Braid-Reinforced Medical Tubing - The wire producer’s role in enabling optimal braiding performance.
Medical tubing is an essential component in an ever-expanding array of delivery systems and related devices used in minimally invasive surgical procedures. Round or flat stainless steel wire is often used to braid-reinforce tubing for applications that require torque transmission, burst strength, or column strength. The tubing material and wire specifications, along with the braiding PIC count, are collectively used to achieve the desired level of stiffness, torque response, and related characteristics of the tubing.
Producing ultra-fine wires to extremely small dimensions that can be less than 15% the size of a human hair is only the beginning. Precisely controlling the dimensions, mechanical properties, and cleanliness over the length of the wire is essential. The science, know-how, and practices required to enable optimal performance in the subsequent braiding operation is a topic unto itself. It will be the primary area of focus for this article.
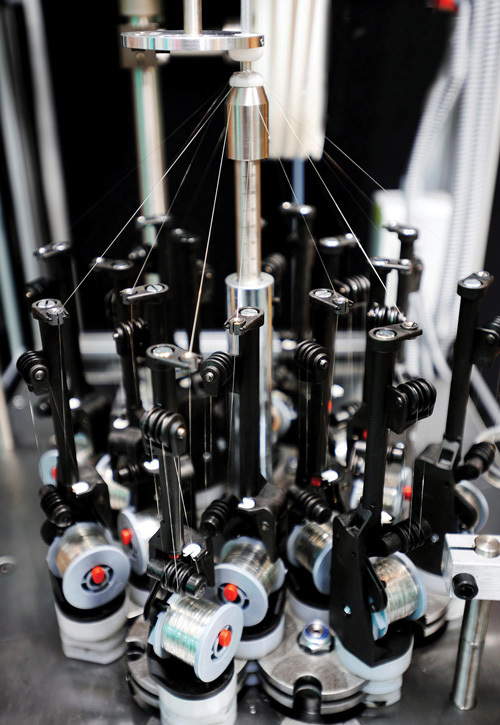
The braiding process requires that wires be wound onto braider bobbins, which are then placed into carriers on the braiding machine. 16 - 32 carrier braiding machines are commonly used in medical tubing applications, though up to 288 carriers can be used in some instances. The wire on every bobbin must unroll smoothly and consistently if the braiding process is to produce suitable braid-reinforced medical tubing.
Problems encountered in braiding that can be attributable to the wire include:
- Tangles
- Breaks
- Kinks
- Twists
- Contamination
Avoid The Breaks! Winding wire onto braider bobbins to enable optimal braiding performance.
Ensuring accuracy in the dimensions of the bobbins and winding device, and precise concentricity and alignment are only the first steps. The wire must be wound with an array of parameters that should be matched to the parameters that will be used in the braiding process itself. A “level wind” can only be achieved if the traverse dimensions, spacing, and reversal settings are appropriately set and controlled. If the wire is not level from flange to flange, it will likely lead to problems during braiding.
Biconical bobbins are sometimes used to make it easier to wind and unwind the wires, but straight-flanged bobbins will perform perfectly well if the winding is controlled correctly. Moreover, the winding tension should be selected based upon the tension that will be used during braiding. Braiding machines typically use special ratchet and tension springs to set and maintain the tension. The wire should be wound with slightly higher tension than the braiding tension. Optimum performance can only be achieved if the wire manufacturer and the braid wire manufacturer work together to define the unique winding parameters for each bobbin to be wound, ultimately based upon the braiding parameters used.
Preventing Tangles and Breaks in the Braiding Process
Wire tangles and breaks can be caused by many possible factors in the braiding process and are not always attributable to the wire itself or the winding parameters used to wind it onto the bobbin. However, there are several factors directly related to the wire that can result in tangles and/or breaks.
For example, if there is a gap between the flange and the layers of wire at one end of the bobbin barrel or the other, the wire can “snag” in the gap as it is unwinding. This will most often result in a wire break. Wire manufacturers must ensure an even and precise wind that eliminates this gap to ensure quality and prevent snagging as the bobbin contents unwind during the braiding process.
