How to Specify Aerospace Alloys
The challenge of specifying alloys for aerospace applications
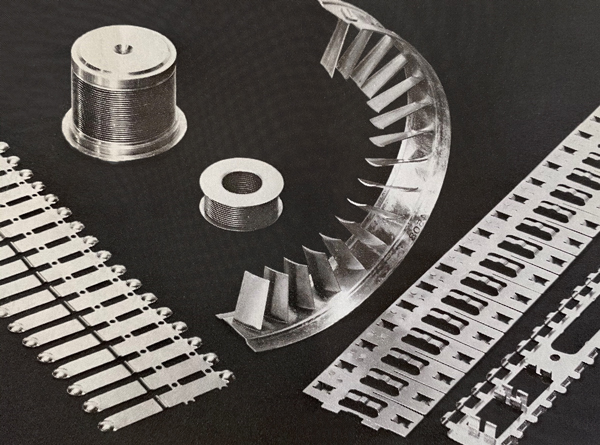
You have combed the metals references and found the perfect alloy for that troublesome part in one of the company’s best-selling products. It has the corrosion resistance, deep draw formability, design strength . . . everything.
Now enter the real world of supply and demand.
Your local service centers indicate they do not have the alloy in the temper and thickness you need, and they are not too optimistic about finding it. And your order is not large enough to have one of the big, integrated mills produce a heat lot.
How specifying alloy properties, not chemistry, can solve your problems
The answer is to be more flexible in your specification. Do not lock into a single alloy or chemistry. This is especially true when dealing with stainless steels and nickel-based alloys because there are so many options available. But the very extent of the selection will work in your favor if you can give the supplier some latitude.
Instead of naming a chemistry, specify the properties and characteristics that are critical to the success of your application. These include resistance to specific types of corrosion, operating temperatures of the part, wear resistance, strength, elongation and processing characteristics such as formability, weldability, etc.
Within this framework, suppliers of these alloys can usually meet your requirements.
The characteristics of stainless steel and nickel-based alloys are created by alloy additions to the base metal. In today’s world, there is a chemistry available, either in a generic or proprietary alloy, that will meet almost every need, no matter how specialized.
How can a stainless steel or special metals service center or re-roll mill help?
If your order is large enough, an integrated producer can meet your requirements, but it may be months before a heat of that metal is produced. If your quantity is small or if you find it impossible to wait for the mill’s lead time, your service center can tap their vendor sources to meet your specification with a similar alloy, one that is specifically processed to meet, or at least come close to, the chemistry you have specified.
The service center can utilize their reroll sources to custom produce the finished product from previously produced hot or cold rolled bands. Those coils are precision rolled and annealed from thicker gauges to the specific dimensions and properties specified. In this way, a reroll source can provide their customers with most specialty requirements.
Re-rollers with metallurgists are great resources to help solve your spec issues.
In fact, the reroll mill may actually assist in writing the specification, especially if the alloy requires precision gauge tolerances or a special surface finish. With such elements as work hardening and thermal processing involved, ordering these alloys often requires a special understanding of applied metallurgy.
