17-7PH Stainless Steel: An Introduction to this Workhorse Stainless Alloy
Stainless steel is a widely used group of alloys used across various industries, including automotive, aerospace, energy, medical, food processing, and home appliances. The type of stainless steel you need is dependent on your application and final product goals.
One such stainless alloy is 17-7PH stainless steel. 17-7PH is one of the most formable of all precipitation-hardening stainless steel grades. 17-7PH is known as the "Workhorse Alloy" for good reason as it has high strength and good formability. We hope this will serve as your introductory guide to 17-7PH stainless steel.
Ulbrich has supplied 17-7PH in coiled strip and wire forms since the 1980s.
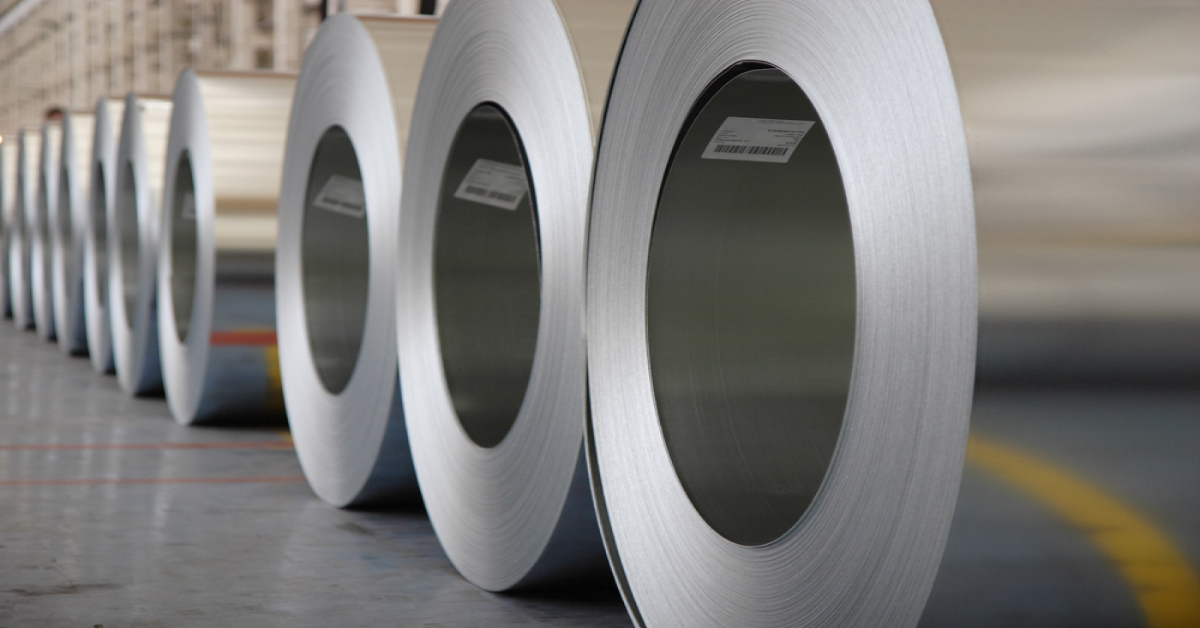
What Does the 'PH' indicate in 17-7PH Stainless Steel?
The 'PH' behind the '17-7' in the alloy name means that this is a precipitation hardening alloy. The principle of precipitation hardening is that a supercooled solid solution changes its metallurgical structure on aging. Precipitation hardening stainless steel offers a means of obtaining very high strength for a stainless material through a low-temperature treatment applied after fabrication with minimal dimensional distortion. The PH alloys of stainless steel fall into three categories: austenitic, semi-austenitic, and martensitic. Each type has unique chemistries, heat treatments, properties, and applications associated with it.
It is essential to understand that 17-7PH is a semi-austenitic PH alloy. In a semi-austenitic PH alloy, quenching to room temperature after soaking produces an austenitic structure. Martensite is formed by one of two processes. The first is cooling the steel to sub-zero temperature; the second involves conditioning heat treatments that remove carbon from the solution in the form of chromium carbides.
