Ferritic Stainless Steel: A Useful Overview of Ferritic Steel Grades
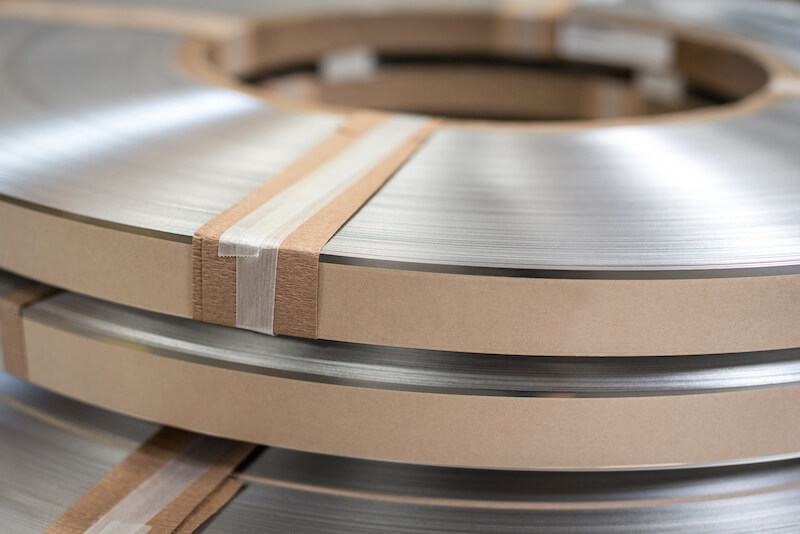
What is Stainless Steel?
Stainless steel differs from other types of steel in that it contains chromium, nickel and other alloying elements that give it a far superior degree of corrosion resistance. Within the world of stainless steel, a staggering amount of variation exists, with well over 100 unique grades currently available. Most of these grades fall within five broad categories:
- Austenitic Stainless Steel
- Ferritic Stainless Steel
- Martensitic Stainless Steel
- Duplex Grades
- Precipitation-Hardening Stainless Alloys
Each of these types of stainless steel possess a unique set of metallurgical attributes. Naturally, different types have different strengths and weaknesses in terms of potential applications. This article takes a closer look at ferritic stainless steel, outlining some basic information about how ferritic steel is graded, and what sets it apart from other varieties of stainless steel.
What is Ferritic Stainless Steel?
Ferritic steel is a grade of stainless steel alloy containing more than 12% chromium and differs from other types of stainless steel in two crucial regards: its chemical composition and its molecular grain structure. Here are some of the key things you should know about each of these differences.
Ferritic stainless steel is really defined as a straight chromium non-hardenable class of stainless alloys which have chromium ranging from 10.5% to 30% and a carbon level under .20%. These steels are essentially non-hardenable by heat treatment and only slightly hardenable by cold rolling. Some ferritic stainless grades are:
- Type 409 Stainless Steel
- 430 Stainless Steel
- 430LI Stainless Steel
- 434 Stainless Steel
- 439 Stainless Steel
- Type 442 Stainless Steel
- 444 Stainless Steel
- 446 Stainless Steel
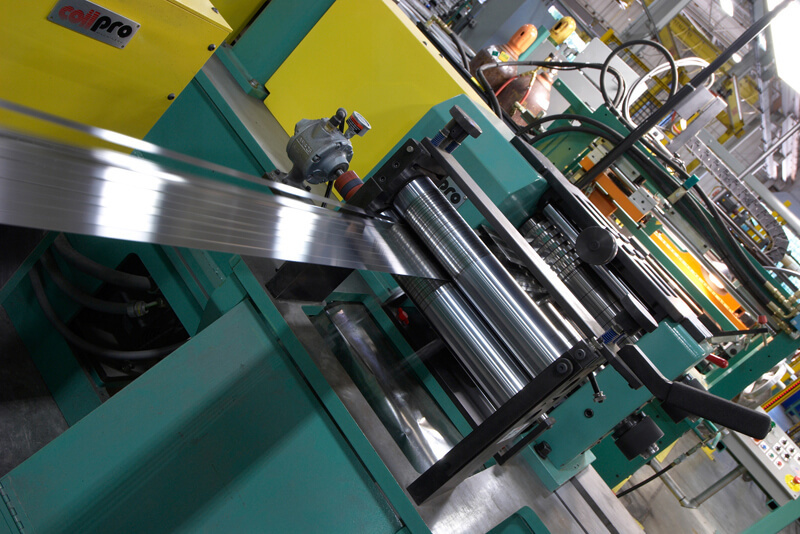
What is the Chemical Composition of Ferritic Steel?
