The Role of Precision Metals in Clean Energy Innovation
As the world transitions toward sustainable energy sources, the demand for precision-engineered materials in clean technologies is surging. So, too, is the complexity of these applications. From solar power and nuclear energy generated by fission and fusion to fuel cells, electrolyzer and battery technology, evolving and emerging technologies are introducing new material challenges for manufacturers.
Additionally. innovative manufacturing techniques are breathing new life into traditional forming methods.
As our customers adapt to these changes, they rely on us to supply precision metals that can meet their stringent requirements and withstand the rigors of sustainable technologies. Tight tolerances, advanced alloys, and innovative forming methods are shaping the future of clean energy applications—one precise component at a time.
Whether it’s a solar cell or a wind turbine blade, even the slightest deviation can impact performance. As a result, manufacturers are pushing the boundaries of material tolerances. Tighter tolerances mean that the dimensions of metal parts must be controlled within extremely narrow limits.
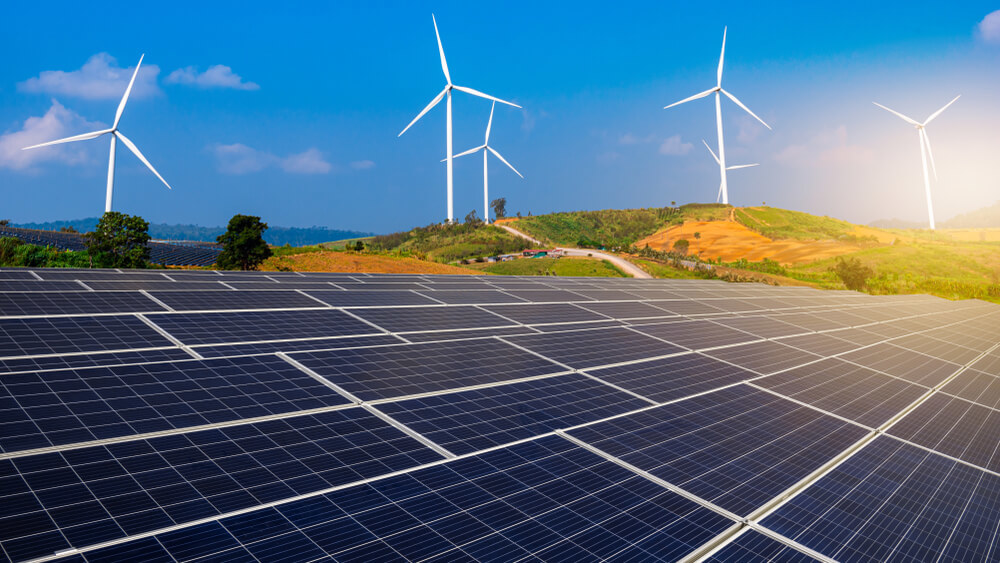
For instance, consider the manufacturing of solar panels. Each photovoltaic cell must be precisely aligned to maximize energy conversion. Any variation in the thickness of the metal substrate can lead to inefficiencies. As technologies improve, the demand for materials with consistent dimensions becomes paramount.
Clean energy applications subject metals to harsh conditions—extreme temperatures, corrosive environments, and mechanical stress. Consequently, alloy mechanical properties are more critical than ever. Engineers seek materials that exhibit high strength, excellent fatigue resistance, and superior corrosion resistance.
Stainless steels, nickel alloys, and titanium are popular choices. These alloys offer a delicate balance of strength, ductility, and resistance to environmental factors. For example, wind turbine blades experience tremendous forces due to wind speeds. Advanced alloys allow manufacturers to design longer, more efficient blades without compromising structural integrity.
In this article, we'll explore unique material properties, supplier requirements, and other considerations for the next generation of clean energy applications. We'll also discuss the crucial role that precision alloys play in powering a greener future.
Fuel Cells & Electrolyzers
Hydrogen is a versatile and clean fuel that — when consumed in a fuel cell — produces electricity that can power facilities or vehicles with water as the only byproduct. It holds enormous potential to reduce greenhouse gas emissions and has unprecedented political and business momentum.
However, producing hydrogen requires a significant amount of energy, and the decarbonization impact of switching to fuel cells depends on how hydrogen is created. If the hydrogen is produced using fossil fuels, it is known as grey hydrogen or blue if fossil fuels are assisted by carbon capture, utilization, and storage.
Producing green hydrogen, which is truly clean energy, is where electrolyzers come into the picture. An electrolyzer can be considered a "reverse" fuel cell that uses electricity to turn water into hydrogen, with oxygen as the only byproduct. For the hydrogen produced to be green, the electricity fed into the electrolyzer must come from a clean energy source, like wind, solar, or nuclear.
