Rolling, Annealing and Slitting Stainless Steel & Special Metals: A General Overview
The Value of Our Steel Rolling Mill (USSM)
Ulbrich’s rolling division, USSM, provides engineered strip metal and foil products to exacting specifications. USSM produces a specialized rolled coil, not readily available from other suppliers. Our ability to deliver a customized and consistent product allows us to provide our customers the material they need to create enhanced processes and products. The strip mill’s diversity of equipment and experienced staff enables us to establish robust processes capable of supplying a precise and consistent product for use in a wide variety of applications across multiple industries.
Need to hold a tight gauge tolerance? Our standard tolerance is +/- 5% nominal thickness. However, we employ a combination of techniques and equipment, from the automatic gauge control system on our rolling mills to our meticulous sampling, and measurement at incoming inspection and final slitting, to ensure conformance to some of the tightest tolerances in the industry.
Need an exotic alloy or temper? Ulbrich offers strip or foil in over 160 alloys and we will work with our customers to develop, specify and supply a unique product to fit their manufacturing needs. Founded in 1924, USSM continues a long tradition of precision strip manufacturing in collaboration with our suppliers, customers, and a dedicated staff.
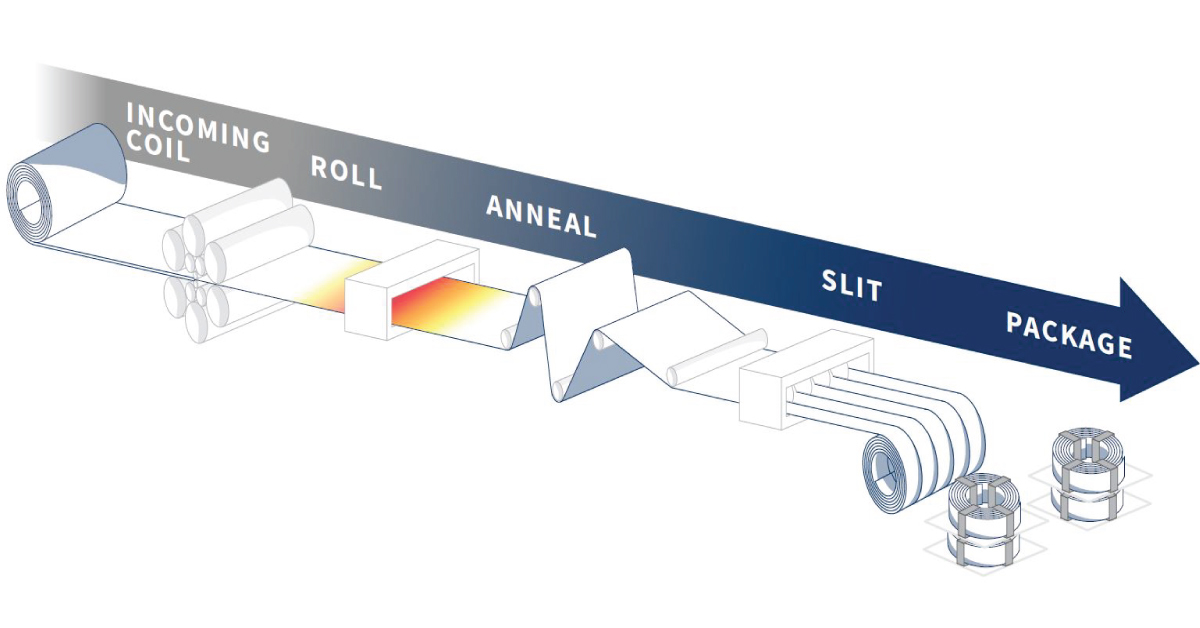
The USSM Manufacturing Process
USSM converts strip metal from widely available standard specifications to meet unique customer needs including: thickness, width, specific mechanical properties, industry specifications and many other critical characteristics.
The conversion process can be broken down into three basic steps:
1) Rolling: To reduce thickness
2) Annealing: To restore ductility
3) Slitting: To separate a wide strip into narrower cuts.