As noted above, all stainless steel incorporates the metal known as chromium, which is noteworthy for its hardness, corrosion resistance, and exceptional gloss when polished. Ferritic steels are unique in that they usually contain higher levels of chromium than other type of stainless steel.
For instance, one of the most common types of austenitic steel — so-called 18/10 stainless — contains 18 percent chromium — but unlike austenitics, it contains no nickel. Ferritic stainless steels, by contrast, may contain chromium levels as great as 27 percent. That said, not all types of ferritic stainless steel contain such high amounts of chromium; some may even have less than their austenitic counterparts.
A more universal difference between ferritic and austenitic stainless steels is that ferritic steels contain little if any nickel. Ferritic stainless steels share this trait with martensitic stainless steels, most of which also contain no nickel. Finally, ferritic steels are characterized by the fact that they contain only small amounts of carbon.
About the Ferritic Grain Structure
The particular composition of a stainless steel plays a large effect on how the metal is structured on a molecular level. Those structures are even what give the different types of stainless steel their names. Ferritic steels, in other words, are characterized by the fact that they are made up of the microstructures known as ferrite.
Ferrite is a metallurgical phase of iron in which metallic alloying elements are in solid solution, but carbon is essentially insoluble. Ferrite is virtually absent in quenched martensitic and austenitic stainless steels, but its presence characterizes stainless steels. Its also important to note that annealed martensitic stainless steels contain ferrite and carbide.
Without getting too much deeper into the chemistry of metal formation, you should understand that the various alloys of stainless steel primarily differ in terms of where the iron atom is located within each grain. Ferritic steels have a body-centered-cubic grain structure. Austenitic and other types of stainless steel, by contrast, have a face-centered grain structure.
The body-centered-cubic grain is responsible for the fact that, unlike all other types of stainless steel, ferritic steels have a magnetic nature. This difference lies in the quantum-mechanical aspect of the metal's microstructures — in other words, way that electrons are arranged at the core of the metal's grain.
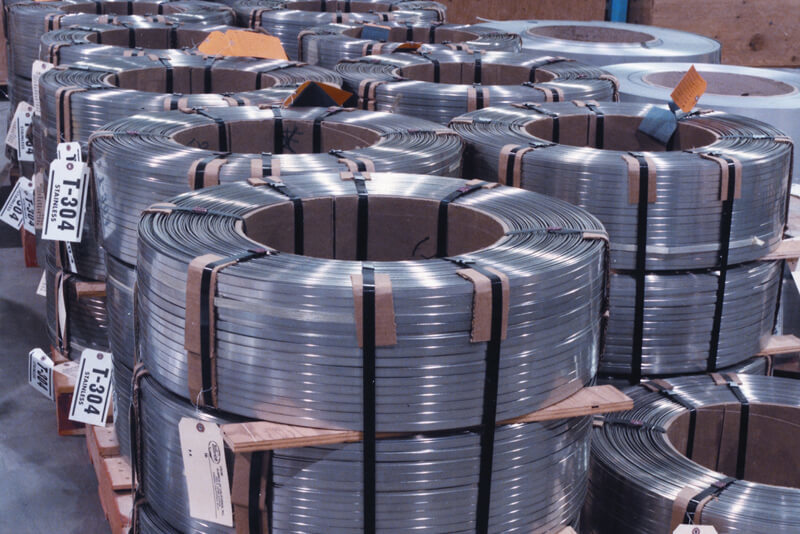
Characteristics of Ferritic Stainless Steel Strip
Now that you have a basic understanding of how ferritic steel alloys differ from other varieties of stainless steel, you are probably curious about how this affects the performance of ferritic steel. There are five important characteristics to be aware of.
Steel with Resistance to Stress Corrosion Cracking
Stress corrosion cracking (SCC) is a common form of steel degradation, caused by a combination of tensile stress and a corrosive environment. Austenitic stainless steels are particularly vulnerable SCC when exposed to chlorides. The microstructures found in ferritic steels, however, give them a high degree of resistance to SCC, making them a great choice for use in environments where chlorides will be present.
Stainless Grades which have Good Ductility and Formability
Carbon is what gives steel its hardness — yet carbon also contributes to making steel more brittle and less ductile. Because ferritic steel contains low carbon levels — as little as 0.03 percent — they tend to possess above average ductility. As a result, ferritic steels can be shaped extensively without risk of weakening.
The low carbon content of ferritic steels also gives them excellent formability properties, meaning they can be formed into various shapes without encountering problems such as necking or cracking.
The benefits of ferritic steel's low-carbon composition do come with certain trade-offs to be aware of. For instance, ferritic steels cannot be hardened through heat treatment. Furthermore, certain types of ferritic steel may exhibit problems when welded — for instance, unwanted cracking along the heat-affect zone.
