s investigate corrosion resistance a little more though. Why does it have corrosion resistance? Why does stainless steel not rust? The short answer: Chromium. Let’s look back at our equation up top. Iron, being the base metal in most stainless steel, usually rusts relatively quickly when exposed to oxygen on its lonesome. What separates stainless from carbon steel or other types of steel, is the chromium oxide layer that is added to this base metal. This layer works to form a passive film which greatly increases the corrosion resistance and, in turn, minimizes rust. As one might guess, increasing the amount of chromium increases the resistance to corrosion.
Stainless Steel has many different alloying options and the different metallurgy of each alloy results in different families of stainless steel and different grades within those families. There are 5 main families of stainless steel:
- Austenitic (300 Series) Stainless Steel : The most commonly used, austenitic stainless steels are known for their exceptional resistance to heat and corrosion.
- Martensitic (400 series) Stainless Steel: Unlike austenitic, martensitic stainless steel can be hardened with heat. These treatments make martensitic steel stronger than other types.
- Ferritic (400 series) Stainless Steel : Containing more than 12% chromium, ferritic steels are essentially non-hardenable by heat treatment and only slightly hardenable by cold rolling.
- Precipitation Hardening (PH Grades) Stainless Steel PH alloys contain small additions of copper, aluminum, phosphorus, or titanium. After a part is formed is from these alloys, it is given an age-hardening treatment in which these elements precipitate as hard intermetallic compounds that significantly increase hardness and strength.
- Duplex: this type of stainless steel is called "duplex" because these alloys have a two-phase microstructure that consists of grains of ferritic and austenitic stainless steel.
Within these families, there are different grades of stainless. Adding different elements changes the chemistry of each grade and changes the factors of that grade which can affect the application of the material. For example, in the case of formability vs. weldability.
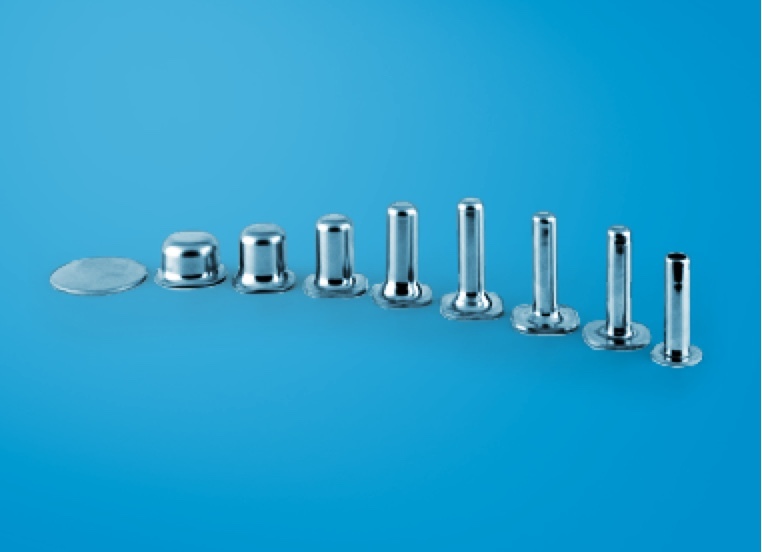
Which Stainless Steel Grade is Best for Formability?
If one would look for an alloy with better formability they would look for a grade with increased Nickel, Copper, and Manganese content such as 305 Stainless Steel Wire. Typical 305 Stainless Steel applications include:
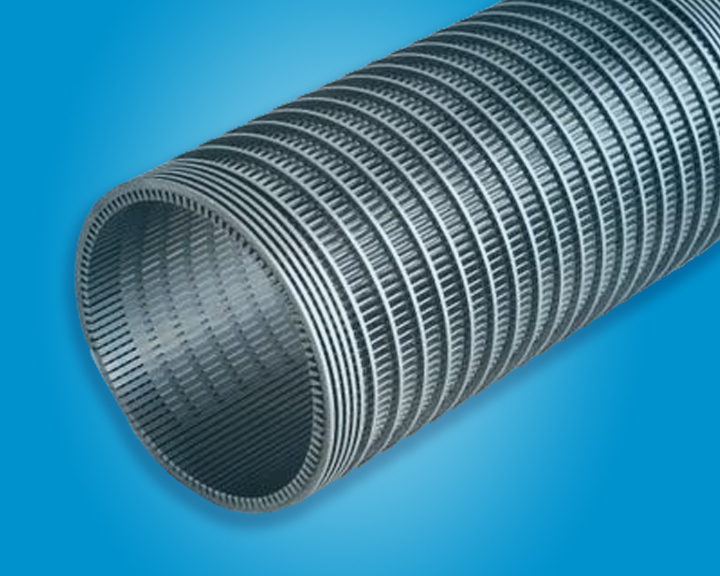
Which Steel Grade is Best for Weldability?
