What are the Most Common Forms of Metal Corrosion?
Corrosion is a natural phenomenon that affects nearly all metal objects we use in our everyday lives. Automobiles, aircraft, medical instruments, buildings, infrastructure, appliances, and energy distribution systems are all comprised of metal, and thus all of them can corrode.
We’ve all had that one car. Yes, the automotive incarnation of the Ship of Theseus that we’re pretty sure doesn’t exist anymore. Thanks a lot, corrosion!
Corrosion comes in various forms, and usually corroding components made of metal will suffer from more than one form at the same time. The mix of metals used in a component and the wide range of environments it is exposed to often provide opportunity for more than one form of attack. In certain environments, metals may be exposed to various types of local corrosion including pitting, crevice, intergranular, stress, and galvanic corrosion. Even a single alloy can suffer from more than one form of corrosion depending on its exposure to different environments at different points within a system.
The length of time, overall conditions, and level of exposure to corrosive environments can all influence the rate, severity, and type of the resulting corrosion.
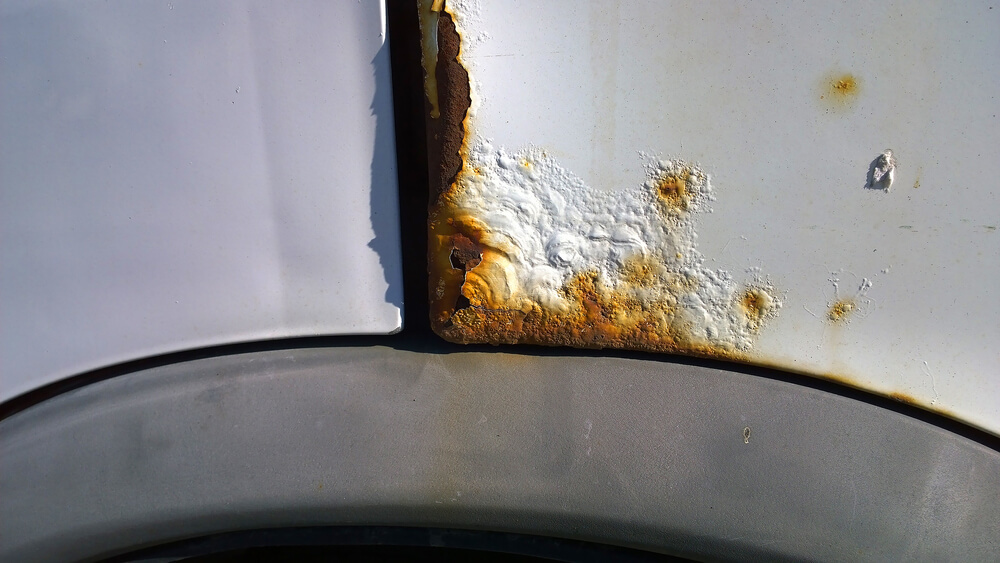
What is metal corrosion?
Corrosion is the deterioration of a material as a result of chemical reactions between itself and the surrounding environment. Although corrosion affects materials other than metals, including polymers and ceramics, the term is most often associated with the degradation of metals.
Why do metals corrode?
Most metals do not occur naturally in their metallic state, it takes energy (being put into a blast furnace) to separate these metallic elements from the compounds they comprise in nature. Because entropy increases and free energy must decrease, the atoms that comprise a metal in its metastable state want to return to the stable condition which required the lowest energy to maintain. Corrosion is the return of the energy used to extract them from their original low-energy (ore) state through oxidation.
This is achieved through an electron exchange which occurs between a metal and its environment.
During corrosion the metal is usually losing electrons, becoming oxidized, while the environmental substances acting upon it gain electrons, becoming reduced.
This reaction is both spontaneous and electrochemically favored.
Unfortunately for metals almost all environments will cause corrosion to some degree because the corroded state is the more stable state.
What are the most common types of metal corrosion?
Corrosion is classified by the way in which it displays. Its various forms are grouped based on the appearance of the corroded metal with corrosion forms identified by visual observation. In most cases the naked eye is sufficient, but sometimes magnification is helpful or required. NACE, the authority on corrosion, categorizes corrosion into 3 groups. These groups are:
- Group 1: Corrosion determined by visual observation
- Group 2: Corrosion needing additional means of examination
- Group 3: Corrosion requiring microscopic verification
Within these groups, there are many specific types of corrosion that can occur. The following are some of the most common.

1. Stress Corrosion Cracking
While looking at your part with an eyelet, you notice small, hairline fractures visible on the corners. This is a telltale sign of a notoriously bad form of corrosion, stress corrosion.
Stress corrosion occurs while material is in a corrosive environment and tensile stresses are present. All metals have different tensile limits/ranges, and the closer to the height of this limit the more likely it is for stress corrosion to occur. An example includes any processes that include High/Low temperature changes/cycles. It is very important to make sure that this is accounted for during the of R&D phase while choosing the correct alloy for your application.