The rolling process generally begins with material in the annealed condition. The condition of metal (e.g. annealed, tempered) can be defined by the grain structure, or, microscopic structure (microstructure) of that metal. To the unaided human eye, most any metal surface looks continuous and homogenous. However, metals are actually made up of a network of individual microscopic crystals called grains, which can be viewed using a microscope on a polished and acid etched surface. The size, shape and alignment of these grains can tell us how the metal will behave, and will change in response to the various manufacturing processes the material is subjected to. Grains in annealed material are considered uniform and equiaxed: they are all very similar in size and shape with little directionality. Material with a properly annealed, equiaxed grain structure is ductile enough to be cold rolled to reduce thickness without breaking.
Rolling Steel & Special Metals
Cold Rolling is the cornerstone of USSM and the heart of the conversion process. Rolling is a continuous metal forming process in which metal stock is fed between two hard work rolls which apply enough pressure to plastically deform the metal, inducing a permanent reduction in thickness uniformly across the width of the strip. Rolling at USSM is considered “cold rolling” because we do not increase the temperature of the material before we roll it. Modern rolling practices employ a combination of screw down pressure, perpendicular to the strip surface, and longitudinal tension to ensure that the reduction in thickness translates exclusively into an increase in strip length instead of a reduction in strip width.
As the strip realizes a macroscopic reduction in thickness and increase in length, the grain structure is also changed. Rolling elongates grains in the longitudinal direction and, depending on the extent of the deformation, either partially breaks down or completely transforms the individual crystal structure of each grain. This microscopic modification from equiaxed to elongated grains translates into an increase in strength and reduction in the ductility of the bulk material. Strengthening the material through plastic deformation in this way is called cold working or work hardening. The more the thickness is reduced, the more the microstructure is changed and the harder and more brittle the material becomes until it cannot be reduced any further without breaking. Each alloy work hardens at a different rate and has a specific maximum amount the thickness can safely be reduced before it must be annealed.
Understanding the work hardening rate of a given alloy or heat lot within an alloy is paramount to achieving the mechanical properties specified by the customer. Process routings for tempered items allot a specific amount of reduction in thickness during the final rolling session, which is intended to work harden the material to the mechanical properties specified by the customer. An item ordered “Quarter Hard” will require a very small amount of reduction compared to a “Full Hard” item which would be rolled a reduction approaching the maximum the alloy can withstand without breaking. Generally, appropriate reductions are determined by analyzing a combination of historic data and chemistry.
USSM currently owns 8 rolling mills of three different configurations: 1 high-tech advanced 20-High mill, 2 Four High mills (H-mill), and 6 Sendzimir mills (Z-mill). H-mills are the simpler of the two, and use two large diameter work rolls which are driven and supported by a set of back up rolls situated atop and below, hence four high. The more complex Z-mills use three sets of cascaded back up rolls to focus the screw down force of the mill onto much smaller diameter work rolls. This roll cluster enables the Z-mill to apply a greater roll pressure without roll bending than an H-mill. Apart from differences in tooling, both H-mills and Z-mills operate in a similar manner. The operator can vary the screw down force applied by the work rolls, and the tension applied by the coil pay-off and take-up winders to achieve the desired amount of reduction for each pass. The equipment generally cannot provide enough force to induce the entire planned reduction at once; coils are rolled back and forth multiple times, or passes to achieve the desired reduction. USSM has been honing its rolling practices since Ulbrich purchased their first Z-mill in 1955 and first H-mill in 1957. Now, our largest H-mill can handle incoming material up to .187” thick, while our smallest Z-mill can roll foil as light as .00039″: an order of magnitude thinner than a human hair.
Annealing Metals in our state of the art annealing furnaces
The difference between the starting material thickness and the final ordered thickness of a given product is often greater than the maximum reduction an alloy can withstand without breaking. In this case, we must recover the equiaxed grain structure of material before we can roll any further. This is accomplished through annealing which may also be referred to as solution heat treating. The material is heated to an intrinsic critical temperature, and held at that temperature long enough for the microstructure to essentially reset. The thermal energy introduced by the furnace allows the grains to recover from the effects of the work hardening introduced during rolling, at which point the metal will re-crystallize, or precipitate all new equiaxed grains. The grains start very small, and grow in size over time. You may refer to the earlier post “Stainless Steel Grade Selection for Strip, Foil and Wire” for further information on the preferred grain size for various applications. Our anneal cycles are designed to begin cooling down the material immediately after the grains re-crystallize to avoid excessive grain growth. If grains are grown too large, the bulk material may exhibit erratic mechanical properties or an undesirable surface finish. Once the equiaxed grain structure has been restored, the strip is ready to be rolled again. This rolling and annealing cycle can be repeated as many times as necessary to reach the final ordered thickness. On products ordered in the annealed condition, no subsequent rolling is needed.
