Titanium Versus Steel: A Battle of Strength
Is titanium stronger than steel?
If you’re looking for a short answer, yes. Titanium has a higher strength-to-weight ratio, making it well-suited for applications that place a premium on stronger, lighter alloys — like aerospace.
Keep reading for the long answer because, like most things in manufacturing, it isn’t quite that simple.
Both steel and titanium are strong, durable, and can easily withstand tough, high-stress environments. The answer to which is stronger can depend on the exact grade of steel or titanium and the context in which it is being used.
Some types of steel are actually stronger than some types of titanium, especially when it comes to hardness or resistance to wear and tear. For example, 17-PH stainless steel can have a higher tensile strength than some titanium grades while still being relatively strong and corrosion-resistant.
It also depends on whether you are discussing alloyed or unalloyed steel. Alloyed steels, such as stainless steel, are generally stronger than plain carbon steel because adding elements (like nickel, chromium, molybdenum, and vanadium) alters the steel's properties and can make it stronger, harder, more ductile, and more resistant to wear and corrosion.
If you’re trying to decide whether steel or titanium is right for the needs of your demanding application, this article will explore the properties, limitations, and advantages of each high-strength alloy.
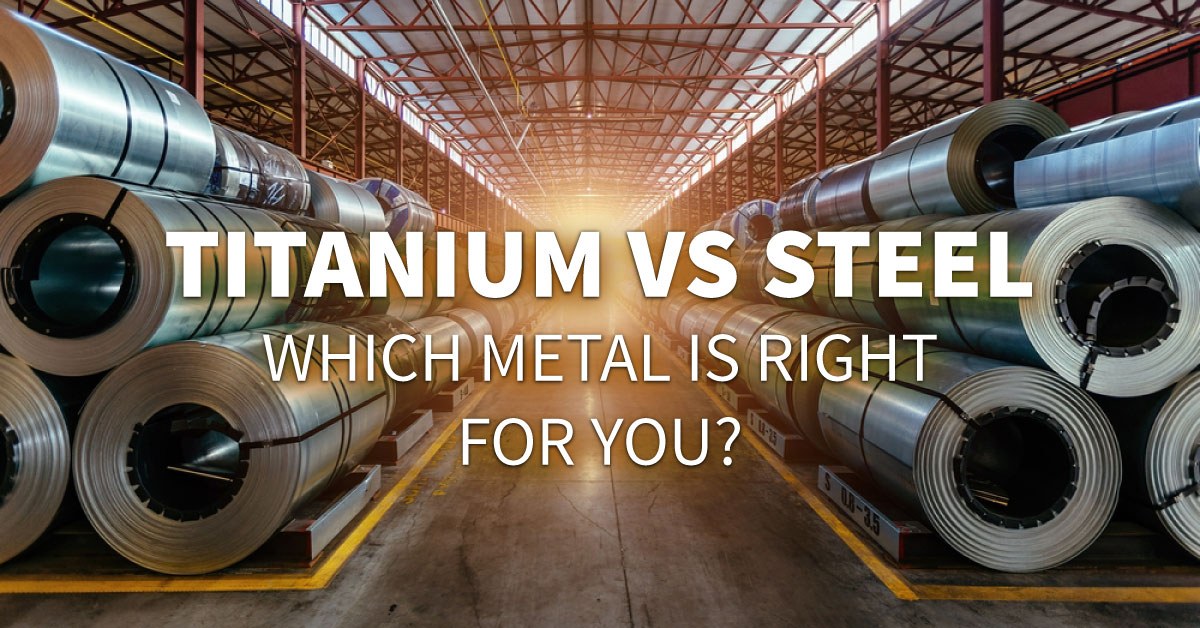
Properties of Titanium and Steel
Many industries prize steel and titanium for their durability, strength, and resistance to harsh environments. However, each material has unique properties that make it suitable for specific applications. Knowing these properties is critical to choosing the perfect material for your needs.
Properties of Titanium
Titanium is a naturally occurring element. Titanium dioxide, which occurs in plants and animals, interacts with oxygen to form titanium oxide, which appears in ores, sand, and soil. William Gregor, an English mineralogist, first identified titanium in 1791 as a new element in black sand.
