Forming Stainless Steel and Nickel Alloys
As part requirements continue to become more advanced, a more complex raw material may be needed to keep up with improving designs. Cheaper alternatives, while cost-saving, can introduce defects and errors across manufacturing processes. These can be solved may times by correct alloy selection and design. Ulbrich specializes in stainless steels and specialty metals, and has been aiding its customers as their needs, as well as the needs of the rapidly evolving industry, have continued to change for almost a century.
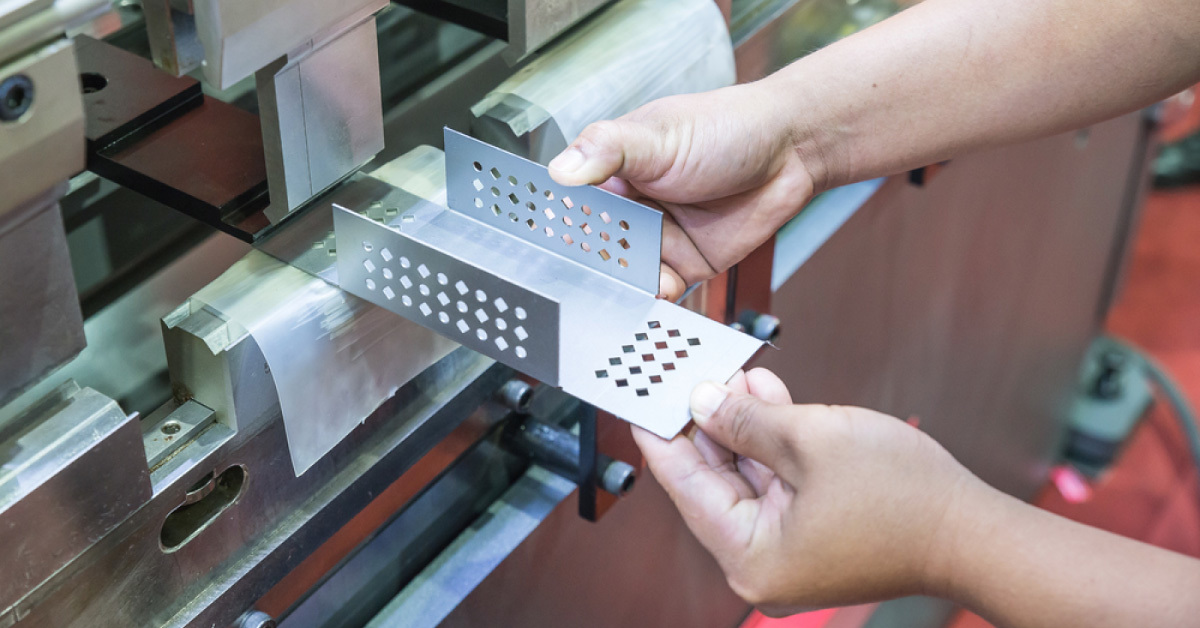
There are many considerations that need to be taken when selecting a specialty metal like a nickel-based alloy or a stainless steel for a customer’s design. Mechanical properties continue to become more specified and stringent with every new product and lend themselves to creating a more consistent part that can be used in critical applications without error. Formability and strength are also variables to be considered when selecting an alloy, as many different factors can influence these properties. Through partnership and development with a mill or reroll source, a specification that maximizes the chance for repeatable success can be created.
As the needs of customers and consumers continue to advance and become more challenging, selecting a more highly engineered product can help save production time and capital. When looking at formability, stainless steel and nickel alloys become the go-to material for fulfilling advanced requirements.
Formability
The relative formability of metals is characterized by the R/T ratio – a ratio of the radius of the bend to the thickness of the strip – or minimum bend radii. A 3T minimum bend radius means the smallest radius to which a material can be bent without cracking is three times its thickness. But with the use of custom processed strip, higher precision processing equipment and controlled composition of the metal, there is less reliance on these guidelines today.
Formability can be adjusted according to the limitations of the material and the complexity of the part. One important property used to modify formability is grain size. Adjusting the grain size of the material can greatly improve formability, as the grain size can be manipulated through processing steps to improve characteristics that better suit post processing operations. For example, deep draw applications typically require a coarser grain to allow the material to flow while maintaining properties throughout the draw.
A great deal also depends on the depth and complexity of the part, and the number of stations in the progression. For blanking, a finer grain is appropriate. The greater strength assures an effective, clean punch through the material. However, too fine a grain can make the material so resistant to deformation that it can pull apart in the die.