Like austenitic stainless steels, semi-austenitic PH Alloys such as 17-7PH have good corrosion and oxidation resistance and do this without losing toughness and ductility typically associated with high-strength materials. 17-7PH is known for its ability to gain higher strength through heat treatment, similar to martensitic grades.
What Does '17-7' in 17-7PH Stand For?
The numbers "17" & "7" making up the name of this alloy refers to its chromium content (~ 17%) and the amount of nickel (~ 7%) present in the alloy. This numbering is a common way to refer to stainless steel grades. For example, 304 stainless steel is sometimes referred to as 18-8 due to the composition being approximately 18% chromium and 8% minimum nickel. In addition to the chromium and nickel, other vital elements in 17-7PH are manganese and aluminum. This chemistry of this stainless alloy grants 17-7PH good corrosion resistance, high strength and hardness, formability, and excellent fatigue properties, which make it a very desirable alloy for many applications.
The manganese reduces the critical cooling rate during hardening, meaning it increases the hardenability of this grade. While the aluminum is added for deoxidizing and grain refining, however because of the aluminum content, working with 17-7PH can present challenges.
Aluminum serves as the hardening mechanism and has a strong affinity for Oxygen. Aluminum oxide is extremely abrasive and will wear down tooling if it is present in excessive amounts on the surface 17-7PH. It's important to note that when annealing 17-7, the adequate atmosphere, including ensuring minimal amounts of trace oxide in the furnace, is required to minimize the tendency for the material to form Aluminum oxide. The complexity and precision needed to produce this material to the highest quality standards are why manufacturers working 17-7 should seek highly capable precision manufacturers who can control this process. Quality can only be achieved through constant measurements of temperature, anneal speed, dewpoint, trace Oxygen, and quench rate, which is carefully monitored in real-time and examined for effectiveness.
What are the Other Categories of Stainless Steel?
Stainless steel grades fall into five categories:
In the 1930s and 40s, a standardized numbering system for the different stainless steel grades was developed by the American Iron and Steel Institute (AISI) and SAE to categorize the various stainless steel types. The AISI/SAE stainless steel numbering system is as follows:
- 200 series - High-manganese austenitic alloys
- 300 series - Chromium-nickel austenitic alloys
- 400 series - High-chromium ferritic and martensitic alloys
- 500 series - 4-6% chromium alloys
- 600 series - Proprietary alloys (many PH alloys fall in here)
This system was later replaced in the 1970s when the ASTM and SAE initiated the Unified Numbering System for Metals & Alloys. This system consists of a prefix letter and five digits to designate a material composition. The letter prefix represents a material type, the first three digits typically match older three-digit numbering from AISI/SAE system, and the last two digits indicate modern variations. Details are explained in ASTM E527, "Standard Practice for Numbering Metals and Alloys in the UNS." UNS is now the accepted numbering system for the steel industry in the US. Other countries have their own numbering systems. In the 1980s, the International Standards Organization (ISO) attempted to develop a uniform numbering system. This effort failed, resulting in many different designations depending on the country of origin, for each alloy.
An example of the differences in the numbering systems for the grade 17-7PH would be:
1. Japanese Industrial Standards
2. Deutsches Institut Normung – West German Steel Specification
3. Europaischen Normen – Western Europe
How is 17-7PH Stainless Steel Manufactured?
17-7PH is manufactured the same way as other stainless steels.