2. Pitting Corrosion
Upon inspection, someone in quality notices small cavities within the material as well. Although the stress corrosion cracking is also present, this shows tell-tale signs of a much more dangerous type of corrosion: pitting.
These small, deep cavities can be caused by a variety of different factors. A few examples are poor coating application, film damage, or from foreign deposits within the metal itself. Nevertheless, pitting can cause very quick and devastating failures if not caught early in the life cycle of the manufacturing process. In spots where this film (passivity) has been broken, moisture has the potential to enter and cause corrosion cells. This creates an increased risk of failure within the material itself, as there are multiple points where the material’s grains do not have structural rigidity.
3. Erosion Corrosion
One of the more commonly occurring entries on the list, erosion corrosion occurs when a corrosive liquid runs across a metal, thus creating an accelerated deterioration of that metals surface. This type of wear on metals is usually visible to the naked eye, creating grooves, craters, or valleys on the surface of the material.
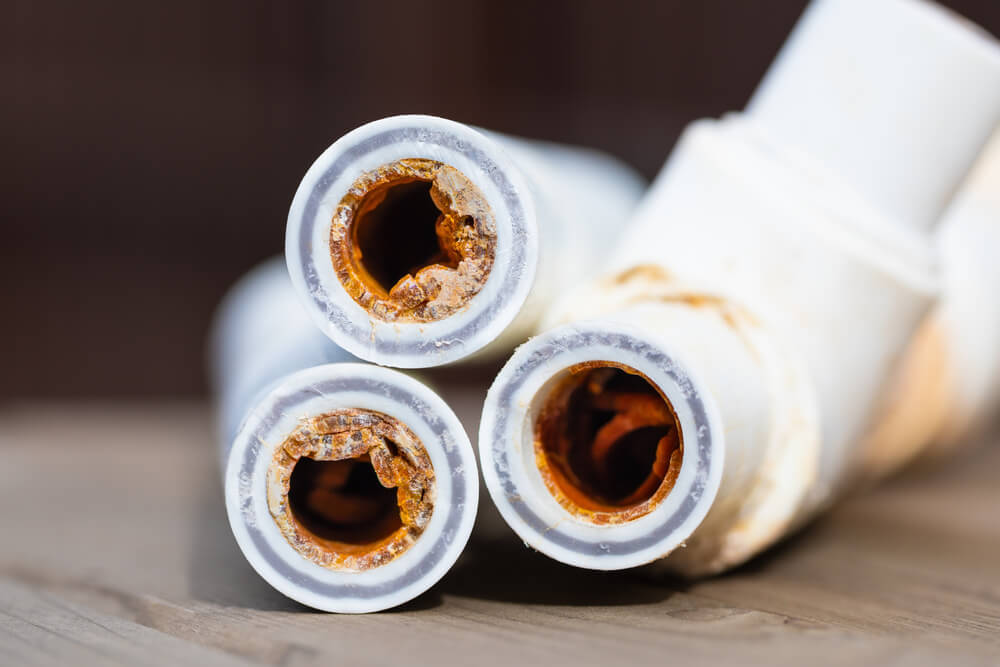
How does this work? Ions on the materials surface are literally being swept away by the force of the corrosive liquid running on it. This leads the material to be much more susceptible to damage by removing film and penetrating the metal itself. Like many of the other forms of corrosion, the timeline for this breakdown is dependent on many factors.
If you have questions about your unique material needs or the processes you perform on metal you buy and want to understand the most likely factors that will cause this type of corrosion in your application, Ulbrich’s team of Metallurgists can assist.
4. Crevice Corrosion
As the name states, this type of corrosion is formed inside gaps or crevices on the surface of the metal. Crevice corrosion can also affect anything that the metal is ‘connected’ to; welded metal on metal, or even metal attached to non-metal objects.
These crevices most often get filled with contaminates that accelerate the speed of the corrosion process. Water (usually stagnant) is the biggest suspect to look out for. This water is the catalyst in causing the electrochemical reactions that will eventually lead to the breakdown and failure of the material.
5. Selective Leaching
Picture this: You are looking to build a new tool for your shop and use a scrap piece of stainless steel that was lying around to make a funnel for liquid to run through. This fluid constantly running through the funnel. Over time, you notice that there are small flakes of metallic material in the fluid coming out of the other side. After looking into the inside of the funnel, you realize that the fluid running through the funnel is causing grooves and divots throughout the inside surface. This is an example of denickelification; a form of selective leaching that causes nickel to be specifically stripped from other elements in the alloy.