As the coarseness of the grain increases, the microstructure can begin to lack uniformity. This can cause issues in all post-processing operations, but particularly stamping operations. The stamper needs to start looking for “orange peel” at the edges and sidewalls of the parts, especially those that are deep drawn. If orange peel does not occur and surface roughness is not a major factor, a grain size can be specified as even coarser, which results in a very soft, easy-to-form material. However, in order to achieve this structure, the material may require more customer and precise processing through the final anneal.
In the case of nickel alloys, a little finer grain than stainless is recommended for best results. To learn more about grains, check out our article on the king of manufacturing operations.
Adjusting Grain Size
Once the extent of the forming operation is known, a specification can be determined to ensure success with the product. First, the metallurgist will create a specific process in order to target the mechanical properties and grain size specified by the customer.
To confirm the results, samples from the heat will be examined in the metallography lab. Grain size will be measured, and mechanical properties will be tested and reported. These measurements are imperative not only to Ulbrich, but to the customer as well. Knowing what the mechanical properties are on the material being used is key in preparing and tooling for the job ahead.
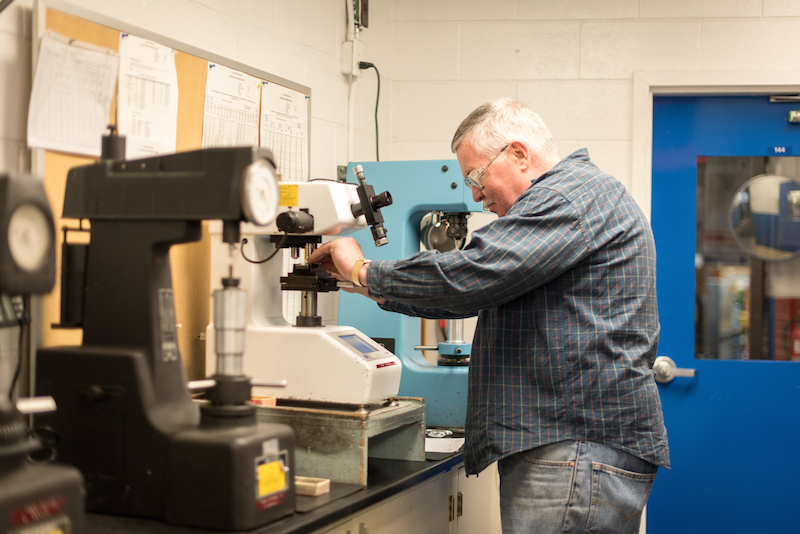
Hitting the Specification
If formability were the only objective in specifying the annealing process, meeting the customer specification would be relatively easy. But there are other factors which must be considered. In many cases, a grain size smaller than ideal for forming may be needed to provide the required mechanical properties. When this is the case, a material compromise must be reached within the specification being created.
Stainless steel can be specified in annealed or cold rolled tempers. The latter are designated ¼ hard, ½ hard, full hard, and extra full hard tempers depending on strength requirements. What is important to remember, however, is that strength and formability are inversely related. Everyone wants the strongest and most formable material for their designs, but this is simply not achievable. Increasing temper limits the amount of forming that can be done, as there is a maximum amount of deformation every material can handle before breaking. That limit decreases with an increase in temper and mechanical properties. Even forming the ¼ hard temper requires significantly more effort than regular annealed material.
Alloy Selection
Type 301 is a good candidate for stamped parts because its range of tensile and yield strengths is extremely vast when compared to other stainless steels. It is true that Type 301 can take a great deal of pulling and stretching, but its tendency to work harden quickly means that annealing is generally required to soften the material to avoid stress cracking or splitting. For this reason, Type 301 is usually not employed in operations involving severe deep drawing.
Type 305, on the other hand, exhibits a much narrower range between yield and tensile strengths, and the spread narrows during plastic deformation. But its relatively high nickel content gives it a slow work hardening rate. Yield strength and tensile strength increase very slowly during forming, so it can be worked over a series of dies without getting extremely hard or brittle. Extensive forming is usually possible before it is necessary to stop for annealing.
