An Unsung Hero: Producing Wrap Wire for Resonant Guitar Strings
This article originally appeared in an issue of Music Trades Magazine as "Ulbrich Steel - An Unsung Hero"
Producing wrap wire for most of the industry’s guitar and violin strings, Ulbrich’s metalworking expertise is a key component of stellar tone.
When guitarists analyze the source of great tone, they may point to tonewoods, strings, vintage designs, and the luthier’s art, but odds are, they never mention Ulbrich Stainless Steel & Special Metals. An unsung hero of the music industry, Ulbrich is a diversified metal processing firm that produces much of the wrap wire used in wound guitar strings. The company also produces wire for violin strings and speaker and microphone coils, making it one of the more important companies in the industry that no one has ever heard of.
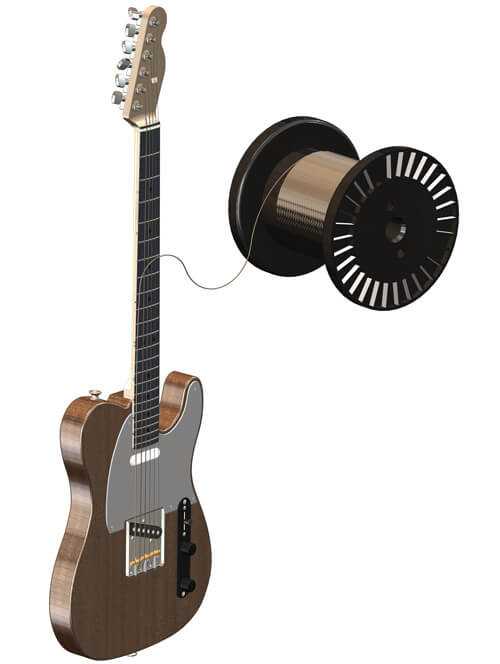
With over 700 employees in operations around the world and sales in excess of $450 million, Ulbrich has created a thriving business tailoring metal and wire components for highly specialized applications. Ulbrich wire can be found in solar panels, telecommunications equipment, the Space Shuttle, medical devices, and other applications too numerous to list here. The metallurgical skill and technology that allows the company to draw wire to ultra-fine dimensions have been applied to create the wire that gives guitar and violin strings just the right feel and resonance.
Everyone in the music industry agrees on one thing: the perfect string does not exist. One individual string cannot suit every instrument. If this has happened in the past, it was simply a matter of lack of choice. From a conceptional standpoint, modern strings are basically produced the same way they were a long time ago. The only difference is that today there is a larger variety of materials. With a few exceptions, all modern strings share the same basic construction: a gut, synthetic, or stranded-steel core, often covered by some form of damping material, wound (wrapped) with ribbons of metal.
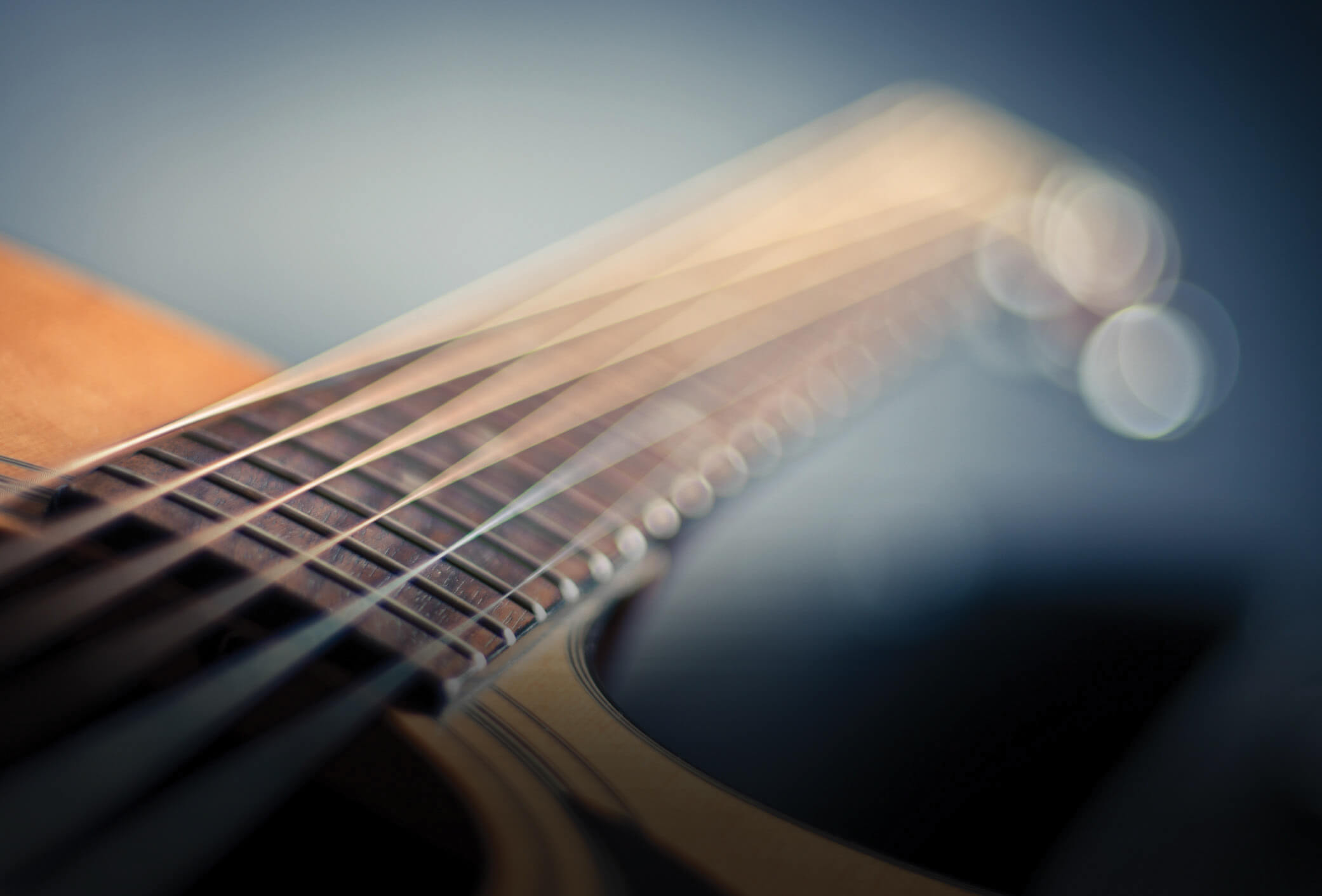
The Ulbrich Specialty Wire Products facility in Westminster, South Carolina, produces an assortment of string wrap wire. Varieties include aluminum and tungsten wires for bowed instruments as well as brass, bronze, nickel-plated steel, and stainless-steel varieties that can be offered bare or electroplated (with silver, gold, nickel, or tin) for guitar strings. Wrap wire is also produced in round, half-round, and flat configurations, and in