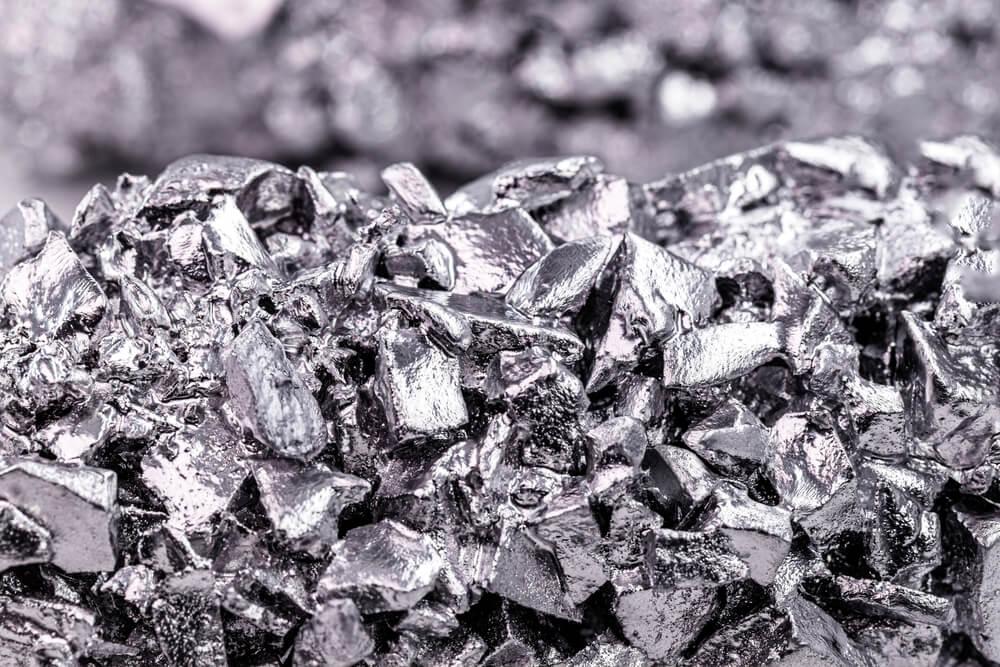
However, it took until 1910 for Matthew Hunter to develop the first commercial process for producing titanium. Hunter’s process heated titanium chloride with metallic sodium in an airtight steel cylinder to make pure metallic titanium. Then, William Kroll invented a new process in 1932, which reduces titanium tetrachloride with calcium to produce ductile titanium.
Several types of titanium exist, including commercially pure (CP) titanium and titanium alloys. While CP titanium delivers high corrosion resistance, a titanium alloy proves ideal for high-strength applications in aerospace and medical implants.
The versatility of titanium results from its strength, light weight, corrosion resistance, and biocompatibility. It is a go-to material for a wide range of applications, including aerospace, medical devices, sporting goods, and jewelry.
Properties of Steel
Steel is an extremely strong, fracture-resistant alloy of iron and carbon. We can trace this material’s origins back to over four thousand years ago, which was the beginning of the Iron Age. As the Industrial Revolution began in the nineteenth century, builders required stronger, more versatile metals to build structures like railroads. Thus, several inventors developed methods to produce steel on a massive scale.
Manufacturers make steel by first smelting iron from its ore. Then, they reprocess the steel to reduce the amount of carbon to the desired ratio. Manufacturers may then add other elements to create a steel alloy, such as manganese, chromium, cobalt, nickel, and titanium.