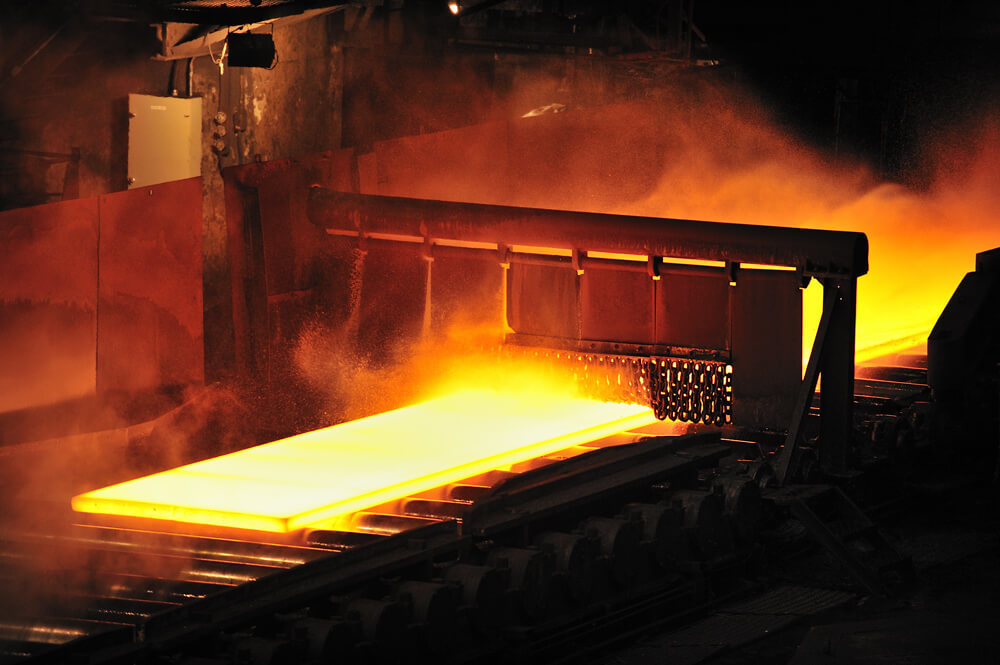
Steps of the Stainless Steel Making Process
- Melting and Refining – Stainless steel scrap and raw materials get added to an Electric Arc Furnace (EAF). Various refining stations, such as Argon Oxygen Decarburization (AOD), Ladle Metallurgy Station (LMS), Wire Feed Station (WFS), and the Argon Stir Station, are used to get the steel to the desired chemistry and temperature.
- Continuous Casting – The molten metal is transferred to a ladle then to a tundish and continuously cast into ~ 10" thick slabs. The width of the slabs can vary, as can the length.
- Hot Rolling – In hot rolling, the slabs of metal pass through a furnace, which heats them to the desired temperature depending on the grade of stainless steel that is being processed. When the desired temperature is achieved, the slabs run through a series of rolls, reducing the thickness of the material from approximately 10" thick slabs to 1/8" thick strip. Afterward, the strip is coiled for further processing.
- Anneal & Pickling – Annealing is the process of heating the material to the desired temperature to soften and set properties, which allows the material to be further processed by cold rolling or fabricated into parts. Pickling is the process that removes the scale formed on the surface through hot rolling or annealing in the atmosphere through the immersion of the strip in an acid solution. These two processes can be combined into one single process known as a continuous anneal and pickle line.
- Cold Rolling – The process in which the steel is passed through one or more pairs of rolls at a temperature below the recrystallization temperature to reduce the thickness to the desired gauge.
- Slitting – The process of cutting large, wide coils of steel into narrower widths.
