Alloy Selection Guide: Key Factors to Consider When Specifying Metals for Manufacturing
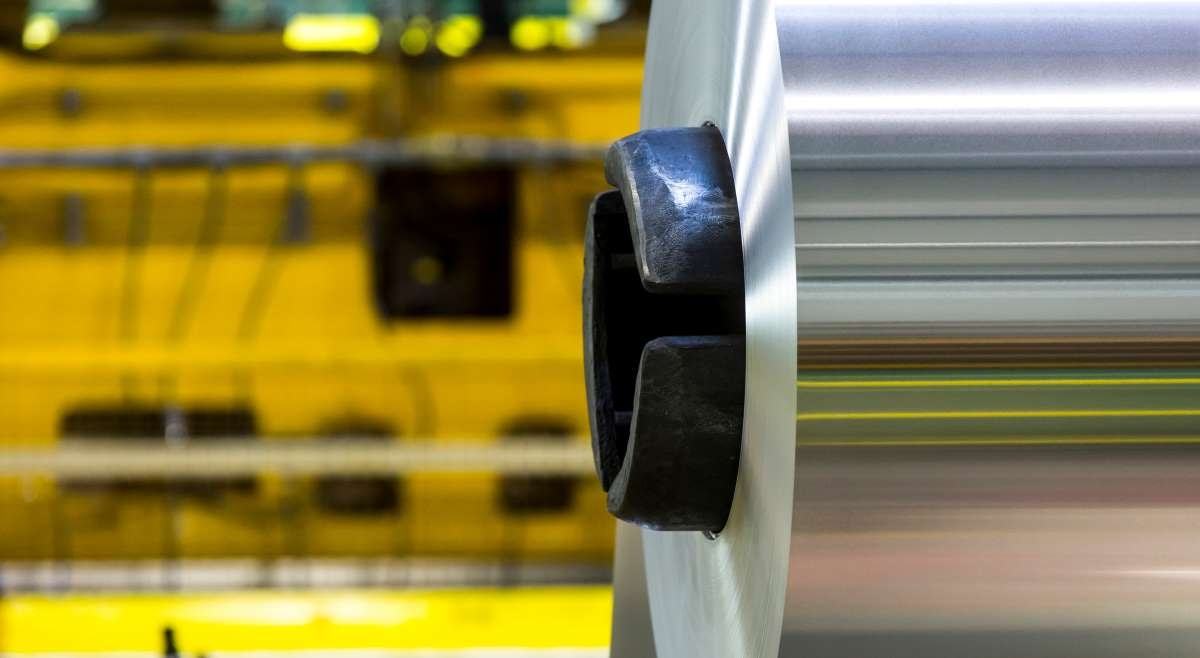
A lot goes into the planning and prototyping process when developing a new application for a specific end use. In this alloy selection guide, our goal is to help you find the right balance across all the common factors and land on the alloy that fits your manufacturing process, application needs, and buying requirements. Once you know your goal, you must determine what alloy is going to be the best for YOUR product and be able to justify it. Many aspects need to be considered in alloy selection and they are not always weighted evenly. Purchasing usually has certain things to consider, while Engineering may be evaluating things differently, and the same goes for Production. Departmental, or the interests and requirements of different disciplines within your organization may have their own factors to consider that may not always line up but is important to consider all main factors of alloy selection when choosing the metal for your product.
Manufacturers understand that every metal alloy has unique properties to weigh against each other when deciding on an alloy for your product. The main factors that are often considered are:
- Physical Properties
- Mechanical Properties
- Cost
- Service
- Fabrication
- Surface Properties
How each of these ranks will, of course, vary from project to project and application to application. The point is though, that all of these should be factored into your selection and if you are not sure how to go about ranking them, we should dive a little deeper into the ins and outs of each. Ulbrich's Metallurgy department can always help with this too.
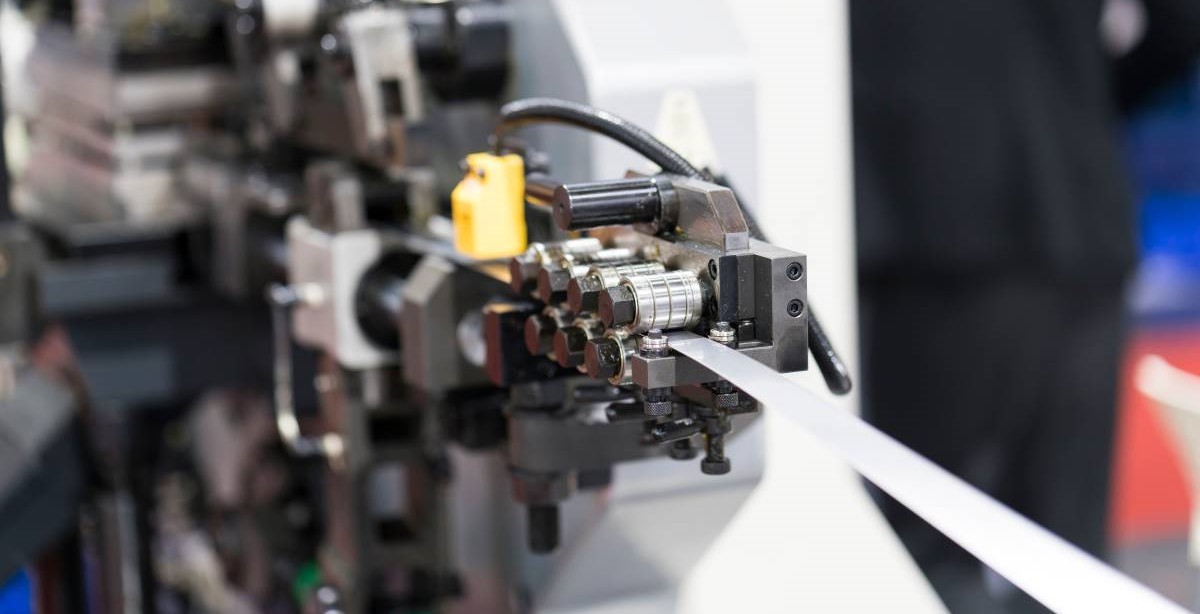
Physical Properties
This is a crucial factor in determining the appropriate alloy for your application because there are so many different things to look at. If you are looking for something that may be exposed to water, we would want to consider an alloy with excellent corrosion resistance. Other applications may bring things like thermal, electrical and magnetic properties into play. If the end use of a product is within the aerospace field, it may be worth looking at how the alloy operates under high and low temperatures, so a Nickel alloy may be the best option. If it is a consumer product, aesthetic appeal could be more important, so it will be worth looking at the different finish options.