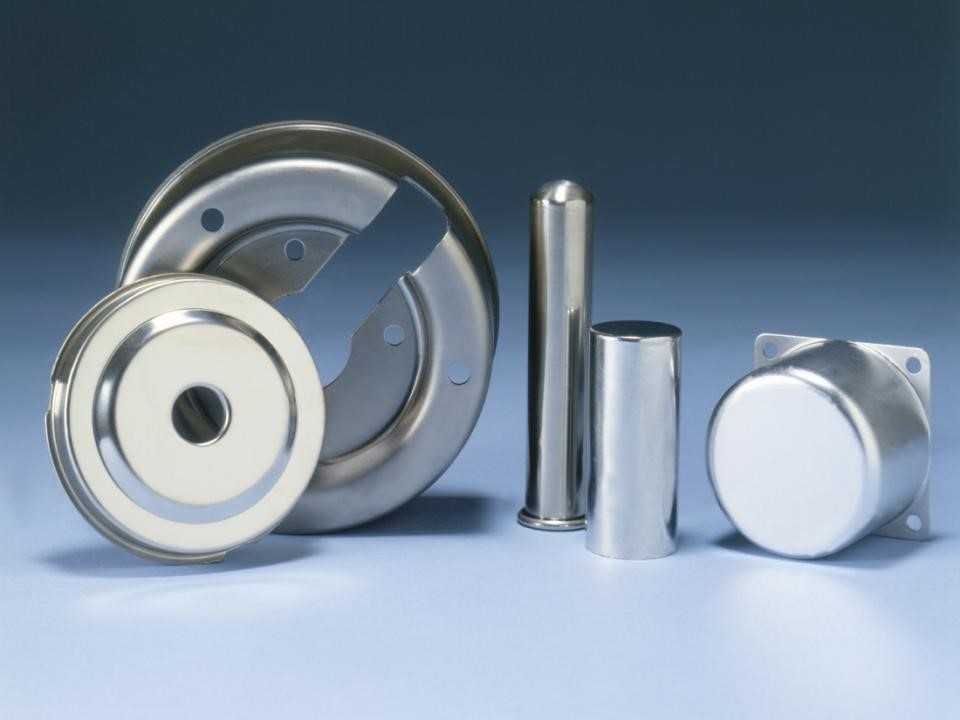
Factors to consider when specifying aerospace alloys
Even specifying a common alloy such as Type 301 series stainless steel can be a challenge because of the wide compositional range within the standard AISI chemistry. Stainless Type 301 (high tensile) will achieve a tensile strength of 270-300 ksi, but there is another T-301 composition at the other end of the spectrum, which work hardens relatively slowly, making it ideal for deep drawing applications.
Other grades of 300 series stainless can be just as versatile – and sometimes confusing. Stainless grades 309 and 310, for example, are high temperature alloys used mostly for furnace fixtures because of their high carbide and oxidation resistance. However, if the designer is looking for deep drawing properties, 309 or 310 will again provide excellent design choices. Both grades have the high alloy content that permits extensive forming.
For all but the most specialized applications, there are usually three or four compositional choices among the stainless steels and nickel-based alloys that will meet numerous combinations of corrosion resistance, wear resistance, tensile strength or high temperature cycling requirements.
Considering Yield & Tensile Strength in your specification
Indicating a tensile strength figure is appropriate for specifying castings, forgings and other heavier steel applications. It does not always work for many wrought strip products, such as stainless steel and nickel-based alloys.
In certain design situations, such as springs, yield strength may prove to be more meaningful than tensile strength. Yield strength approximates the theoretical point at which a material stops being elastic and becomes plastic.
Some alloys reach their yield point just before failure, others, reach it relatively early on the stress/strain curve. Specifying strictly by tensile strength does not do justice to alloys having a greater yield strength.
Another major concern of stampers is springback. This characteristic can also be controlled by annealing the material at specific points in the rolling sequence. However, springback is a function of the relationship between the tensile and yield strength of the metals and will vary among alloys.
It is also important to know how ductile the material needs to be for a specific application.
The Impact of Grain Size on Manufacturing
Grain size is important for fabricators because of its effect on forming or deep drawing of strip products.
If grains are too coarse or lack uniformity, sidewalls of deep drawn components may roughen up and “orange peel”. If the grains are too fine, the part may tear. When the appropriate grain size is not immediately available, it can be custom produced by thermal processing.
Smaller grain sizes create more uniform mechanical properties in alloys. They also alter hardness, tensile strength, yield strength, and the relationship between tensile and yield strength.
If there is a maximum yield strength specified, for instance, heat treating to attain a certain grain size must be controlled within the acceptable yield and tensile strength parameters.
The ASTM grain size code has a range from 0 to 13, the lower end of the range indicating coarser grains, the upper end, a finer grain. A typical specification for stamped parts is 7 to 9. Special processing will attain grain sizes beyond that range, but over 13 the steel is approaching non-recrystallisation.