Types of Stainless Exhibiting Low Thermal Expansion
Another key benefit of ferritic steels is their naturally low coefficient of thermal expansion. This simply indicates the fact that ferritic steels will undergo less expansion as they take on heat. Instead, the metal will retain its fixed dimension much more readily. As you can imagine, this property is especially important for metals that will be used for high-temperature applications.
Stainless Known to Have High Thermal Conductivity
Ferritic steels demonstrate excellent thermal conductivity attributes, meaning they allow heat to move efficiently through them. As a result, ferritic steels are a popular choice for furnace and boiler heat exchangers, and other applications involving the transfer of heat.
Stainless Steel with High Oxidation Resistance
Finally, ferritic stainless steel exhibits a stellar degree of resistance to oxidation, especially at high temperatures. This resistance has to do with the formation of a protective chromium-oxide film on the surface of the steel. Manufacturers can improve oxidation resistance even more by including aluminum and/or silicon when producing ferritic steel.
What is a ferroalloy?
You might hear the term ferroalloy in your travels as a manufacturer or someone who commonly works with metals, but what does it mean? A ferroalloy is an iron-bearing product, not within the range of those called steels which contains a considerable amount of one or more alloying elements. Such elements might be manganese, silicon, phosphorous, vanadium, chromium, ferromanganese, ferrophosphorous, etc. The chief use of these alloys is for making additions of their respective alloying elements to molten steel.
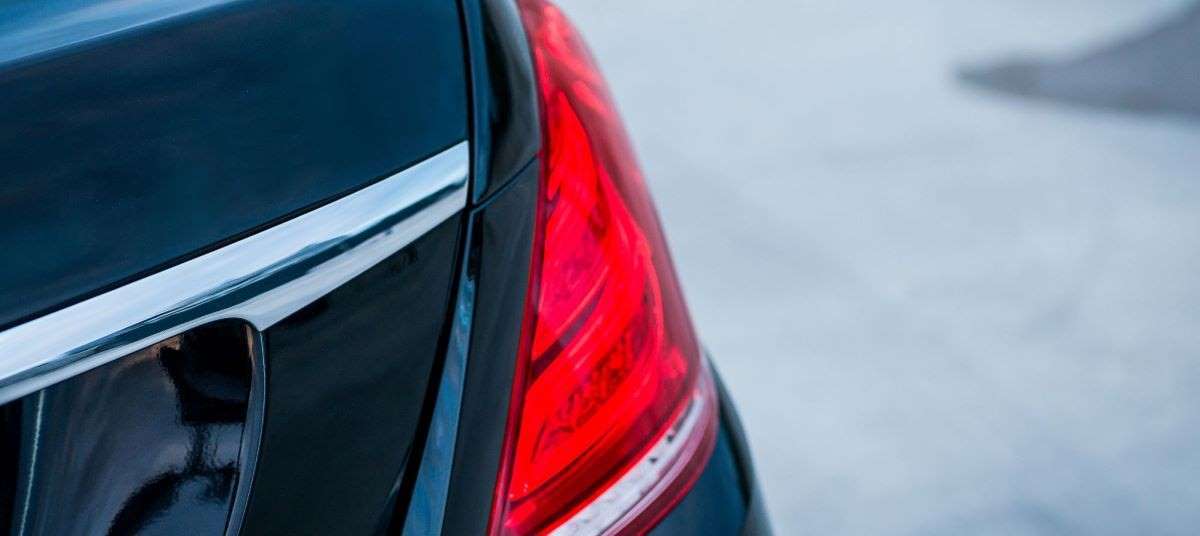
The Five Groups of Ferritic Stainless Steel
Ferritic stainless steels can be further broken down into five groups, which vary in terms of the exact amounts of various metals they contain, as well as their performance attributes.
Group 1 ferritic steels are among the least expensive forms of stainless steel. They have very low chromium levels, which means that they will usually accumulate a layer of localized surface rust over time.
Group 2 ferritic steels are the most commonly encountered variety. With their higher chromium levels, these steels possess more corrosion resistance. Group 2 ferritic steels are commonly used for interior appliances and building features.
Group 3 ferritic steels are noted for their ease of welding and forming, which gives them a broader range of applications.
Group 4 ferritic stainless steels contain greater amounts of molybdenum, further increasing their corrosion resistance. As a result, this type of steel is often used for high-moisture applications like hot water tanks and exhaust systems.
Finally, group 5 ferritic steels have the highest amount of chromium, giving them a degree of corrosion resistance rivaled by few other metals.
There is no one stainless steel to accomplish all tasks. Instead, you must select the grade of steel best suited for your particular application. For assistance picking out the right grade of stainless steel strip or wire for your next project, please contact the industry experts at Ulbrich Stainless Steels & Special Metals.