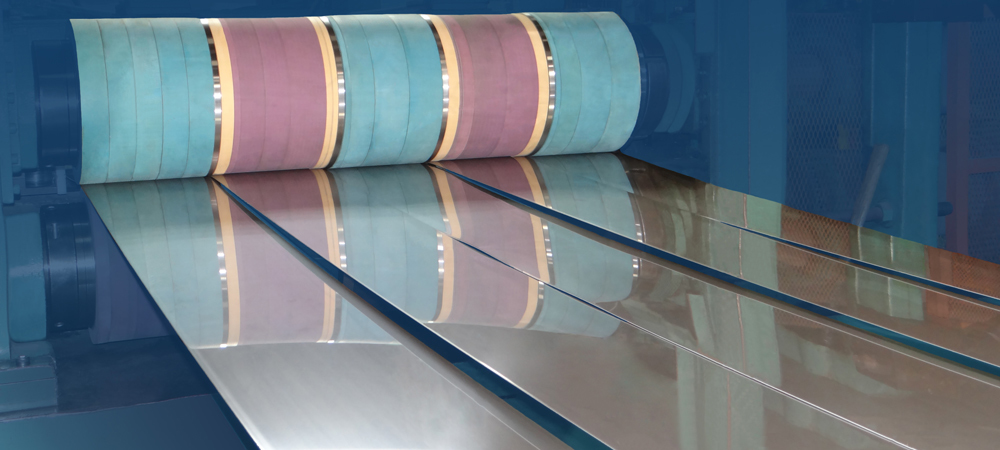
What are the Differences Between 17-7PH Stainless Steel and Other Types of Stainless Steel?
Different types of stainless steel possess different properties and are suitable for varying applications based on these characteristics. Let's take a look at the differences between 17-7PH stainless steel and other types of stainless steel.
17-7PH Stainless Steel
17-7PH stainless steel is chromium-nickel-aluminum, semi-austenitic PH Alloy. Desirable properties that engineers and purchasers seek out this alloy for their applications include:
- High strength
- Good corrosion resistance
- Excellent fatigue properties
- Good formability
- High-temperature properties
This type of stainless steel is less magnetic than other PH grades but provides high strength and hardness, good formability, and offers minimal distortion following heat treatment. This combination makes it suitable for many aerospace applications.
Austenitic Stainless Steel
These stainless are either chromium-nickel (300 series) or manganese- nitrogen (200 series) alloys. They contain a minimum of 16% chromium, and the nickel can range from 3% - 30%. Molybdenum can be added for increased pitting corrosion resistance. Austenitic stainless steels are non-magnetic in the annealed condition but become partially magnetic through work hardening. This largest category of stainless steel has excellent formability, corrosion resistance, and a wide range of strengths available, making them excellent choices for almost every application.
Ferritic Stainless Steel
Ferritic stainless steels are straight chromium grades with the Cr level varying from 10.5 – 30%. They make up the 400 series of alloys, which have good elevated temperature oxidation resistance, good ductility, and are magnetic. These properties and their relative price stability due to low nickel and other alloying elements make them an excellent fit for many automotive applications.
Martensitic Stainless Steel
Often referred to as 400 series alloys, these stainless steels are comprised primarily of chromium and carbon. Martensitic stainless steels are magnetic and capable of being heat-treated to very high hardnesses and strength levels.
Precipitation Hardening Stainless Steel
Precipitation hardening stainless steels are chromium-nickel with additional key elements depending on the grade. They can attain very high strength as a result of the precipitation-hardening process while maintaining toughness.
Duplex Stainless Steel
Duplex stainless steels are a combination of austenitic and ferritic stainless steel, hence the name. These alloys have been developed for applications in which high strength and excellent corrosion resistance are essential. They are used extensively in the oil & gas industry, pulp and paper industry, and chemical refineries.