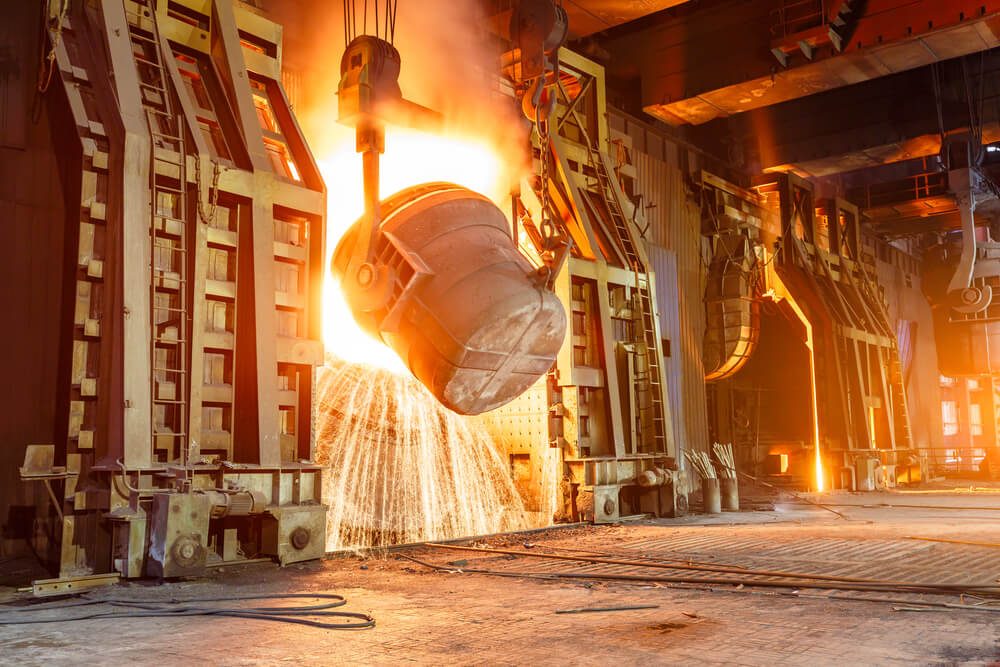
Steel is a very dense material that is physically hard yet simple to work with. It is extremely strong, magnetic, and able to conduct heat and electricity. Due to its strength and low cost, steel is a popular choice for applications like buildings, weapons, ships, and steel frames for cars.
Some types of steel are susceptible to corrosion, however. Stainless steel, a rust- and corrosion-resistant alloy that contains chromium, can help reduce this risk. Manufacturers often use stainless steel for surgical implants and home products, like cutlery, kitchen sinks, and cookware.
Property Relationship of Titanium to Steel
There are several key differences between the properties of titanium versus steel. First, steel is an alloy, while titanium is a chemical element. The production process for titanium is more complex than steel, especially for pure titanium.
Other differences include:
- Steel is stronger than titanium, with higher tensile yield strength. However, titanium offers higher strength-to-weight ratios.
- Titanium boasts excellent corrosion resistance, especially in harsh environments. Some types of steel are more prone to corrosion.
- Titanium is lighter than steel, making it a popular choice for weight-sensitive applications.
- Steel is more widely available and less expensive than titanium.
- Titanium is biocompatible and commonly used in medical implants, while steel has lower biocompatibility and higher tissue reaction risk.
Titanium Strength versus Steel Strength
Both titanium metal and steel are tough and able to withstand high stress, making them ideal for applications where high strength is a key factor. It is common to wonder which is the strongest material. However, the answer is not straightforward.
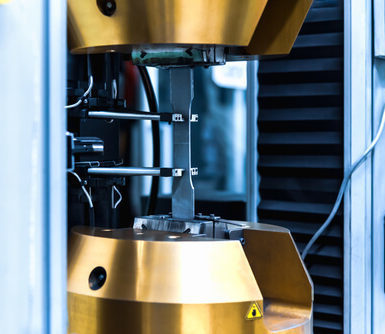
How to Determine Strength
Mechanical tests such as tensile strength, yield strength, and hardness tests determine the strength of steel and titanium.
- Tensile strength tests measure the maximum load the metal can withstand before breaking.
- Yield strength tests measure the stress at which the metal yields and permanently deforms.
- Hardness tests measure the metal’s resistance to plastic deformation by determining the depth of the indentation in the metal surface.
The strength of each metal depends on its composition and microstructure. Steel boasts higher strength than titanium, but titanium stands out for its lighter weight and corrosion resistance.
Titanium’s Advantage
While steel beats titanium in terms of high strength, titanium is lighter and can support more weight relative to its own. This is critical for applications where both strength and weight are factors, such as aerospace, sports equipment, and biomedical implants.
