What Is Camber in Rolled Metal?
In the simplest terms, camber refers to curving. And in metalwork, this can sometimes be a good thing — think the curved steel beams of a bridge or the aerodynamic curves of a sports car. Steel remains strong, and sometimes even grows stronger, when bent.
However, in rolled metal manufacturing camber can be very problematic because subtle irregularities in material can have a cascading effect that drastically affects quality. This is why a steel rolling mill must control for camber in its process.
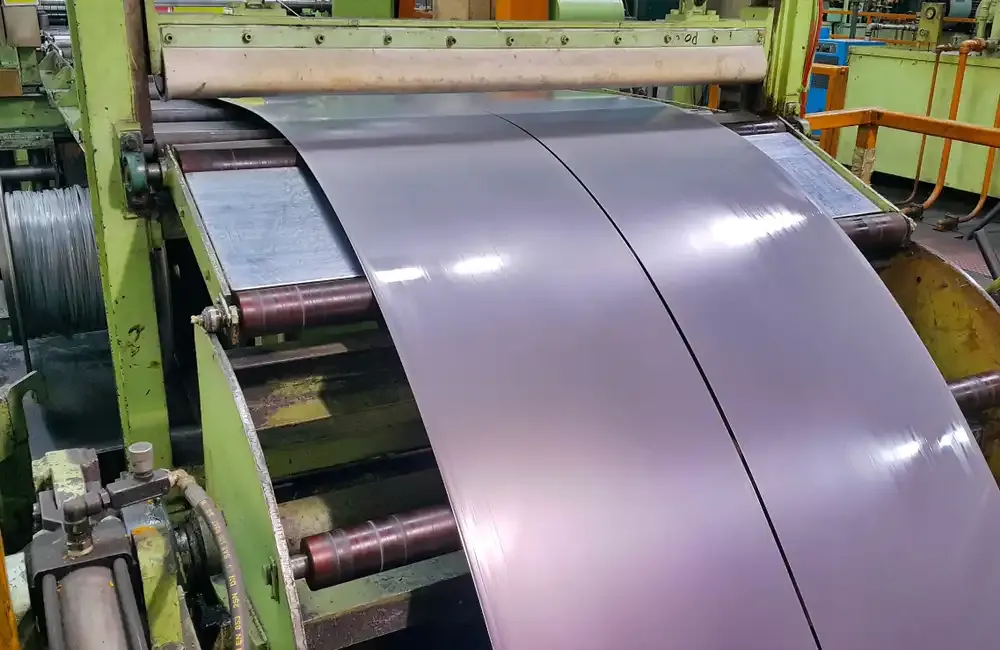
Effects of Camber on Rolled Metal
In rolled metal, camber is a curve across the plane of the sheet, whether down the middle or along one or both edges. Camber is measured by putting a straight edge next to the sheet. The greatest distance between the straight line and the sheet’s curve is the camber. A cambered sheet might be slightly thinner in the middle than on the edges (concave), thicker in the middle (convex), or thinner on one side (triangular). Any one of these can lead to costly machine malfunctions later on.
Typically, camber in sheet metal is caused by roll deflection, perforating, or cutting. Rolling direction and variations in the thickness of coiled steel can create problems. Improper camber in a sheet of metal makes it difficult to roll the sheet into a coil. And camber in a rolled coil makes it difficult to cut or shape the roll into pieces. Processing machines depend on consistent thickness for cutting, punching, and custom shaping or roll forming, so precision is key.
The Difference Between Camber and Sweep
Camber is a curve in the vertical plane or strong axis (hardway bending) of a metal beam or sheet. Imagine you’re looking at a beam from one end. The beam would be positioned like a capital “I.” Sweep is a curve in the horizontal plane or weak axis (also known as easyway bending). The end of the beam would look like a capital “H.”
Like camber, sweep can be created with heat, hydraulic pressure, or rolling to achieve desired mechanical properties for particular projects. And like camber, sweep can be used to add aesthetic interest, aerodynamic qualities, or strength to a vehicle, medical appliance, or skyscraper.
Controlling for Camber in Rolled Metal
The quality of coiled metal needed depends on its ultimate use. Higher-strength steel is prone to more camber issues but can be worth it in the long run. Ideally, a work roll of coiled steel should be perfectly flat. In reality, curves happen.
