Is this Foil, Strip, or Ribbon? What’s the Difference, Really?
If you work in stamping or deep draw manufacturing, you've probably heard the terms foil, strip, and ribbon used to describe flat metal coil. Maybe you’ve even used them interchangeably in conversation or RFQs. And truth be told, so have we.
That’s because different people, different industries, and different generations have found their own ways to talk about the material that runs through their presses.
But when you’re sourcing high-precision coil for a demanding application—especially when tolerances are tight and tooling is expensive—it helps to understand what these terms usually mean, how they’re used, and when the differences actually matter.
This isn’t about being precise for precision’s sake. It’s about avoiding surprises, protecting your process, and helping your team get exactly what they need.
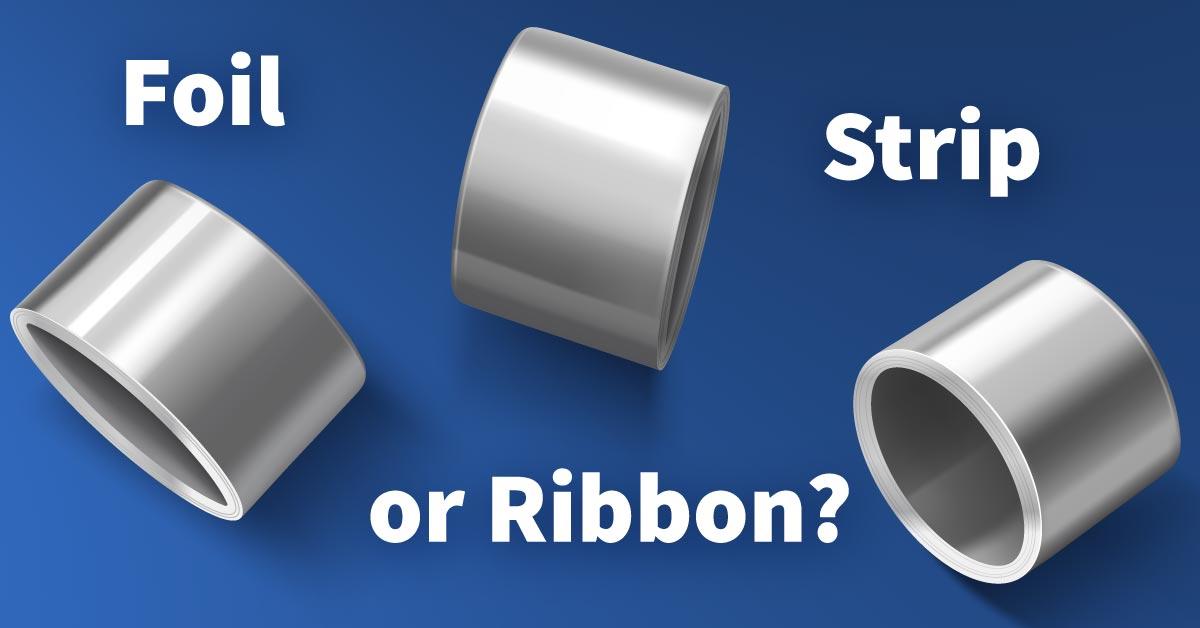
So, What Is the Difference?
Let’s start by demystifying the terminology. These aren’t hard and fast rules but by breaking them down we can start to create a shared language.
Foil usually refers to metal under 0.005" thick. It’s ultra-light, highly formable, and often used in medical components, shielding, and other micro-scale applications. It handles differently on a press because of how thin it is. And, because of how sensitive it can be to surface damage or tension issues.
Strip, on the other hand, typically ranges from 0.005" up to around 0.125". This is your workhorse material—the stuff running through progressive dies, transfer tools, and deep draw operations. It’s engineered for consistency, strength, and repeatability. It might look simple, but good strip is anything but basic.
Ribbon is the wildcard. It isn’t about thickness, it’s about shape. When someone says ribbon, they’re usually talking about narrow, flat material—often with a specialized edge condition or dimensional profile. You’ll hear it more in fine wire, electrical, or transformer applications, and sometimes from legacy drawings or long-time toolmakers.
Now, if you call something ribbon and we call it strip—it’s not a problem. What matters most is the dimensions, tolerances, and performance requirements. As long as we’re aligned on those, we’re speaking the same language.