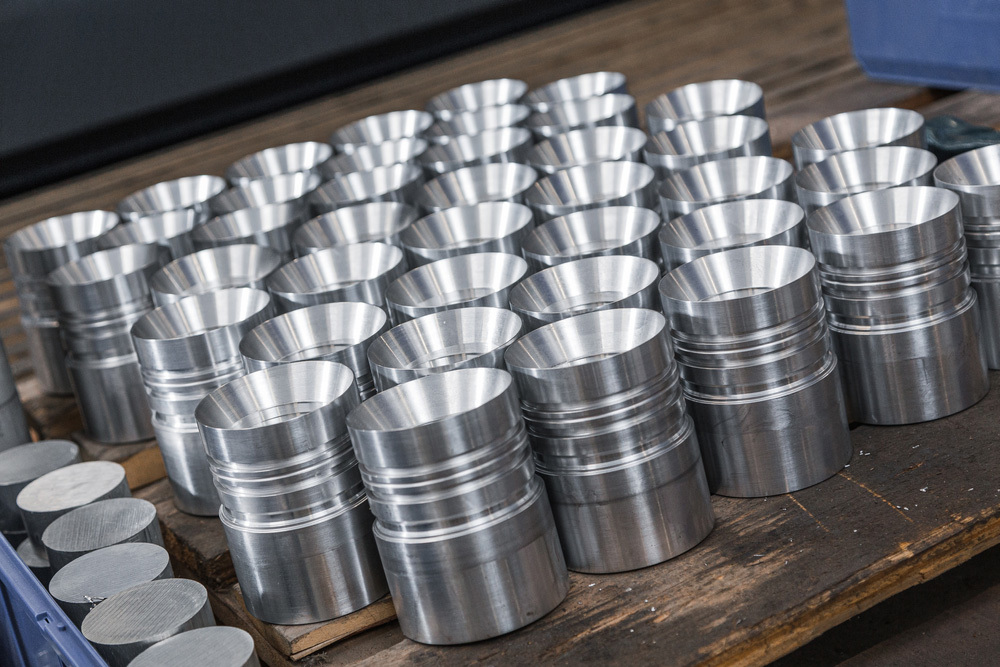
The initially high elongation of 305 falls off rapidly, however, so it is not suitable for operations involving stretching. Even for deep drawing operations, the metal should be allowed to flow freely through the hold-down pads in the die to hold stretching to a minimum. Unless the part is locked into another alloy, Type 305 is the grade of preference if the choice is left to the stamper.
The straight chromium grades of the stainless that are most commonly fabricated by cold forming are Types 410, 420 and 430. Compared to carbon steel, the strengths and hardness of the 400 series of alloys are higher while elongations are generally lower. This means more power must be applied to achieve plastic deformation.
If the application requires a nickel alloy, the one with the highest nickel content will be easiest to form. Among the proprietary alloys, Monel® 400 and Inconel® 625 are somewhat less formable but offer superior mechanical properties. Stampers are also drawing other nickel-alloys, particularly Hastelloy® C-276, Hastelloy® X as well as Haynes® 230. None of these alloys are highly ductile, but they can be rolled and annealed to provide very acceptable formability.
Tooling
The mechanism that makes stainless steel and nickel alloys corrosion resistant is an oxide formation. Oxides on the surface of a metal are extremely abrasive. These alloys will impose more rapid tool wear than straight carbon steel, and galling can be a very serious problem. Tungsten carbide tooling and extreme pressure lubricants are always required, although it is possible to do short pilot runs with hardened tool steel. Since stainless steel and nickel alloys do not accept reductions as readily as carbon steel, the tooling should also take this into account. On complex parts, one or two additional stations might be required in the die progression.
Production
Because the higher strength of these alloys creates more resistance at the die face, some accommodations may be required in production. This could include somewhat slower press speeds than are normal for carbon steels, a more powerful press, or some combination of these factors. It is recommended to consult with a metallurgist or product expert before making your alloy selection.
Confer, Consult, Communicate
The best information that the stamping producer can provide to the supplier of stainless steel or nickel alloy strip is a drawing of the part. Metallurgists familiar with forming processes can tell from the severity of the bends and complexity of the part which alloy and temper to recommend.
For very complex shapes, the stamping manufacturer may want to go back to the buyer and inquire why the part is being made in stainless or nickel alloy. If the user is looking for greater strength, there isn’t too much leeway in adjusting the metal for greater formability. But if improved corrosion resistance is the major reason, which it often is when the alloys are specified, the user may be willing to accept a softer material.
