Stainless Steel Supply Chain: What are Melt Mills, Re-Rollers, and Service Centers?
The metal industry is among the oldest in existence. Several countries determine their industry growth by the increase in metals, demonstrating how crucial this material is. The metal supply chain comprises three critical stages: melt mills, re-rollers, and service centers. There are, of course, other steps in the supply chain and different tiers beyond these three. For the purposes of this article, and obtaining material for manufacturing processes such as stamping or deep draw however, let’s regard these as “the big three”.
The melt mill, precision re-roller, and service center have specific and vital roles they play in stainless steel & special metal manufacturing.
All metal items begin the supply chain journey in melt mills, where steel or other alloys are melted, refined, and cast into usable forms. From the melt mill, the material is usually sent to either service centers or re-rollers. This is usually dependent on the type of material, the thickness and the application for that material. This metal may go through many more tiers of the supply chain such as part makers or stampers before it reaches its end user.
Most sector players consider re-rollers and service centers to be even points, but this may not always be the case. At Ulbrich, our divisions include both re-roll mills and service centers to meet our customer's varying product lifecycle and scale needs, but this is unique for our industry.
In this article, we’ll discuss all the stainless steel supply chain stages, their significance, and how they meet the needs of manufacturers. Some of this information can be applied to special metals and the supply chain of those alloys, but we’ll save the differences for another article! Most of our concentration in this article will be on stainless steel. We will try to inform on each of the three stages’ roles and when it is appropriate to purchase from each.
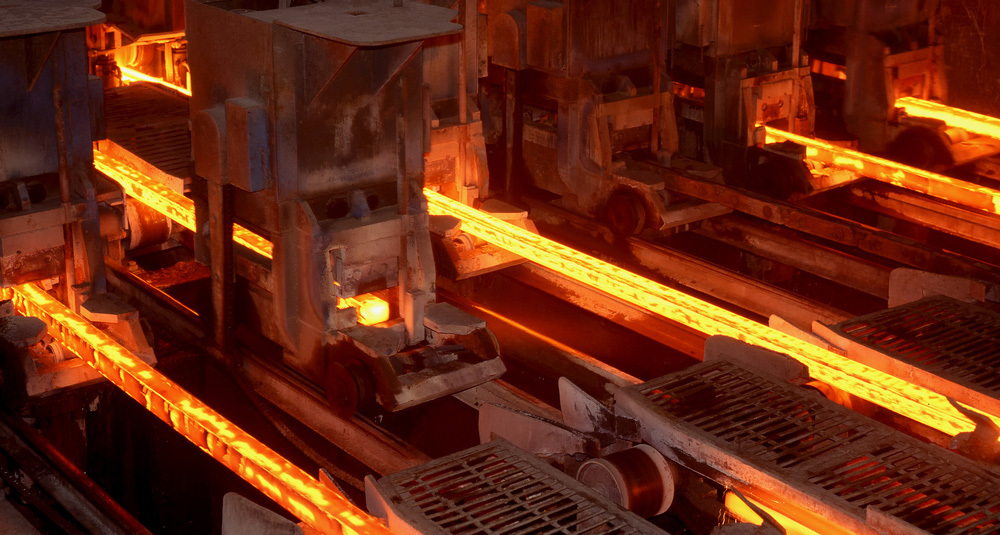
Melt Mills
Also known as the steel mill or sometimes even steel plant, the melt mill plays an important role in the stainless steel supply chain. This is where new and recycled metal material are melted together to form stainless steel strip or other forms such as bar, plate and wire. Melt mills collect and process a combination of recycled and virgin stainless steel material to come up with different steel grades. Usually the makeup of this is around 90% recycled steel and 10% virgin steel. This is true of both stainless items and carbon steel.
Recycled material can come in from a variety of sources such as regular stainless steel consumer items that are recycled, and scrap from dealers and vendors. Scrap vendors will work with precision re-rollers, service centers, and part makers to purchase and sort “precision scrap” which is already sorted by alloy and avoids impurities within the metal. The scrap vendors then sell this material back to the melt mills where it is checked and sorted again before being melted along with the virgin material to create the metal products we know such as strip, wire, and bar.