Term |
Typical Thickness Range |
Key Characteristics |
Foil |
< 0.005" (0.127 mm) |
Ultra-thin, lightweight, used in EMI shielding, fine medical components |
Strip |
0.005" – 0.125" (0.127 – 3.175 mm) |
Engineered for strength and precision in progressive or deep draw stamping |
Ribbon |
Not gauge-specific; typically refers to narrow width flat material |
Often edge-conditioned or rounded; used in fine wire and transformer components |
Why Understanding These Terms Still Matters
Knowing what someone probably means by foil, strip, or ribbon helps ensure your RFQ gets off on the right foot. But more importantly, it helps us help you when the application calls for something more nuanced.
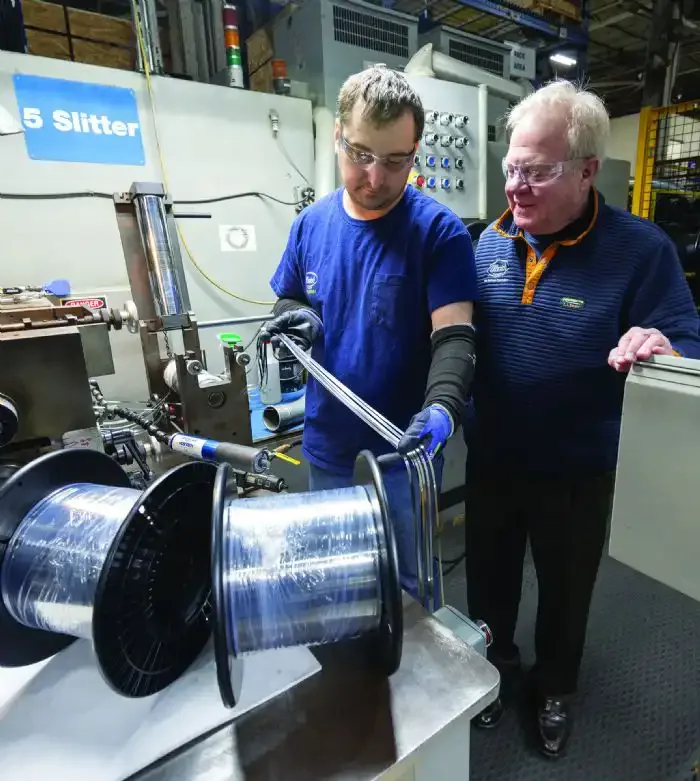
Let’s say you need 0.0045" thick stainless with a rounded edge. Technically, that’s foil—but if you tell us it’s for a progressive die running 400 strokes a minute, that changes how we approach the edge, the temper, and how tightly we control camber and flatness.
Or maybe you’ve asked for “ribbon” at 0.020", 0.250" wide. What you really need is narrow strip with precision edge condition—something we can produce by rerolling and slitting from master coil to meet both the width and edge performance your tooling expects.
This is where the conversation becomes more important than the terminology. It’s about what the material needs to do, not just what it’s called.
A Quick Word on Tolerances, Burrs, and Setup Sensitivity
At Ulbrich, we’ve walked the floor with plenty of stamping teams that were running good tooling, on good presses, with the right material—and still getting inconsistent results.
The culprit? Tolerance stacking.
When your strip gauge varies too much, even within spec, it can throw off stroke depth, increase burr height, or cause parts to stick in the tool. Multiply that across 20 stations and you’ve got a real mess: cracked parts, misfeeds, and operators scrambling to adjust mid-run.
The same goes for edge condition. A strip with a sharp, square edge might work fine in one application but act like a blade in another—scoring the die or chewing through feed guides over time. It’s not that the material is wrong, it’s that the spec didn’t reflect what the tooling really needed.
That’s why we treat every RFQ like a conversation. We ask about stroke rate. Form depth. Burr control requirements. Because the more we know about your application, the better we can engineer material that performs—not just material that meets a spec sheet.
