Metal Selection Guide: Strip Versus Flat Wire
Using today’s precision slitters, it's possible to produce strip products in widths as narrow as .035 inch. However, material thickness has an impact on how narrow you can go. In instances where the starting material is too thick, flat wire is an avenue to achieve those narrow widths. This similarly ties in to material edges as well.
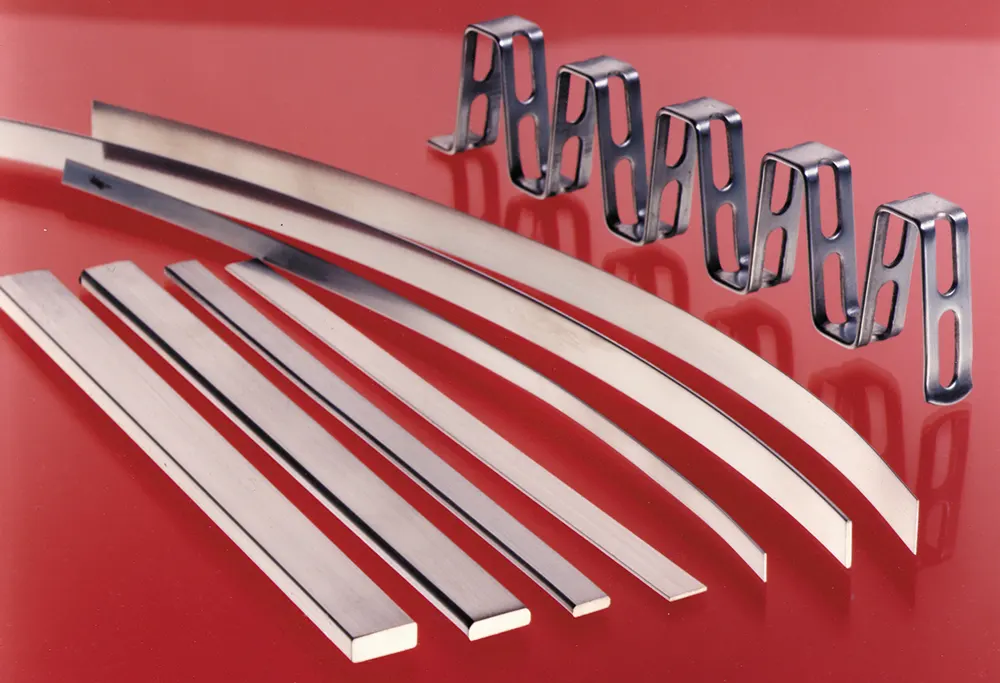
The similarities and differences in narrow width strip, one produced by slitting coil stock, the other by flattening round wire through a mill, can be seen above. The four lengths on the left started as round wire; the three on the right are slit from strip. The curtain bracket part shown in the background can be produced by either of these methods.
For most narrow-width applications, slit strip can be the most economical selection. Slitting is done on efficient, precision slitting machines which can hold close-width tolerances and make multiple cuts in a coil.
However, when the part requirements demand deburred edges, a long continuous length without a weld, or a relatively small thickness-to-width ratio, flat wire offers some advantages. These include longer continuous lengths; burr-free custom edges; or larger-sized packages of material.
The Basics of Rolling Flat Wire Strip
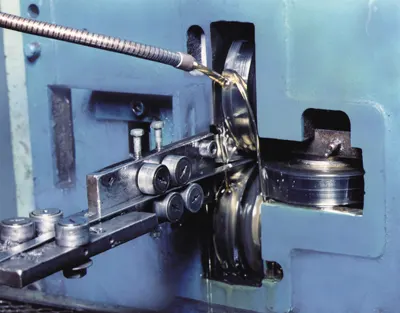
Flat wire is made by feeding rod of the appropriate starting diameter through a rolling mill, where it is flattened to the desired thickness. A set of opposing rolls in the other direction achieves the correct width and forms the edge, whether round square, or some special shape. Excellent control of width and edge condition are two of the advantages of producing narrow width strip in a wire mill.
Flattened wire is just as easy to form or blank as strip of the same grade, but just like strip, there is a width-to-thickness ratio to consider. Most flat wire applications call for a material that is relatively thick compared to its width.