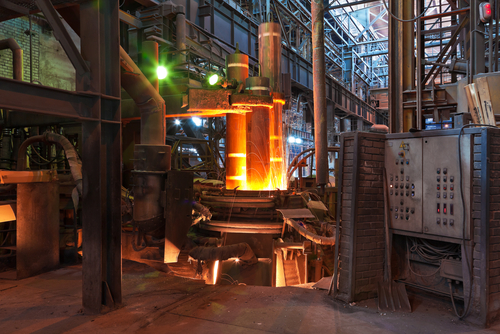
Most mills use the eco-friendly EAFs (electric arc furnaces) as opposed to traditional blast furnaces. This alternative consumes less energy and produces significantly lower carbon emissions. Also, companies in the stainless steel industry are keen on keeping wastes as minimal as possible. They collect and segregate any product pieces that are usually discarded during manufacturing. All this in-house scrap will be later melted in the electric furnace.
The different furnaces used in melt mills are responsible for melting the steel. The metal chemistry is also adjusted by reducing several alloy elements and introducing others to achieve optimal chemical purity. Thin slab casters in a hot steel mill convert the molten steel into a continuous steel ribbon about 60 millimeters thick. These can be rolled into huge steel sheets or slabs efficiently, cost-effectively, and quickly. Metal can also be formed into wire, tube, pipe and various other forms.
The slabs go through cooling water to make them completely solid and reduced to customer requirements on a hot rolling mill. The new hot band of steel will then be coiled automatically, and the coils chemically cleaned in the cold mill complex.
Notably, the material leaving this section can be in a strip form, but it is usually on the thicker side with looser tolerances. This makes the material unusable for a range of specialized applications in industries like the medical and aerospace markets. This is where the critical role of a stainless steel re-roller comes into focus who create steel varieties with distinctive features for specific sectors or usages.
For manufacturers looking to purchase metal, going mill-direct might be a consideration if they buy a large quantity of material with minimal specification requirements and can store a large amount of material on-site at once. Additionally, companies that can meet the Minimum Order Quantities (MOQs) set by melt mills —typically larger than orders placed through distributors—may find this route beneficial. MOQs refer to the smallest amount of metal that a melt mill is willing to produce and sell in a single order, which can vary depending on the alloy and the mill's production capabilities.
Melt mills often operate based on heat size, which refers to the batch of metal produced in one melting process. A heat size can range widely, depending on the furnace and type of metal being produced, but it usually involves significant quantities of material — think 240,000 pounds of material that you must take all at once.
In terms of lead times, mills typically offer longer lead times compared to distributors and customers are subject to whatever they can offer. This is because melt mills often produce metal to order, meaning production only begins once the purchase order is received.
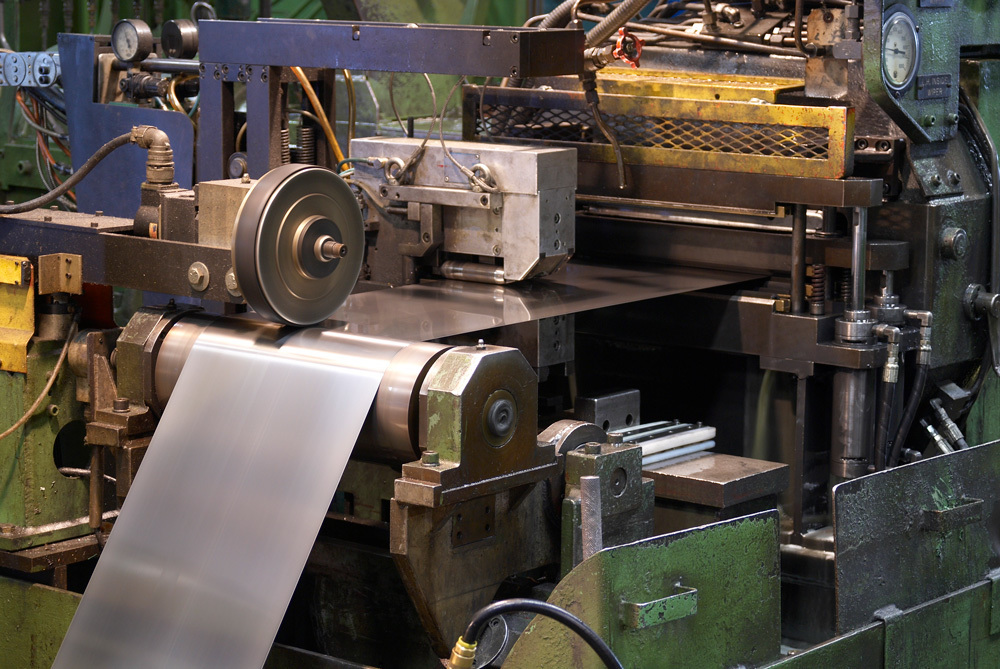
Stainless Steel Re-Rolling
Stainless Steel re-rolling plays a crucial role in the steel supply chain, offering material in smaller quantities and better lead times. Re-roll mills also provide customers with critical metallurgy and product management support for a more personalized experience.