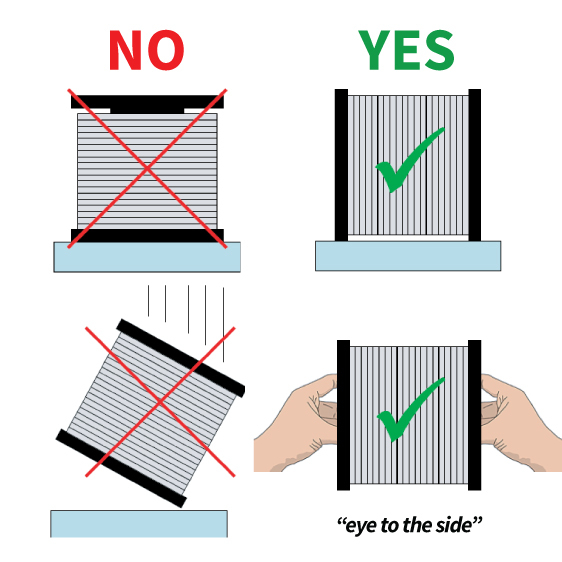
Another common cause of tangles or breaks is when the wind is not level across the length of the barrel; adjacent wraps of wire can slide over or under one another as they are unwound. This results in a tangle and often a wire break. This can also happen if the wire bobbin is stored or mishandled, which is why braid wire manufacturers must ensure that their teams are well trained in proper wire handling to prevent a pristine bobbin from being jeopardized due to user error.
When the tension used to wind the wire onto the bobbin is less than the tension applied in the braiding process, the wire can be pulled into the gaps in the layers below as it is paying off. This is another wire production factor that can cause a tangle or break.
Flat wires in a certain width to thickness (aspect) ratio range can be more prone to tangling or breaking due to the intricacies of their geometries coupled with the winding and braiding processes themselves. This challenge can be effectively addressed with the controlled application of an approved lubricant such as isoparaffinic mineral oil. This method of preventing tangling is widely used within the wire manufacturing industry. It can prevent a great deal of scrap loss and downtime caused by tangling in the precision wire that falls within these aspect ratios.
Wire tangles and breaks result in a stoppage of the braiding process, which results in scrap and time lost restarting the process. It is a problem that all braiders will strive to minimize or eliminate.
Preventing tangles with a mild isoparaffinic lubricant such as IsoPar®
As we mentioned, flat wires within a specific range of aspect ratios tend to be more problematic to braid. The challenges with this category of wires can be overcome by applying a very light, carefully controlled coating of IsoPar®. This mineral oil is used in a variety of personal care products where it comes in contact with the human body. IsoPar® is an isoparaffin that has proven safe in biotoxicity testing and can be beneficial in enabling improved braiding performance for more troublesome wire aspect ratios. It can also help prevent wire shavings that can result from metal to metal contact during the braiding process if the wire is “too clean”.
Avoiding Kinks & Twists
Kink resistance is an essential aspect of a braided medical wire, so it is critical for manufacturers to ensure that the braiding process and the wire being used are set up correctly during the production process to prevent them. If an incorrect or inconsistent wire gap setting is used in the bobbin winding process, the wires may not pay off evenly, resulting in potential twists or kinks.
Twists and kinks do not entirely stop the braiding process but result in a defective product that is not always easy to detect in the tubing. Preventing these defects from occurring is essential for quality control and scrap reduction. Carefully matched and controlled winding parameters, coupled with the selective use of IsoPar® on specific wire sizes, can conquer many of the common root causes of kinks and twists.