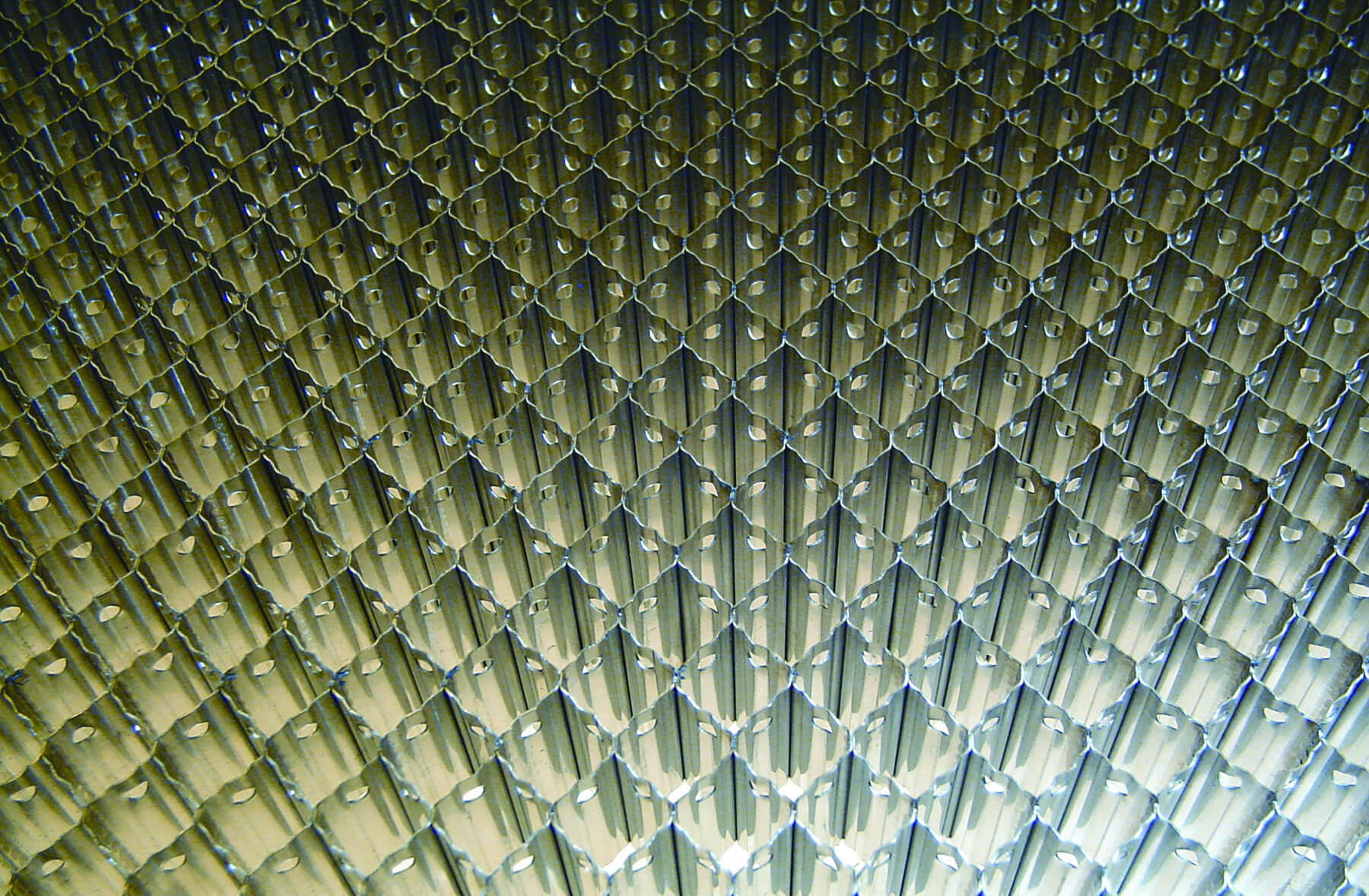
The honeycomb applications, which are one example of a fabrication using these alloys, can be a challenge for both stamper and materials supplier. Honeycomb is utilized in aircraft and aerospace applications in which high strength and stiffness must be combined with minimal weight. It consists of thin, narrow strips of metal with a cold formed pattern of parallel U-shaped ridges with often repeating detailed features. The strips are spot welded to one another, layer upon layer, at the apex of the nodes. Although the forming of the nodes is shallow, uniformity of detail must be maintained throughout the strip for the pieces to match up and structural integrity of the welds to be maintained. Both formability and material thickness must be consistent.
Although processing stainless steel and nickel alloys may require some extra design effort, there are substantial benefits beyond the inherent alloy system that can be achieved. These include more rapid production rates, longer life of the tooling, a better-quality part, and the knowledge that your shop is gaining some ‘bankable” expertise in producing higher cost, higher performance parts.