Titanium also has good fatigue resistance, meaning it can withstand repeated stress cycles without failure. On the other hand, steel is more susceptible to fatigue cracking and may not be the best choice for these applications.
Varying Strengths of Steel
The strength of titanium and different types of steel, such as stainless steel, can vary depending on their composition, heat treatment, and manufacturing process. Here is a very general comparison between the two materials:
- Density: 7.8–8 g/cm3 for steel; 4.51 g/cm3 for titanium
- Tensile yield strength: 350 megapascals for steel; 140 megapascals for titanium
- Stiffness: 200 gigapascals for steel; 116 gigapascals for titanium
- Fracture strain: 15 percent for steel; 54 percent for titanium
- Hardness on the Brinell scale: 121 for steel; 70 for titanium
The choice between titanium and steel depends on the specific requirements of the application.
Generally, high strength, low alloy steels have higher tensile and yield strength than titanium. However, titanium has a higher strength-to-weight ratio and better fatigue resistance.
Tool steels have high hardness and wear resistance but tend to overheat. Stainless steel has better corrosion resistance but lower strength. Unalloyed titanium has a very similar tensile strength to carbon steel, but carbon steel is much denser and a better fit for applications like buildings, bridges, and high-strength wire.
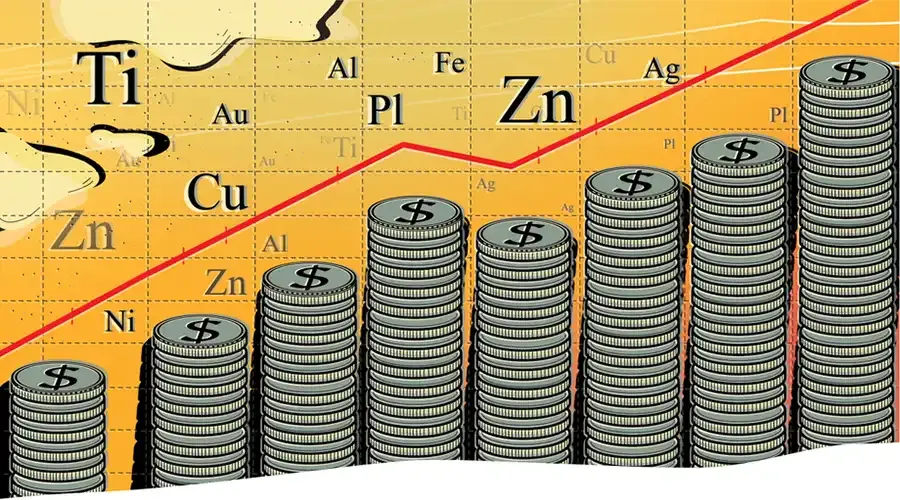
Commercial Viability of Titanium and Steel
Both titanium and steel have unique properties. However, titanium’s cost and availability can impact its commercial viability, which businesses need to consider before selecting a material.
A Limited Resource?
First, titanium is somewhat of a scarce resource, which hinders its availability and raises its cost. This is due to several factors:
- Raw material scarcity: Minerals such as ilmenite and rutile provide the primary source of titanium. However, they are rare and only available in a few countries, limiting the global supply and raising the price of titanium.
- Complex extraction: Extracting titanium from its ores is a complex and energy-intensive process. It requires specialized equipment and high temperatures, which increases production costs and limits availability.
- Growing demand: Titanium has a unique combination of strength, lightness, and corrosion resistance, which makes it attractive to manufacturers. This demand further limits global supply and raises the price. As a result, companies seek cheaper alternatives like stainless steel.
Technical and Commercial Limitations
Titanium can be difficult and expensive to fabricate. The complex and energy-intensive process of titanium extraction and production makes the material extremely costly.
Additionally, there are a limited number of titanium alloys, which makes it difficult to find the right choice for specific applications. The price for titanium is quite high, and manufacturers often seek cheaper substitutes such as stainless steel.
