Types of Rolling Mills
Rolling mills compress metal into a uniform thickness, bend it into custom shapes, and create custom-sized stripping. There are many different types of rolling mills, and the optimal mill for your product depends on the metal and rolling process your manufacturer will use.
All sorts of markets require custom metal products to function. And because so many industries require custom-rolled metal, these products are extremely common in daily life. You’ve almost certainly used something produced by rolling mills at some point, even if you haven’t realized it! From your car to your cell phone to your jewelry, products created by rolling mills are used every day.
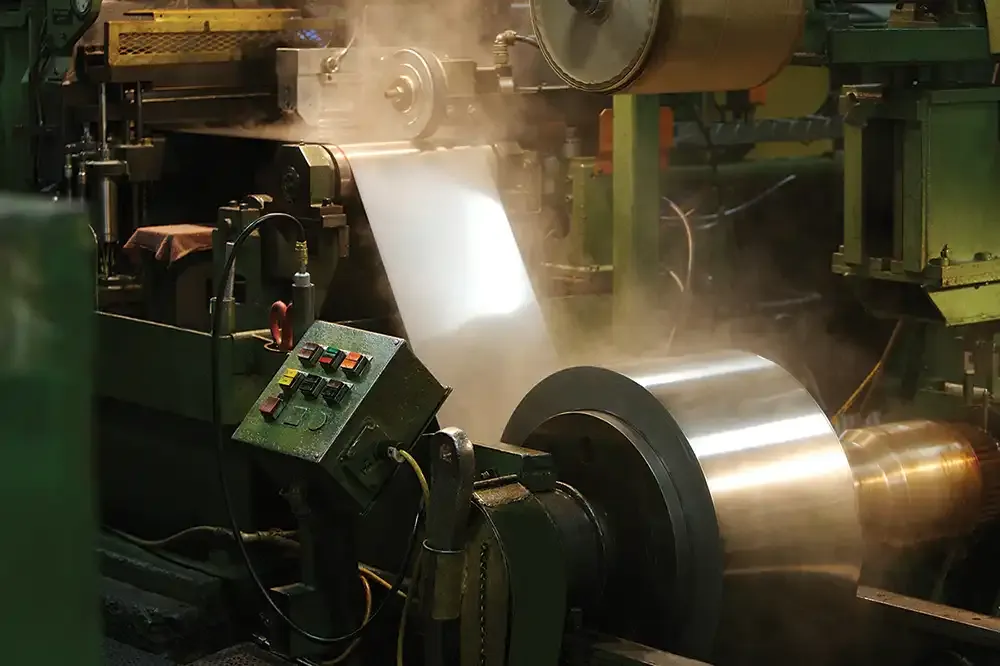
Rolling Mill Uses
Just about all metalwork is custom in some regard. Because of this, there are many different types of mills—and different uses for each one. For example, one mill might specialize in flat rolling and another in working on grooved rolls. A large mill will have a higher rolling load capacity, but not all jobs are large enough to require so much raw material.
Custom metalwork requires fine-tuned machines that can create products like wires, strips, and banding out of a variety of metals. The rolling operation and equipment used will depend on what material is needed and what the end result will be.
Main Types of Rolling Mills
The different types of metal and the specifications of the final product will help determine which type of rolling mill your product will be produced with. Here are a few of the main types of rolling mills:
- Continuous rolling mill. Sheet metal passes through several rolling stands, each pressing the metal thinner.
- Cluster rolling mill. A cluster of metal rolls are lined up to be thinned out.
- An example of a cluster rolling mill would be a 20-High Cluster Rolling Mill. These mills offer impressive accuracy tolerances by bearing the rolling force along the entire width of the rolling mill through the backing bearing. Some featured advanced technology, including automatic gauge control and dynamic power crown adjustment.
- Planetary rolling mill. This type of roll mill is mainly used to crush or grind down raw metal rolls.
- Two-, three-, and four-high rolling mills. Determined by the mill stand quantity, these mills roll in opposite directions to press and finish the metal.