numerous gauges. Producing this essential music raw material involves drawing a relatively thick piece of wire through a series of dies to reduce its original diameter by as much as a factor of ten or more. The drawing process realigns the molecular structure, making the wire harder and less ductile. To counteract this and restore the proper flexibility, or “ductility” in metalworking terminology, requires a heat treatment known as annealing.
Simple in theory, the practice of calibrating the drawing and annealing process to achieve the perfect balance between tensile strength (how much force is needed to break the wire) and ductility requires a combination of art and science. Mastery of this skill is the foundation for Ulbrich’s success.
"Mechanical properties and process controls are essential, said Sergio Sensini, Ulbrich Product Manager. "But ultimately, how good the strings sound are what our customers test for and really care about."
The origins of this broad-based metalworking expertise date back to 1924 when Fred Ulbrich opened a scrap metal yard in Wallingford, Connecticut. In the ‘30s he expanded the company by purchasing a rolling mill to produce stainless steel cutlery. During World War II Ulbrich made hundreds of thousands of stainless-steel knives for mess kits. Competing with much larger cutlery manufacturers, in 1950 Ulbrich exited the business to focus on rolling precision stainless steel parts. Since then, the family-owned business has branched out into specialized wire and a host of other precision metal products. Currently, under the leadership of Fredrick Christian Ulbrich, grandson of the founder, Ulbrich Stainless Steels & Special Metals continues to pursue all markets around the world that require precisely formed metal parts.
Critical Attributes of Music Wrap Wire:
- Wrap Quality
- Tonal Quality
- Cosmetic Appearance
- Cleanliness
- “Feel”
- Lead Times
- Pricing
Ulbrich’s Competitive Advantages:
- Wire Roundness – OOR Tolerances
- Tightly Controlled Width Variation
- Consistent Physical Properties (Process Controls)
- In-House Drawing, Rolling, Annealing & Plating
- Diverse Product Line
- Inventory Management and Customer Service
- Packaging Options
Alloys include:
- 2% & 1.25% Silver Plated Copper
- 2% & 8% Nickel Plated Steel
- 430 Stainless Steel
Contact us to learn more about our wrap wire capabilities and how we can help you produce better-sounding guitar, violin, and other instrument strings.
Information provided by Sergio Sensini, Product Manager at Ulbrich Specialty Wire Products.