Mechanical Properties
Another factor that always needs to be looked at, mechanical properties of an alloy can vary greatly depending on both its content and how it was processed. Strength (tensile and yield), ductility, hardness and toughness are all often looked at within the umbrella of mechanical properties. Some applications are better off with harder material while some, maybe they require a lot of forming, need softer material. This can all be controlled during the rolling and annealing processes. Working closely with a stainless steel and special metals precision reroller with engineering and metallurgy teams on staff are a helpful resource for getting your desired alloy's mechanical properties right for your needs.
Cost
This can often be a key prohibitive factor in the alloy selection process. It is important however, within cost, to explain why things are priced the way they are. Different alloys have different elemental content, are processed in various ways and must be processed differently. By this I mean, a certain alloy might be cheaper as a raw material, but if its’ lifespan is 1/3 the lifespan of an alternative option, is it really worth it? Will money or time be saved in the long run by going with more expensive but also more suitable/qualified option. These are a few questions to consider when weighing cost as a long-term factor.
Service
This factor in alloy selection plays into some of what was mentioned in the Cost Section. Meaning, what will the maintenance be like on your application because of the alloy you selected? In most scenarios there are some type of outside factors such as temperature or other environmental concerns that may affect how long a product will last before it must be serviced. Choosing the best possible alloy for your product should extend the time between servicing or just extend the lifespan. We can look in depth at this and determine if it makes more sense to select an alloy that will be serviced a lot and is easier to process up front or a specialty metal that will need little to no service.
Fabrication
Manufacturing and producing this part is where we need to look at the appropriate fabrication selection. Maybe your part needs to be deep drawn and we should take a look at an alloy with higher Nickel content, such as 305 Stainless Steel. In other scenarios a part may need to be stretch formed or welded and we could recommend an appropriate alloy for that, such as 316L stainless steel in strip or wire. 316L has resistance to intergranular corrosion following the welding process. Ulbrich is happy to review any considerations such as these.
Surface Finish & Surface Properties
A lot of different characteristics can fall under this category and all are important to making alloy selection that makes sense for your process and part. Different end uses for a part will make a manufacturer value different types of surface properties such as the appearance, abrasion, and a coating or the finish. Ulbrich offers many different finish capabilities and will work with you to reach appropriate surface roughness and appearance for your application.
Choosing the appropriate alloy is essential for a successful end product and it is important to give weight to all six factors discussed when doing so. Of course, certain applications will value fabrication and mechanical properties above the others while a separate application may value cost and service higher. It all depends and Ulbrich is here to help make a recommendation when needed. If you already have an application in mind, please contact a specialist and we can get started today!
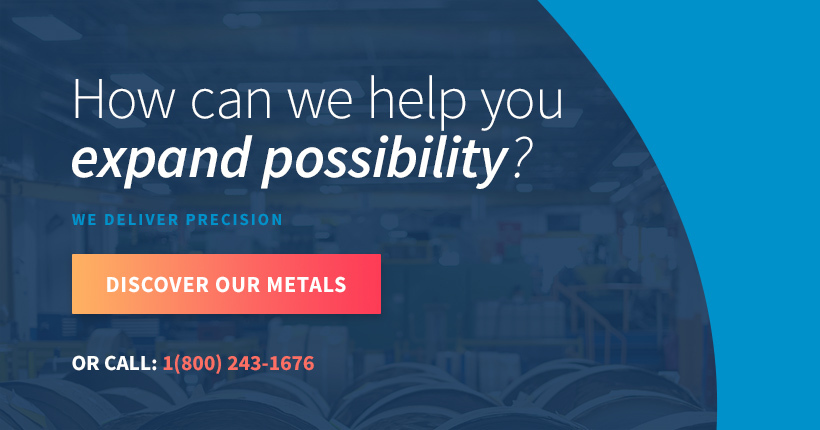