USSM exclusively performs continuous bright annealing using either gas fired muffle tube or electric furnaces. This method of annealing is considered continuous because the strip is fed end to end through a furnace instead of batch heated all together in coil form. The coil is mounted on a payoff winder which feeds the strip through the furnace where it is heated to the desired temperature and then air cooled before being re-accumulated into coil form on the takeoff winder. The furnace temperature and feeding speed are controlled in order to introduce enough thermal energy to re-crystallize the material and achieve the desired grain size. Continuous annealing allows for greater control of the strip temperature than a batch anneal. Proper strip temperature control will result in more uniform mechanical properties and grain structure throughout the entire length of a coil. Our annealing is considered bright because the entry and exit of the furnace are sealed and the interior is filled with a shielding gas. In open annealing, which is not performed at USSM, the hot material is exposed to air which results in a scale forming on the surface of the metal. Subsequent chemical processing is required to remove the scale from the surface. Bright annealed material does not require chemical processing because no scale is formed. The protective atmosphere inside the furnace prevents the formation of excess oxide and allows the strip to retain its rolled finish.
Slitting metal with tight tolerances and edge condition
Slitting, the mechanism we employ to separate a wide strip into “mults” or narrower strips, is a method of continuously inducing fractures in a straight line along the edges of the desired width. The strip is fed through an “arbor” containing two sets of hard, rotating tool steel “knives”. These knives penetrate deep enough into the strip to weaken the adjacent material to the point of fracturing. The slit mults continue from the arbor to a re-coiler where they are accumulated back into coil form. The depth of penetration, or, clearance, of these knives is closely monitored, as the burr on the edges of the mults will vary with the clearance. USSM standard #3 slit edge maximum burr is 10% of product thickness. Our operators will make adjustments to the clearance as they are preparing to slit in order to minimize the burr as much as possible.
Slitting can serve as both the initial and final operation in the conversion process at USSM. All of the slitters at USSM are similar in concept and operation, but vary greatly in size. Our larger machines are dedicated to slitting the heavy gauge incoming coils up to 54″ wide to mults used for re-rolling. At the other end of the process, slitting is used to separate a material at finish gauge and temper into the width ordered by the customer. Many considerations regarding coil configuration must be made during a final slitting operation as the output is often a coil in delivery condition. Apart from width: edge condition, coil support, coil inner diameter, coil size, interleaf and accumulation method are all characteristics of the final product that are realized during final slitting. Once a coil is slit to final width it can be packaged and delivered to the customer.
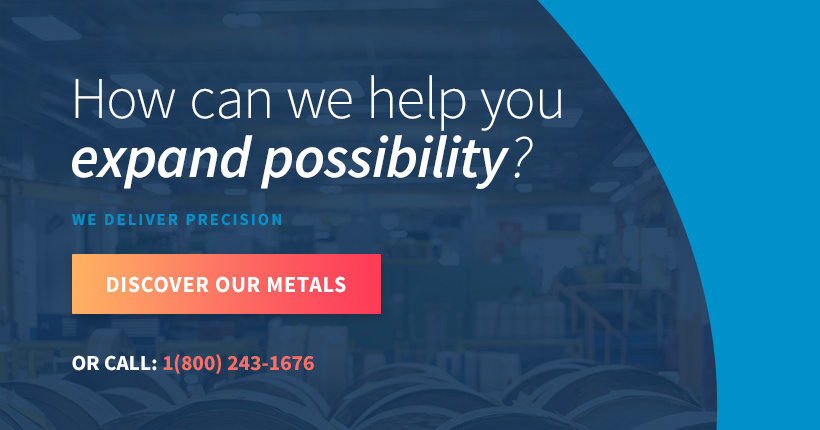