When special edges are need for wider width applications, rolling wide strip in flat wire mills can allow you to create a special edge where you cannot when edging strip.
Guide to Selection: Strip Versus Flat Wire
The following are factors you should know if you are considering flat wire:
- Width. Most wire mills cannot produce widths greater than .625 to .875 inch, depending on the alloy. This is because of the maximum “spreading” that can be achieved from wire rod that is anywhere from .217 to .562 inch in diameter. For anything wider, slit strip usually is the better option.
- Thickness. A strip mill can roll foil gauges down to .001 inch. The limit on the wire mill is .008 inch.
- Tolerances. Strip will provide tighter gauge tolerances up to about .050 inch, and flat wire has good gauge tolerances above .050 inch. The tightest tolerances that can be held with flat wire are: Thickness +/-.0005”, Width +/-.001”
- Continuous unwelded length. Compared to strip, flat wire is available in longer continuous lengths without welds. The welds are made to join coil to coil in early processing stages.
- Edges. Strip coming off a slitter will have a burr along both edges caused by the shearing action of the knives. The edges can be either rounded or squared-off to remove the burr. This can be done without tempering or work hardening the edge. However, it incurs an additional cost, and the operation can be time-consuming for large quantities. On a wire mill, rolling creates a smooth, uniform edge for the entire length.
- Width-to-thickness ratio. As the ratio between width and thickness narrows to 5 or 6 to 1 and below, it can become more difficult to maintain camber, flatness, and other shape parameters when slitting strip. On a wire mill, it is possible to get the ratio down to 1 to 1, which is a square cross section.
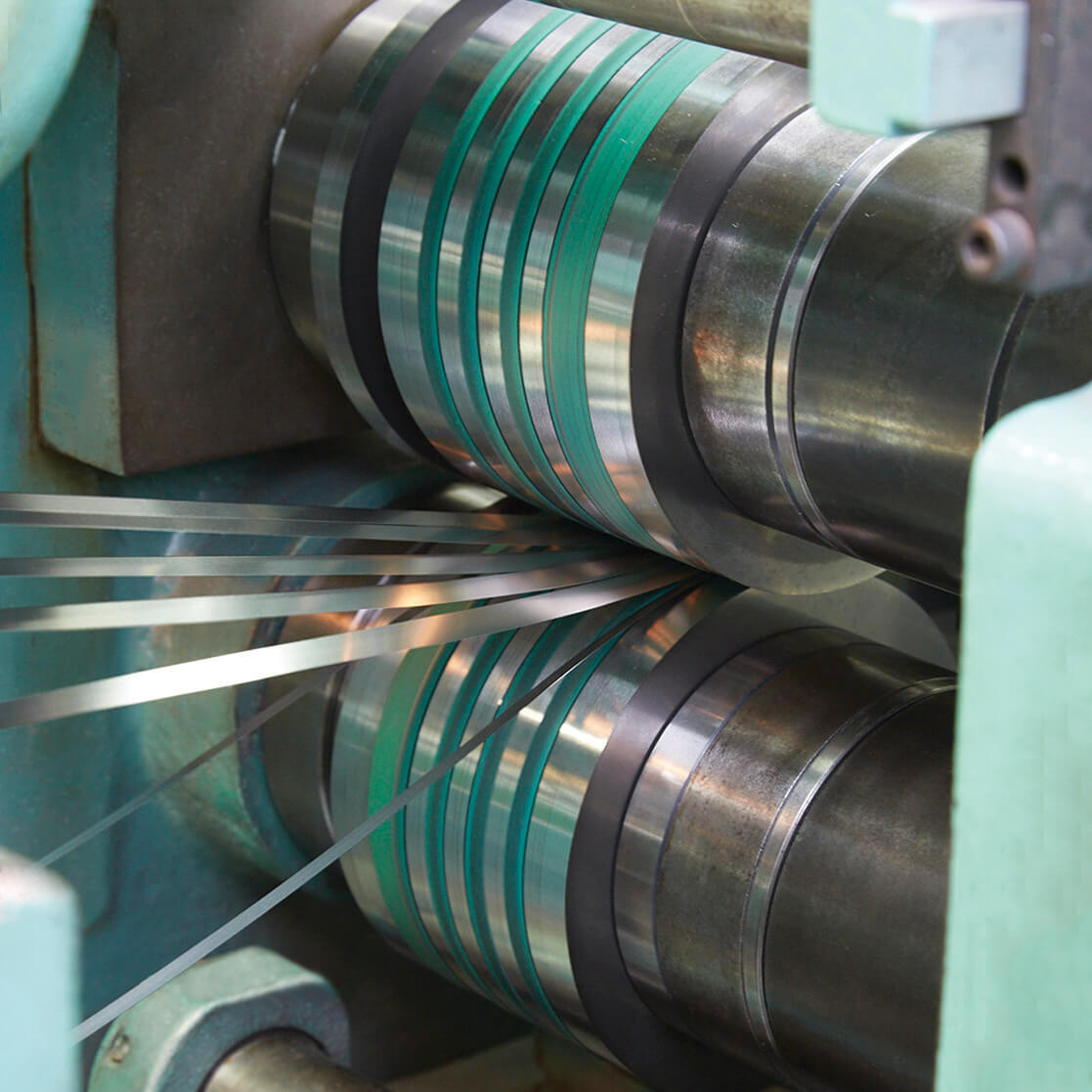