Evaluating Annealing & Tempered Conditions
Annealed or cold rolled stainless steels are available in ¼ hard, ½ hard, full hard, and spring temper hardness which is referred to as extra full hard. These tempers are achieved by rolling specific area reductions on fully annealed material. The amount of area reduction required, and the resulting temper will vary among alloys.
Soft tempers are sometimes needed to withstand severe bends and accept deep drawing. As the temper increases so does strength, but formability is reduced.
With today’s advanced processing equipment and technology, some materials can be varied as much as 200 ksi over a range of tempers at any specified yield strength or tensile strength value.
It is possible to tailor stainless and nickel-based alloys to meet specific requirements even if they are beyond the ordinary specifications of the material. For example, Armco Steel’s 17-7 PH precipitation-hardening alloy is normally available annealed or in 60% cold rolled, Condition C. But it can be specially rolled in other forms, such as 1/2C and 3/4C. These grades are more formable than Condition C, but will precipitation harden with greater strength than the annealed condition.
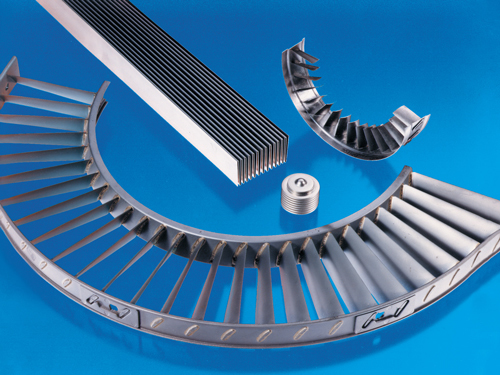
Specifying Metal Surface Finish for Your Application
Stainless and nickel-based alloys can be surface finished to impact cosmetic appeal, carry lubricant more effectively, or provide the additional surface area needed for good sealing or bonding.
Finish should be specified in microinches by either an RMS (root mean square) value or an arithmetic average of the surface roughness as measured by a profilometer. It is advisable to indicate the surface roughness within a range of acceptable finishes.
Remember, specifying nickel or stainless in your aerospace spec is all about flexibility.
Writing specifications that are somewhat flexible gives suppliers a chance to ferret out a solution rather than just saying ‘no’.
If the alloys are not available at the service center, they are readily obtainable from a re-roll mill.
Cold rolled steel and special metal re-rollers exist throughout the metal industry. But, in the stainless, nickel and cobalt-alloy market, they are especially important because these higher priced metals are expected to meet more stringent specifications that require extreme precision. Minute changes in metallurgy or surface finish can be a key factor in the success of many of these applications.
Written by Ron Brucker
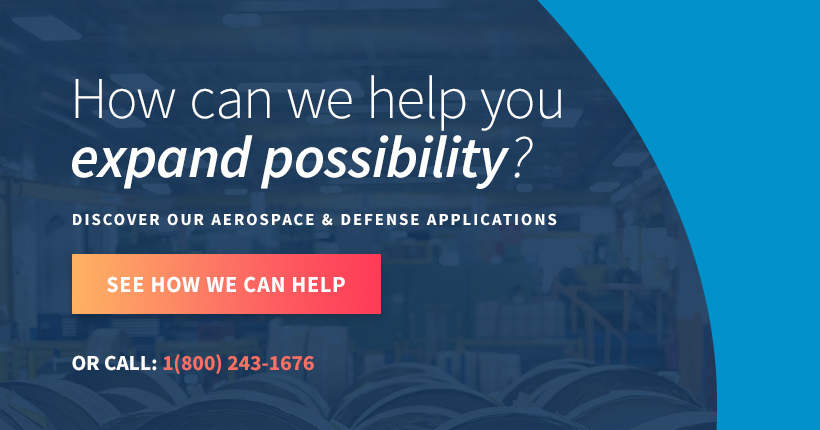