While looking for the alloy with better weldability, we could look for an option with increased titanium or niobium content, such as 316L Stainless Steel. Typical 316L Stainless Steel applications include:
- Chemical Screens
- Oil Refineries
- Flexible Metal Hose
- Marine Applications
- Textile Industry parts
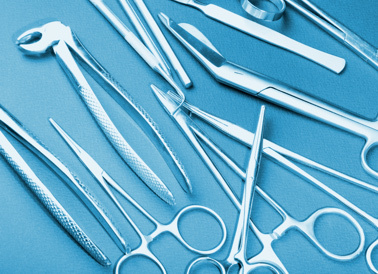
Which Stainless Steel Grade Provides Increased Strength?
Another common characteristic manufacturers look for during part making is material with increased strength. This is achieved with stainless steel by adding Carbon, Nitrogen and/or Vanadium to the stainless alloy. 440 Stainless Steel has a higher carbon content than most stainless options and is, therefore, one of the stronger alloys we have available. Typical 444 Stainless Steel applications include:
- Cutlery
- Scissors
- Surgical Instruments
- Firearms
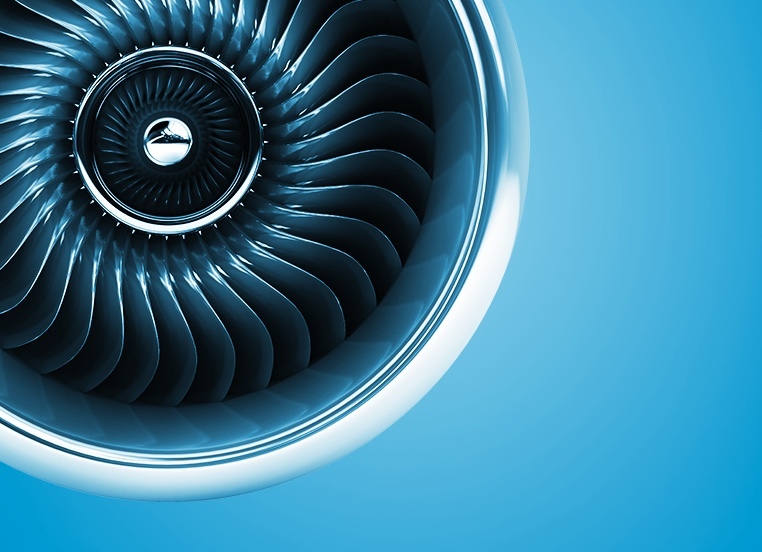
Which Steel Alloy Has Great Oxidation Resistance?
Oxidation resistance is yet another popular characteristic part makers look for in their metal needs. Oxidation resistance is an unusual one, in that it is achieved in stainless steel by increasing the Silicon and/or Aluminum content. 321 Stainless Steel is a popular choice for many reasons, but its’ higher Silicon content does result in better resistance to oxidation. Typical application of 321 Stainless Steel include:
- Exhaust stacks and manifolds
- Jet engine parts
- Fasteners
- Aircraft collector rings
- Tubing
What are the benefits of cold-rolled stainless steel?
Cold rolling stainless steel allows us to reach thicknesses and tolerances that nobody would have thought possible at the time of its’ invention. Being able to reach thicknesses as small as .00039 inches (Yes 3 zeroes is correct) has been a catalyst in propelling the transportation and medical industries in the future. Cold rolling with precision characteristics in mind also allows us to increase the physical properties and strength of the alloy being rolled. Stainless steel truly has some amazing capabilities and will hopefully be a partner in technological advancements for years to come.
Any more questions on stainless steel? Contact a stainless steel specialist at Ulbrich and we’ll be happy to answer them.