Camber can, however, be anticipated and corrected. Processers can use a corrective leveler to straighten a coil as it unrolls. With a series of horizontal and vertical rollers, the straightening machine creates a more uniform sheet before further processing. Since its vital to control the degree of camber for precision stamping and precision deep drawing applications, it’s important to obtain alloys from a metal expert that you can trust.
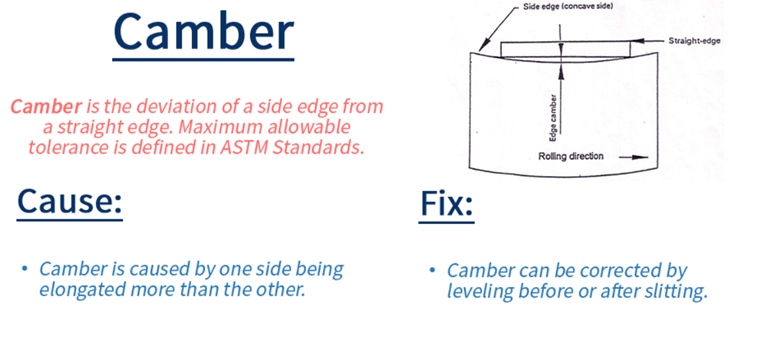
If camber isn’t corrected by a precision re-roller, it can cause a host of problems for their customers. For one, camber will cause the material to walk and oscillate in different directions when the coil is being fed through a machine. This is not a quality problem, but more of a manufacturing one that causes slowdowns and downtime.
Additionally, camber will release when a part is being manufactured from the cambered strip. Camber is more a difference in length and overall deformation of the material than anything else; the edges of the material have been rolled and lengthened either more or less during the rolling process.
What this means is that the outside of the strip is longer than the middle, so the only way to compensate for the difference in length is for the material to bend. When the material is slit, or a manufacturing process is undertaken that difference in directional stresses can release, which will cause directional differences in the parts. Some sides might be longer, thinner, or more deformed than others because the material has what we call residual stress, or stress that has remained in the material during processing that gets released as you take off more and more of the base material.
Trust the Metal Experts
For four generations, Ulbrich Stainless Steels & Special Metals, Inc. has been a global leader in precision metals. We produce an array of customized materials to meet unique demands for many industries. Our ability to deliver consistent product means customers get exactly the material they need. Contact us today.
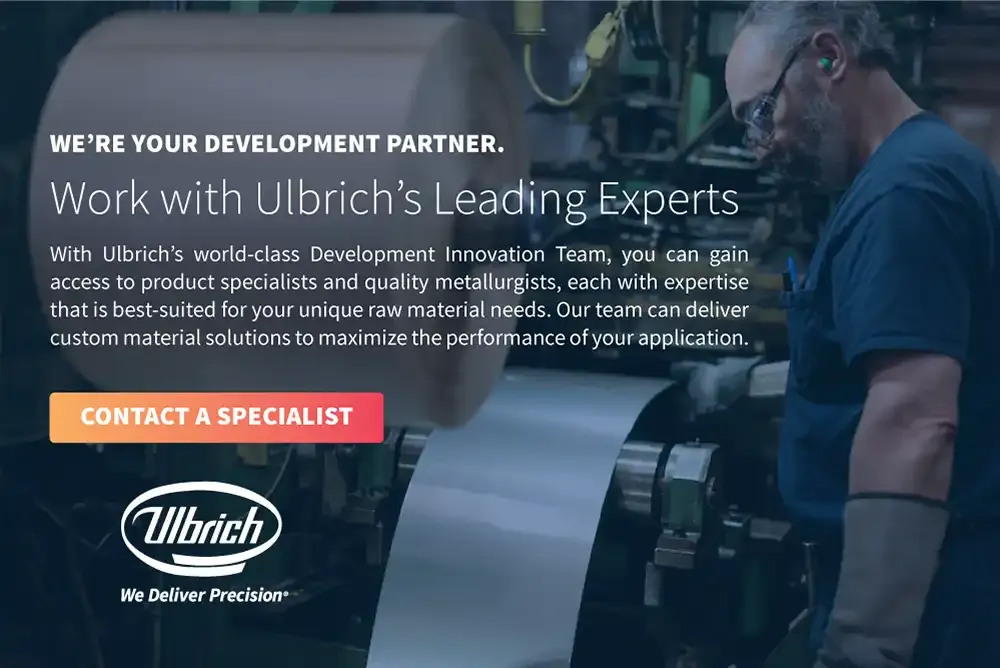