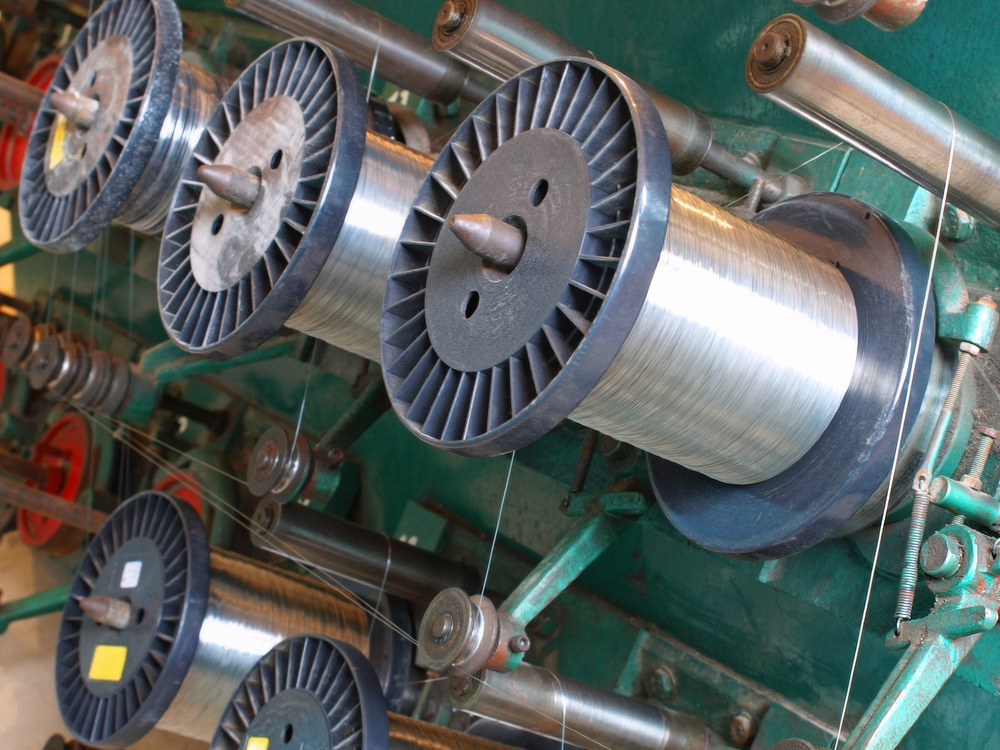
In addition to uneven or mismatched wires being used on braiding machines, many of the factors noted above that cause tangles and breaks can also result in twists or kinks, particularly uneven wind, tension mismatch, and problematic aspect ratio wires that are unlubricated. It’s vital to mutual success, and downstream quality assurance that medical manufacturers and their wire producers work closely together to define critical parameters, specifications, and machine and production settings to ensure that the materials used can achieve the high performance demanded of them. Ulbrich is a constant partner to our customers in developing and delivering high-quality fine and flat wire materials that are kink-resistant and optimized to our customers' unique demands.
Contamination
Contamination can originate from several potential sources. The most common is loose debris introduced onto the tubing, wire or braiding equipment, and substances carried by the tubing or wire itself. Focusing upon what should be done from the wire perspective to prevent contamination, it should be packaged and protected appropriately to avoid loose debris from being introduced during handling and shipping. Potential contaminants that could be carried into the process by the wire can be managed by adequately controlling the wire processing environment and using cleaning processes that are effective in removing residual compounds that are used in upstream cold working processes.
Conclusion
The technical team at Ulbrich Specialty Wire Products possesses a wealth of knowledge and experience in providing braiding wires that will perform effectively and consistently in the braiding processes used to produce braid-reinforced medical tubing. Matching winding parameters with the parameters that will be used in the braiding process is essential in optimizing braiding performance. This can only be achieved if our customer shares their braiding process information with us, enabling us to specify the proper winding parameters for that unique wire item number. Collaborative discussions typically result in practical solutions for these and other challenges related to the design and production of high-quality braid-reinforced medical tubing.
If you are a producer of braid-reinforced medical tubing and have questions or are looking to collaborate on challenges you’re looking to overcome, feel free to reach out to us. We’ll be happy to connect you with one of our metallurgical engineering experts!
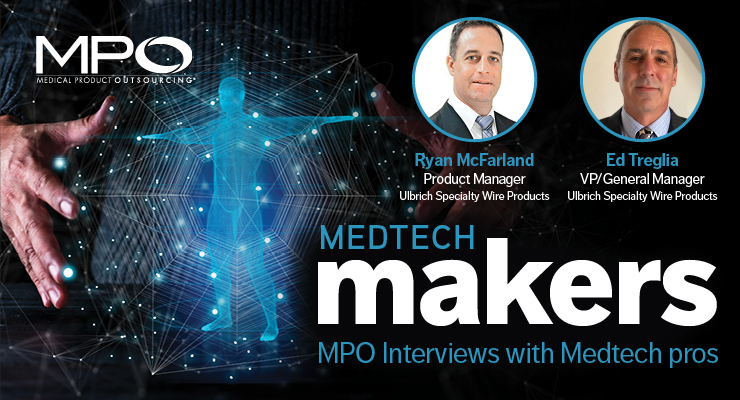
Check out our latest interview with MPO where Ulbrich Specialty Wire Products’ Ed Treglia and Ryan McFarland speak to specification considerations for wire for medical applications.