As the name implies, the process involves re-rolling metal to produce material at thinner gauges with tighter tolerances, after it comes to them from a melt mill. The process is usually necessary for metal used to produce high-end medical and aerospace applications, among others. The demands on the metal may be due to the life threatening situations one may be in when these applications are used, or the environments the metal may be exposed to during its end use. If something is going in your body (medical needle), you will want the highest quality product possible.
Similar to the melt mill, there is a furnace used within the re-rolling business as well. Material enters a re-roll mill in strip form and needs to be re-rolled down to thinner gauges. However, due to the mechanical properties of stainless steel, this cannot all be done at once, for most thicknesses. It needs to be intermediately annealed (heated) in between rolling sessions to relieve stress before it proceeds to be rolled to very thin gauges. The rest of the rolling process typically occurs at room temperature. This is cold rolling. Throughout all of these processes, state of the art equipment and systems are used to control and measure the exact thickness of the material throughout the entirety of the coil. This is how precision re-rollers like Ulbrich are able to obtain such tight tolerances on their metal.
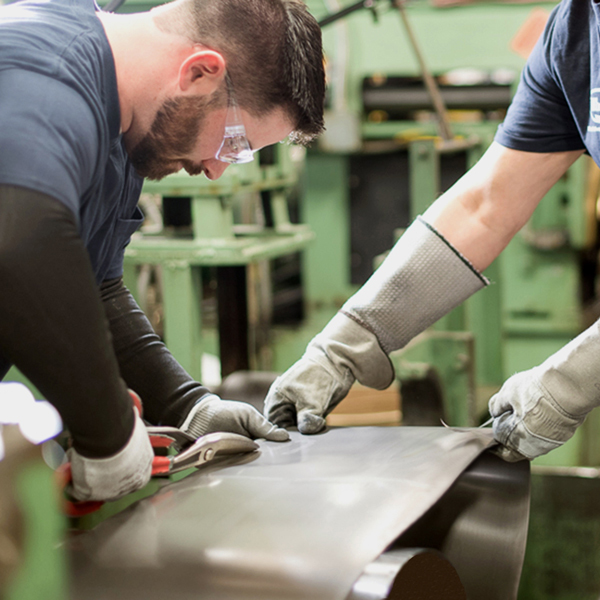
Metal re-rolling is a crucial segment of the steel supply chain and is among the most important combinations of metallurgical expertise, technology, and processes deployed in the whole of stainless steel manufacturing.
The cold rolling process gets rid of metal defects like shrinkage, and the material ends up acquiring a compact structure and excellent mechanical and physical properties, with tight tolerances throughout the finished product. The characteristics that a precision re-roller is able to add to a material make it an excellent choice for customers that value (or even require) consistency and precision in a metal’s properties or tolerances.