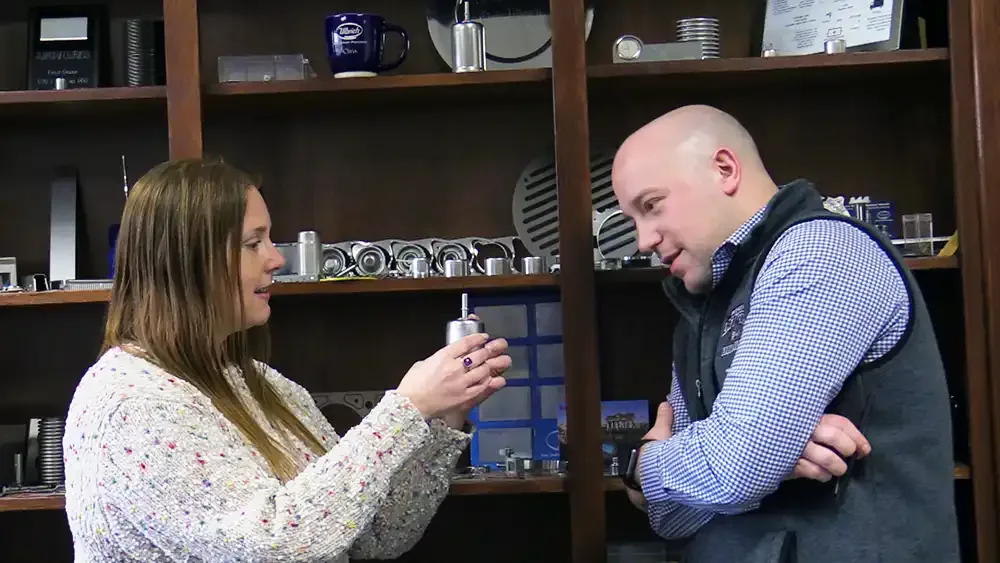
How We Help You Get the Right Material
No Matter What You Call It
We’re not here to police your vocabulary. If you call it ribbon, we’ll know what you mean. If you ask for foil, we’ll still double-check what your tooling is expecting. That’s part of our job—to translate intent into precision.
But what we do care about is:
- What your material needs to do in the press
- What kind of tolerances your parts are built around
- What edge conditions your tooling likes—and what it hates
- Whether your operators are adjusting the press to compensate for material, or the material is supporting them to run at full speed
Our goal is to help you design a process where the coil is invisible—in a good way. Where it feeds cleanly, forms consistently, and lets your team focus on output, not workarounds.
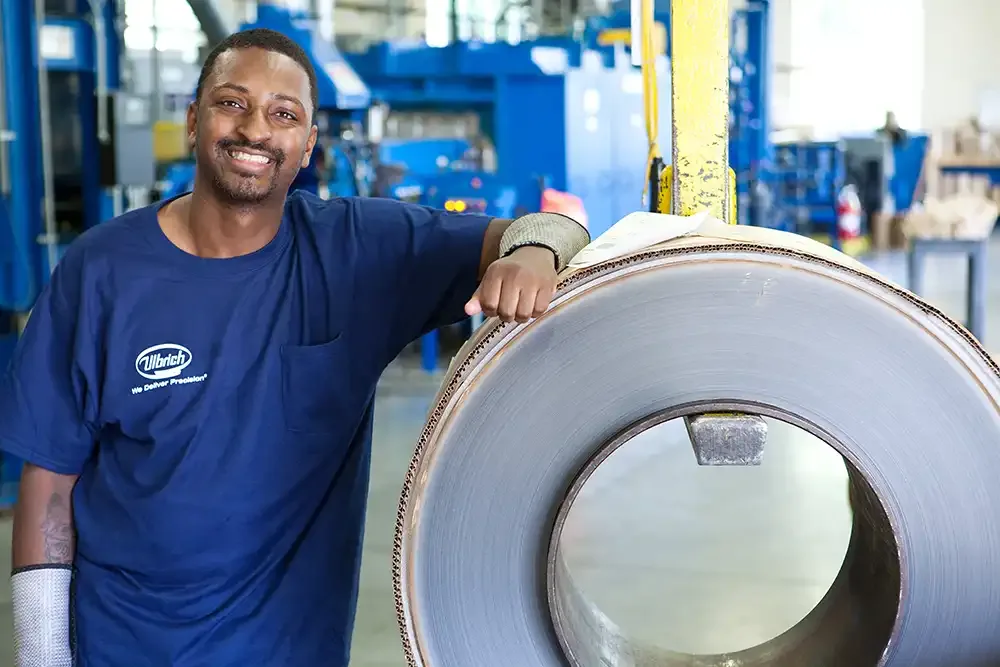
Final Thought: Speak How You Speak and We’ll Handle the Rest
If you take one thing from this article, let it be this:
You don’t need to memorize definitions. You just need a supplier who listens carefully, asks good questions, and delivers material that works the way your press was meant to run.
That’s what we do at Ulbrich. Because in precision manufacturing, getting it almost right isn’t good enough. You need to know the coil you’re getting is going to perform, from the first hit to the last.
So, whether you call it foil, strip, or ribbon, talk to us. Let’s make sure your next run is smoother, faster, and more predictable than the one before it.