In most applications for which both processes are considered, the major issue is the burr created during slitting. If the condition of the edges is not important, slit strip may be the better choice. When it is a factor, the choice comes down to the cost of edging slit coil versus the cost of flat wire.
These cost factors are important in any selection, but they are even more critical with specialty grades of stainless steel and nickel and cobalt based alloys because of the higher cost of the materials.
Alloy Availability for Flat Wire Products
Buyers have almost as many alloy choices with wire as they do with strip, so availability is not a problem. Flat wire comes in Series 300 and 400 stainless steels, nickel alloys and cobalt alloys, precipitation hardening alloys, and many of the proprietary alloys.
When the economics favor flat wire over slit strip, producers can provide close tolerances and burr-free square or rounded edges in either large or small quantities. Flat wire or strip can also be straightened (or flattened) and cut-to-length to meet specific customer requirements.
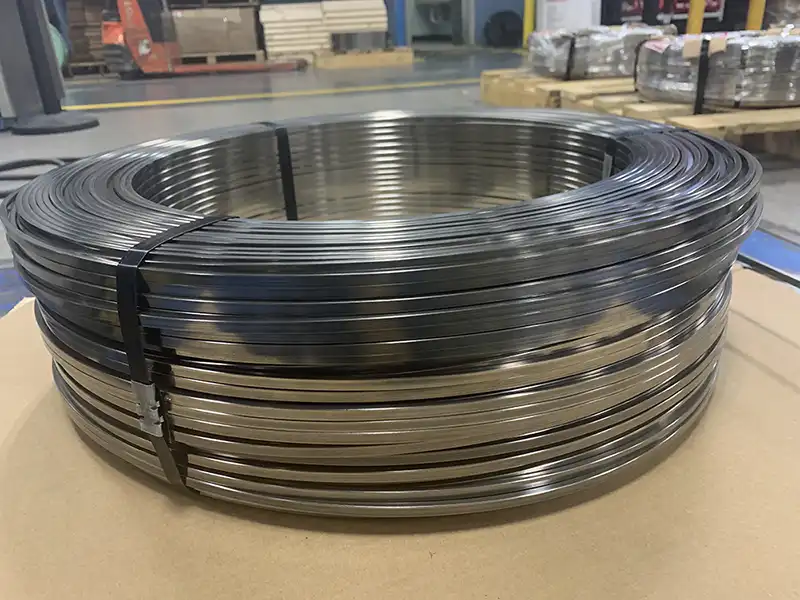
Could Stamping with Flat Wire Be Advantageous for Your Application?
Choosing flat wire over narrow-gauge strip is a decision that depends on the subsequent processing steps and in the final application of the material. Strip that is thick for its width might favor flat wire, especially if the edge condition is important and long, uninterrupted lengths are required.
Whether your application needs are for corrosion resistance, high temperature strength, formability, surface appearance, spring properties, or any combination of these, our metallurgical staff at both Ulbrich Shaped Wire and Ulbrich Specialty Strip Mill will help you select the alloy and product form that cost-effectively meets your criteria. Reach out to us today to discuss your part requirements!
Let Ulbrich help you decide and take the guess work out. We're one vendor that can do both and offer greater options than our competitors.