Manufacturers should consider buying from a precision re-roller when the metal for their application has special requirements that can’t be met by a service center. Re-rollers are critical partners for manufacturers engaged in product development. The combination of expertise and capabilities offered by a re-roller such as Ulbrich are valuable for companies who have an application in mind, but the part makers are unsure of what metal or thickness to go with. A re-roller such as Ulbrich will deploy their team of engineers and metallurgists to help your team overcome metal and other manufacturing challenges uniquely suited for your manufacturing processes and application.
Ulbrich Specialty Strip Mill, located in Wallingford, Connecticut, specializes in the precision rolling of stainless steel and special metals. The facility offers advanced processing capabilities, ensuring the highest quality for critical applications.
Ready to find out how we can help? Request a quote to speak with one of our metallurgists or engineers.
Steel Service Center
Another critical role in the steel supply chain is the Stainless Steel Service Center. A service center deals with a diverse variety of steel from either the melt mills or re-rollers. The facilities have massive storage depots to guarantee the regular supply of their production lines.
Once the material is received, various value-added services may be performed before it's resold to customers. These services include oscillating, cut-to-length, edging, and slitting to different widths, while the thickness, mechanical properties, and chemistry of the material remain unchanged (chemistry is only changed at a melt mill). Service centers may offer spot buying, but this comes with less customization.
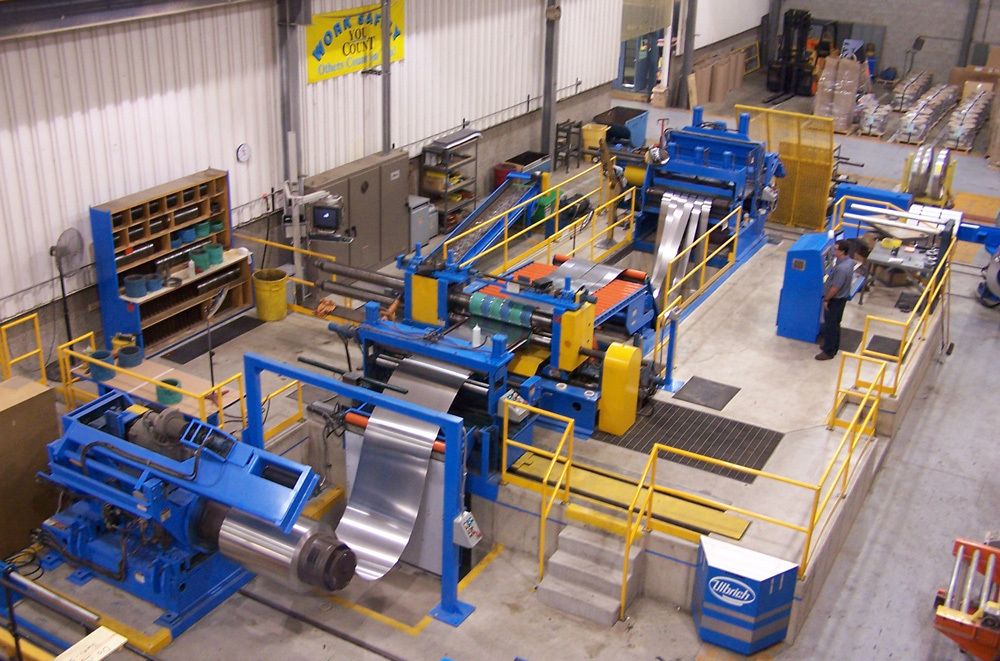
Activities that can occur at a service center, other than storage, include flattening material, and side slitting, which essentially involves cutting the borders with edge-trimming shears for a standard width. It can also be cut width-wise to form steel foils or slit lengthways. All these operations are sometimes combined to ensure the customer gets the product they need.
To add to these, the service center may also inspect, repair, and recondition the coils. They can also take samples and carry out automatic and manual controls along the chain of manufacture. The controls are usually unique to individual customer orders.
The packaging of the material isn't standard and varies based on the requirements of the customer. It's also common to find service centers offering storage and shipping services.