Selective leaching corrosion occurs when only one (or more) elements in an alloy become deteriorated. When this deterioration starts, the alloys begin to separate from one another molecularly. Due to the history and conditions of use, your funnel has now started to show signs of selective leaching. In this case, causing the nickel in the Stainless Steel to be stripped away as the other metals of the alloy remain. A situation like this can be prevented by heat treating material to make it more resilient, as well as conducting further research on how the fluid may cause chemical reactions to occur on stainless steel. This can be an important factor to consider when working with duplex alloys.
6. Uniform Corrosion
A very common example of uniform corrosion that most can recognize, especially those of you who bought a Mazda6 between 2005 and 2008, is rusting! This type of uniform corrosion attacks the entire surface area (or large amounts) of the specified material. It is very much visible to the naked eye.
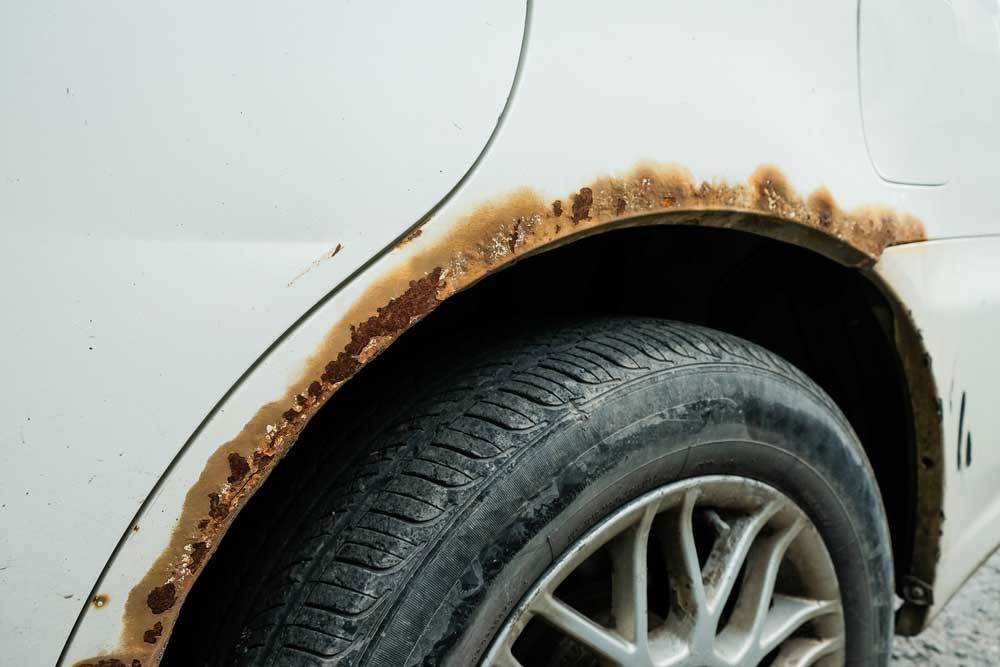
This corrosion will cause the metal to slowly lose it’s ‘thickness’ and break down, dissolving it bit by bit. It will eventually cause the metal to become brittle, and break.
Think about the wheel wells and front edge of the hood of your old 2008 Mazda6. If you live anywhere where its rained more than once since the 2008 model year, you now see brown and brittle flaking metal. You have a real-world example of uniform corrosion! Typically, this is caused by chemical or electrochemical reactions. Uniform corrosion is known as one of the MOST common types of corrosion.
7. Intergranular Corrosion
As many Engineers, metallurgists, and others who work closely with the chemistry of metals know, Metal is made up of billions of ‘grains’. These grains are what affect the rigidity and strength of the metal itself. If intergranular corrosion occurs, then the physical structure that holds the metal together (the grains) is becoming compromised.
As an example, austenitic stainless steels are usually susceptible to intergranular corrosion when going through the heat treatment process. These boundaries that are created when improperly heat treated can cause dire consequences in the future, so it is important to know the data on mechanical properties when considering alloys for your application. The condition results in preferential or unacceptable corrosion to grain boundaries reducing material bulk strength which can result in premature material failure.
8. Galvanic/Bimetallic Corrosion
When two metals that are dissimilar are in contact for long periods of time, bimetallic corrosion occurs. The difference in electrode potentials between the metals causes a cell called bimetallic couple. The bimetallic couple cell causes one metal to act as a cathode and one as an anode.
The further that two metals are from each other in the galvanic series, the larger the potential impact could be regarding Bimetallic corrosion of the two materials.
What can you do to prevent corrosion in metals?
The science of corrosion prevention and control is highly complex. This complexity is only exacerbated by the fact that there are many different forms of corrosion which are affected by a wide array of external factors. To ensure long and trouble-free operation of the products your organization manufactures, it is of utmost importance to work with metallurgically savvy partners who have knowledge about corrosion and the effect it can have on the materials in situ within the operating environment. Component failure, and a significant amount of material damage caused by corrosion can be eliminated by selecting the appropriate alloy and characteristics for a given application.