In addition to the different types of rolling mills, your metal manufacturer might use a cold rolling mill or a hot rolling mill to work certain types of metals and create different products.
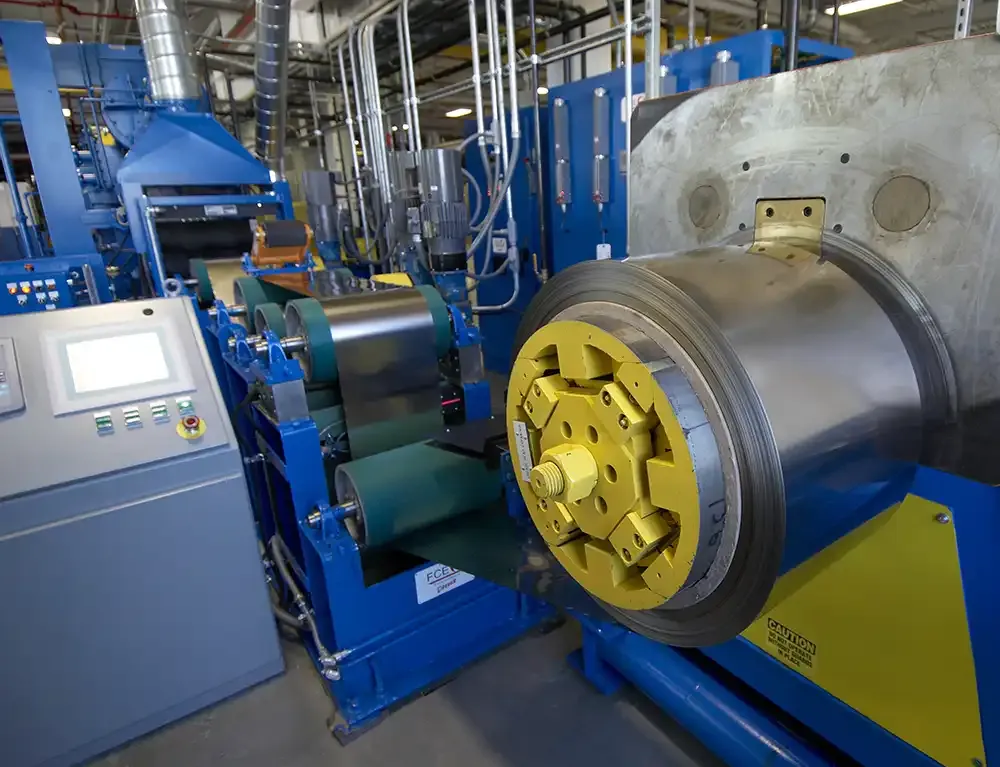
How Rolling Mills Are Classified
In some cases, rolling mills are classified according to their setup. Some manufacturers use a continuous rolling mill or a two-, three-, or four-high mill to achieve your unique desired product. However, different mill configurations fall into two main categories: cold and hot rolling mills.
Ways to Classify Rolling Mills
Although there are several different types of rolling mills, they are generally classified by the temperature they operate with: cold or hot.
In a cold rolling mill, metal is pressed through the machine, and the cold temperature actually hardens the metal. This type of roll mill is often used for materials like stainless steel, aluminum, and titanium.
As you might guess, a hot rolling mill heats up to shape pieces of sheet metal. This rolling process is often used to create steel I-beams for building construction or framing for new automobiles.
Each rolling process is unique, which allows for a steel mill or other metal manufacturer to create a wide variety of products. This versatility is just one of the characteristics of the process itself.
Characteristics of the Rolling Process
In addition to outputting uniform metal sheets, strips or wires, the rolling process actually strengthens the metal itself by treating the material with extreme hot or cold temperatures. And thanks to advancements in mechanical engineering that have enhanced metal mill productivity, there’s hardly any runoff or lost material.