Cost of Titanium
Titanium is generally more expensive than steel due to the factors mentioned above. These prices depend on the specific type and titanium grade but can be as high as $35–$50 per kilogram. Stainless steel can cost $1–$1.50 for the same amount. Titanium alloys are usually more expensive due to additional features like higher tensile strength and flexibility.
Manufacturers need to weigh these costs with titanium’s benefits. In the aerospace and medical device industries, titanium is a preferred choice due to its corrosion resistance and aerodynamics. On the other hand, construction and car manufacturers often choose different types of steel, including stainless steel, for their durability and sheer strength.
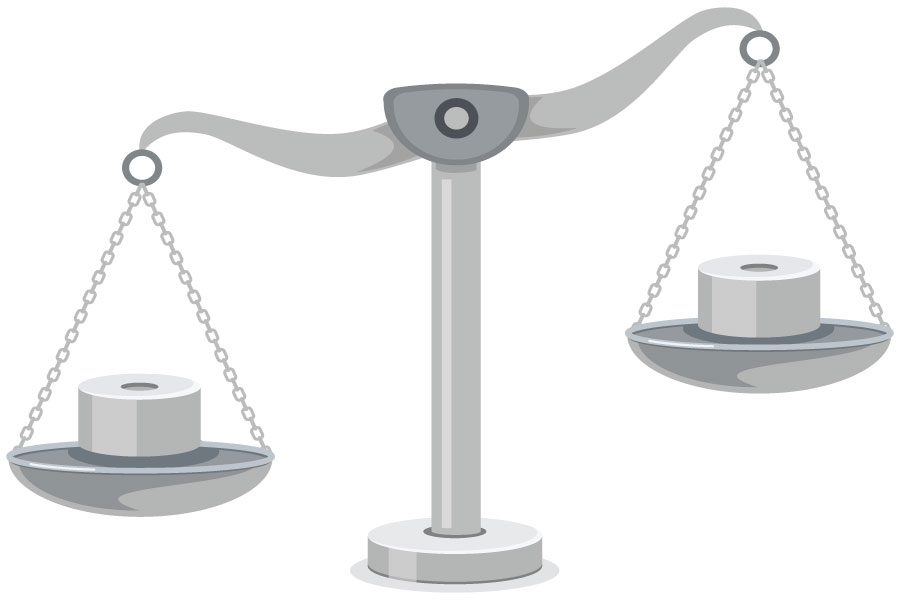
The Choice between Using Titanium or Steel
The choice between titanium or steel is a crucial decision that can impact the success of a project. By weighing the different properties and features, you can decide which material is best for your needs.
Factors to Consider
When it comes to choosing between titanium and steel, there is no clear winner. Both materials have their strengths and weaknesses. Generally, titanium has a better weight-to-strength ratio, while steel wins in its sheer strength and affordability.
Consider the following factors when making your decision:
- Cost
- Strength
- Weight
- Corrosion resistance
- Ease of fabrication
- Availability of alloys
- Biocompatibility, if required
- Durability and life span
When to Choose Titanium
In applications requiring light weight, corrosion resistance, biocompatibility, and high-temperature resistance, titanium can be a better choice than steel. This makes titanium ideal for use in aerospace, medical devices, chemical processing, marine, and high-temperature industrial applications.
When to Choose Steel
Steel may be a better choice than titanium in applications where cost-effectiveness, ease of fabrication, and the availability of alloys such as stainless steel are important factors. Construction, automotive, and heavy machinery companies often benefit from its ease of use, lower price, and wide range of alloys for different requirements.
However, steel’s density and lack of biocompatibility make it unsuitable for many applications, like medical devices and aerospace fasteners. The choice between titanium and steel depends on application requirements and a trade-off analysis of cost, strength, weight, corrosion resistance, fabrication ease, and alloy options.
Your Premier Materials Partner
To choose between titanium and materials like stainless steel, you need to balance the specific needs and demands of your project with the benefits and drawbacks of each material. This process can be complex but having the right materials partner on your side can help.
At Ulbrich, our partnership program starts with a materials evaluation to help identify the right metals and attributes required to reduce risk, decrease failure rates, and increase your speed to market. We work together with our customers to specify the perfect alloy, finish, edge condition, mechanical properties, and more. Contact us today.