Some Service Centers don’t even touch the material at all. They obtain hard to find material for their customers at a lower price because of the vast quantity they procure and then store and send this material to customers as needed. In essence, stainless steel service centers are specialized in managing the supply chain. By doing this, service centers greatly help manufacturers manage their inventory levels and keep certain costs lower, while also ensuring them a steady chain of supply. Therefore, it would make sense to buy from a service center in circumstances where you may need material quickly but cannot hold a lot of inventory. A service center like Ulbrich’s divisions will work with you closely to stock material and send as you need it. The material may not be as special as that provided by a re-roller, but service centers still have the ability to meet specifications and requirements.
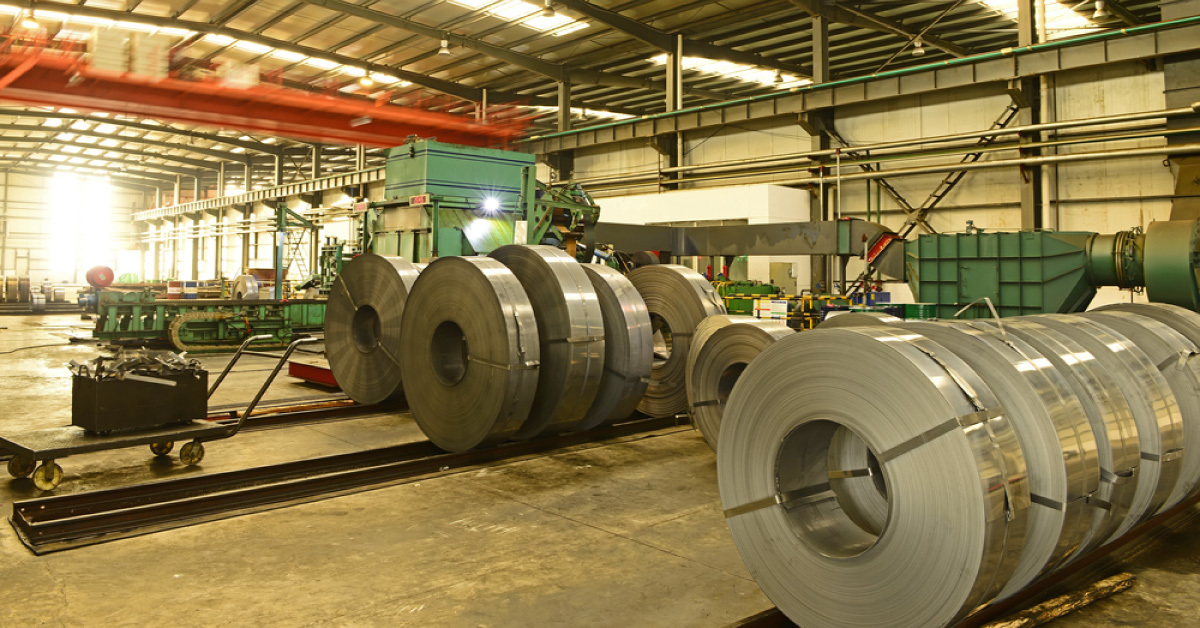
Key Takeaway
The stainless steel supply chain comprises melt mills, re-rollers, and service centers. All these have a crucial place and role and can be interdependent at times. Re-rollers have their own needs that they satisfy, and service centers also serve their own purpose.
Depending on your needs, you can choose to purchase from either of the two. It is important to consider your end application and requirements and decide which may best fit your needs. Buying from a melt mill would mean you require massive quantities and not a lot in terms of specifications and requirements. When considering a service center, it may be worth thinking about if you need help managing the supply chain or inventory levels and ensuring a steady chain of supply. Re-rollers would be providing the most specialized materials. For those specialty alloys and tight tolerances for specific applications, a re-roller might be the ideal choice.
You can count on Ulbrich Stainless Steels & Special Metals, Inc. for excellent quality metals to fit your needs and projects. We are industry leaders in precision metals, offering a vast assortment of stainless steel solutions used by different companies from construction to healthcare.
Contact us today to learn about our products or get expert answers from our metallurgists on any questions you may have.