Another characteristic of the rolling process lies in the mill’s rolling load. Small machines can handle two rolls at a time, and larger ones can handle three and four sheet metal rolls. Regardless of which rolling process used, the result will be a durable, uniform product.
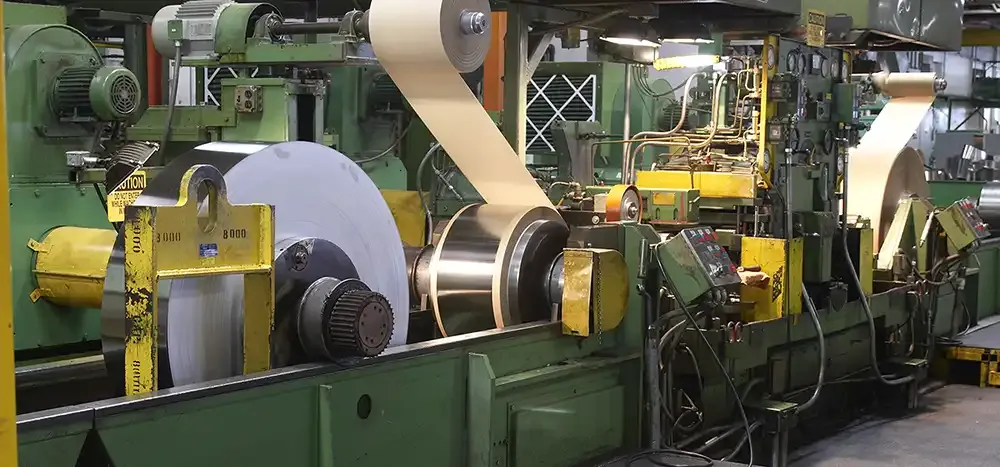
Two-, Three-, and Four-High Rolling Mills
When multiple metal rolls need to be processed at once, a two-, three-, or four-high rolling mill could be optimal. Each has advantages and disadvantages, and choosing the best option depends on the job size, metal type, and shape and size of the final project.
Two-High Rolling Mills
As the name suggests, two-high rolling mills use two mill rolls of sheet metal stacked on the rolling stand. One roll processes through the machine clockwise, and the other roll moves counterclockwise.
These cold-rolling mills excel at working soft metals like copper and lead. And because they’re smaller than three- and four-high rolling mills, the two-high models are often less expensive than larger options. However, because of their size, they can’t always press the metal as thin as a three-high rolling mill can.
Three-High Rolling Mills
Three-high rolling mills generally use two large working rolls, plus a smaller backup roll. The first and third rolls rotate in the same direction, and the middle roll rotates in the opposite direction. Often used to create cladded material, these mills are fantastic for metals like steel, aluminum, and stainless steel.
Although three-high rolling mills have many benefits, if you need an extremely small strip thickness, you might need to use a larger machine such as a four-high rolling mill.
Four-High Rolling Mills
With a four-high rolling mill, two working rolls of metal are placed close to the workpiece, and two larger rolls are placed at the very top and bottom of the roll stand. Although they are expensive, these massive machines can press all sorts of sheet metal into extremely thin strips. Industries like aerospace and the military often require the precision metalwork that a four-high roll mill provides.
Regardless of the working roll and backup roll quantity, the mill’s actual configuration is also an important element in how custom metal products are manufactured. The three main roll mill configurations are the cluster, planetary, and continuous rolling mill.