The primary contributors to the corrosive effects of liquids and metals are:
- Oxygen, chloride and/or sulfide content
- Temperature
- pH - value
Preventing corrosion includes the following strategies:
- The selection of appropriate materials
- The engineered design of the product
- Employing protective methods (coatings, anodes, etc.)
- Proper component installation & maintenance
- Employing best-in-class research, development, and testing
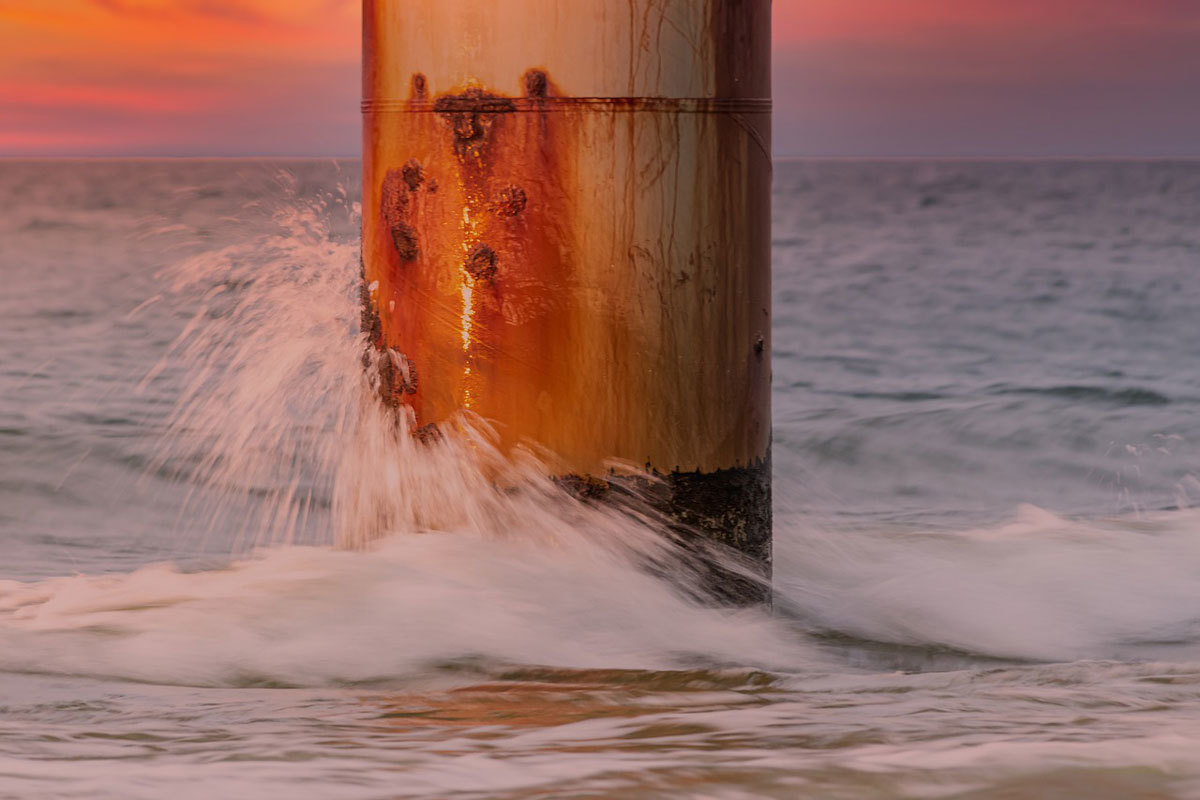
Choosing the right alloy with the ideal chemical composition for your job is key to preventing corrosion. In the case of a stainless steel grade containing at least 11% chromium, when that metal is exposed to an oxygenated environment, the chromium will react with the air to form a passive oxide layer on the metal’s surface. This slows further oxidation and helps the metal to resist uniform and local corrosion. Other elements provide anti-corrosive effects as well. For example, nickel helps to stabilize the microstructure, increasing resistance to stress corrosion cracking. Manganese, in moderate quantities and in association with nickel helps prevent pitting. The addition of molybdenum adds even more resistance to pitting as well as crevice corrosion.
Here at Ulbrich, our team of expert metallurgists have seen it all. Engineer to engineer communication between manufacturers and their reroll partners or metal suppliers are key to overcoming the challenges of metal corrosion. If you’re working on a part or product where resistance to corrosion is critical and would like to lean on us for some assistance, we’re here for you! We’ve helped countless partners producing parts for some of the most challenging applications to identify the right alloy for the job. If you need help selecting a corrosion resistant alloy and want to learn more about the characteristics to look for in order for it to withstand the conditions it will be exposed to, reach out and speak with one of our engineers today!
We also have data sheets on our website which provide details to help you expand your knowledge on our wide selection of alloys.