17-7PH Stainless Steel Applications
17-7PH stainless steel is ideal for any number of applications. It is excellent for products that need a high degree of corrosion resistance and a high degree of strength. Common applications include:
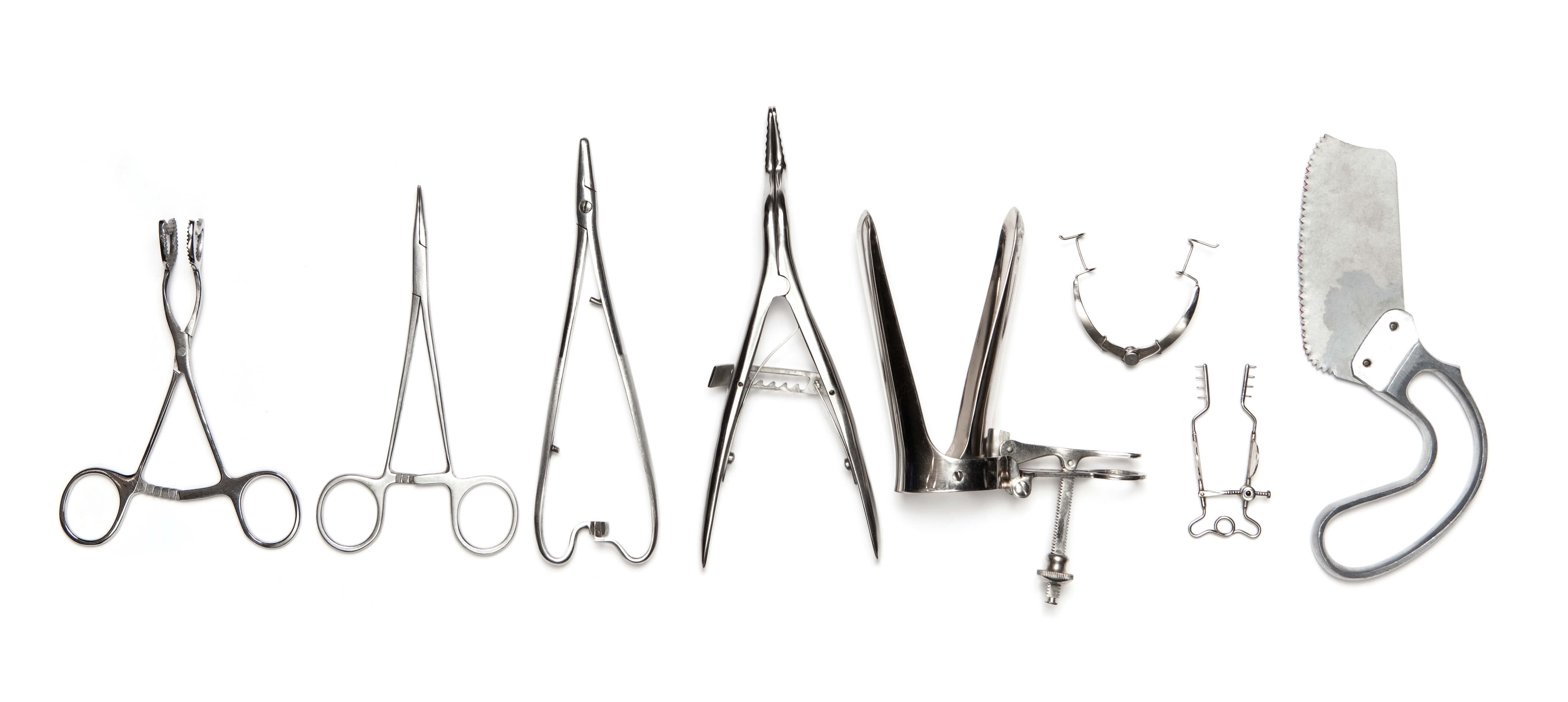
- Numerous Aerospace Applications
- Chemical processing equipment
- Food processing equipment
- Oil and petroleum refining equipment
- Springs
- Bellville Washers
- Heat exchangers
- Surgical Parts
- Honeycomb Structures
- Blades
The Right Stainless Steel Alloys for Your Production Needs
Selecting the right alloy for your production needs makes all the difference in manufacturing a functional product to fit your application needs. Ulbrich has an experienced team of metallurgists and manufacturing experts who can help our clients from start to finish. Our team of metallurgical experts and product managers have decades of assisting manufacturers with the alloy selection process, should you require it. These specialists are happy to take the time to understand your needs and thoroughly explain all of your options. From there, we'll be glad to roll up our sleeves to assist you in overcoming any production challenges you face to ensure a final product that not only meets your production requirements and exceeds your expectations. Contact us today for information on how we can help you with your manufacturing needs.