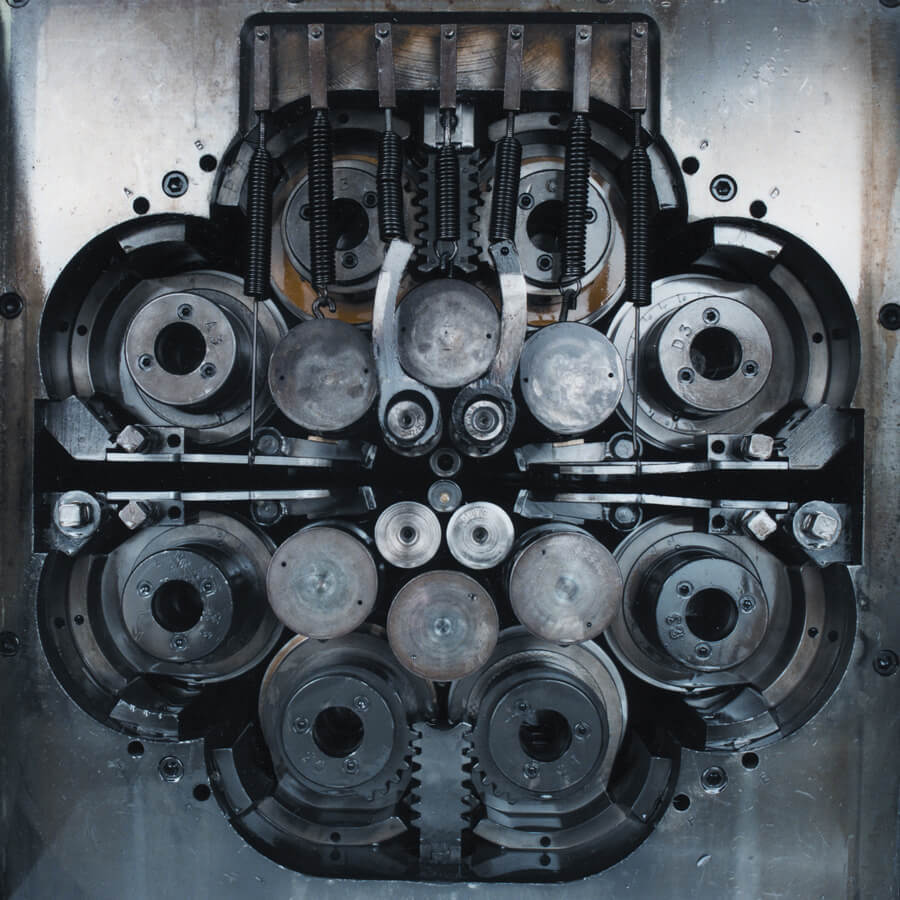
Cluster, Planetary, and Continuous Rolling Mills
Different metals and quantities of product require different mills. When producing custom metalwork, three of the most common options are the cluster rolling mill, planetary rolling mill, and continuous rolling mill.
Cluster Rolling Mills
Cluster rolling mills are massive pieces of machinery. They’re basically a specialized type of four-high rolling mill that allows you to add some larger and smaller work rolls of sheet metal during the rolling process. Thanks to their strength, they’re often used for hard metals like titanium alloys.
Planetary Rolling Mills
Planetary rolling mills are used for processes like steel rolling and stripping. This equipment uses a grinding jar to create friction and grind down the sheet metal that’s fed through the machine.
Although they don’t produce as much output as continuous rolling mills, they don’t require as much heating and result in very little material loss.
Continuous Rolling Mills
A tandem rolling mill, also called a continuous rolling mill, allows multiple rolls of sheet metal to pass through the machine without interruption. Continuous rolling mills are helpful for big projects and are often used to produce a large quantity of heavy-duty material like I-beams for buildings or guardrails for highways or roads.
These mills are excellent for mass production because they can handle a large rolling load. However, they aren’t cost effective for small jobs due to the labour needed to set them up and the utilities required to run them.
With the wide variety of rolling mills available, you can rest assured that you’ll receive excellent custom products manufactured to your specifications.
Delivering Precision with Advanced Rolling Mills
Ulbrich Specialty Strip Mill (USSM) is our premier strip manufacturing facility with an array of 20-high, four-high, and Sendzimir mills. Utilizing the strengths of each, we precision roll more than 160 stainless steel and special metal alloys to impart the exacting material properties and specifications required by our customers.
If you’d like to learn more about Ulbrich’s mills and our precision-rolling capabilities, contact us.