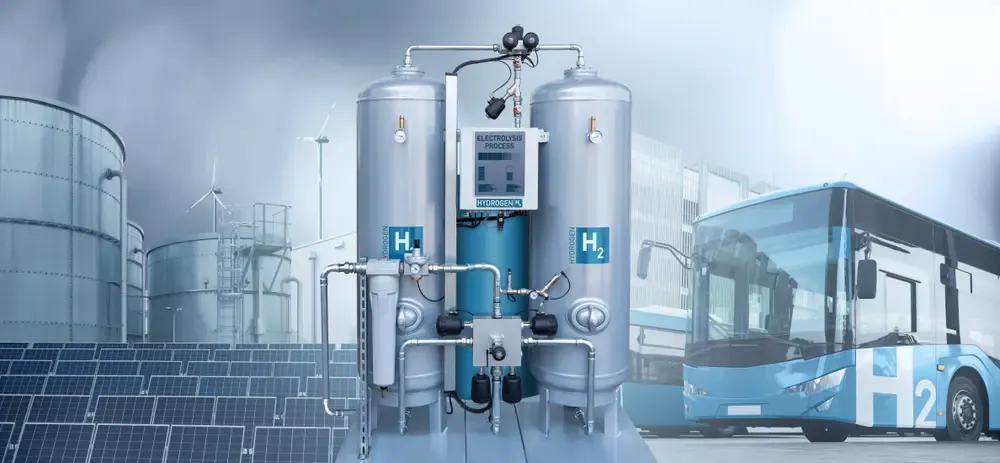
Before we discuss the material requirements for fuel cell and electrolyzer manufacturers, it is crucial to build on this point and note that renewable energy is not created or used in a vacuum. Older technologies like solar and nuclear are often combined with newer technologies like fuel cells and electrolyzers to develop a more holistic approach to clean energy generation. When vetting a materials supplier, consider their expertise across the entire continuum of clean energy applications.
As for precision metals, manufacturers often use thin stamped metal alloys as material for bipolar plates in PEM (proton exchange membrane) fuel cells and electrolyzers.
Role of Bipolar Plates in Fuel Cells and Electrolyzers
Bipolar plates are crucial components within fuel cells and electrolyzers. Bipolar plates facilitate the flow of reactant gases (hydrogen and oxygen) to the respective electrodes (cathode and anode). This efficient gas distribution ensures optimal electrochemical reactions within the cell. Additionally, they serve as a conductive bridge between adjacent cells. The current flows from the membrane electrode assembly (MEA) through the bipolar plates to the end plates. This electrical connectivity is vital for overall cell performance.
Bipolar plates also help manage heat dissipation and water distribution within the fuel cell. Proper temperature control ensures efficient operation and prevents performance degradation.
Finally, bipolar plates also physically separate individual cells, preventing cross-contamination and ensuring each cell operates independently.
Metallic Bipolar Plates vs. Graphite
Traditionally, machine graphite plates were more popular but manufacturers are increasingly turning to thin stamped metallic bipolar plates for several key advantages:
- Reduced Weight and Volume: Metallic plates are lighter and occupy less space, contributing to a more compact and lightweight fuel cell stack.
- Mechanical Strength: Stainless steel and other metallic alloys exhibit excellent mechanical strength, ensuring durability and longevity.
- Cost-Effectiveness: Metallic plates are amenable to high-speed, high-volume manufacturing processes, resulting in significant cost savings compared to graphite plates.
- Better Performance: Metallic bipolar plates provide efficient electron transport, enhancing overall fuel cell performance.
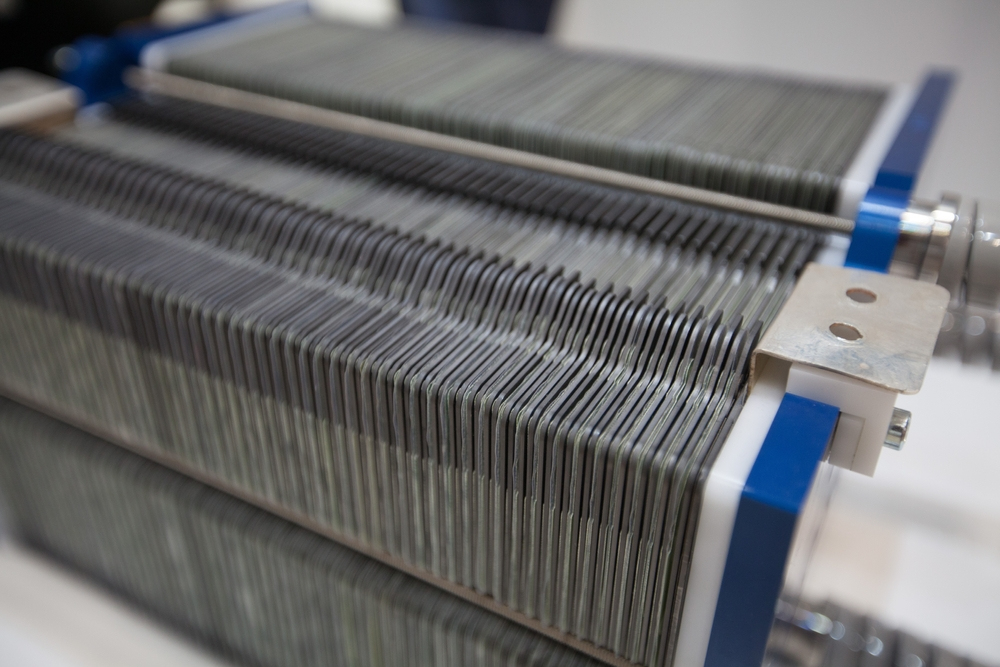
Common Alloys and Important Material Properties for Alloy Bipolar Plates
When choosing an alloy for bipolar plates, consider several key material properties.
- Electrical Conductivity: High electrical conductivity ensures efficient current flow between adjacent cells.
- Corrosion Resistance: Stainless steel and other alloys must resist corrosion, especially in the harsh operating conditions of fuel cells and electrolyzers.
- Gas Permeability: The plates should allow for uniform gas distribution across the MEA.
- Thermal Conductivity: Efficient heat dissipation prevents overheating and maintains optimal operating temperatures.
Several alloys are commonly selected to meet the requirements of these high-temperature, highly corrosive applications. Austenitic stainless-steel alloys, containing a minimum of 8% nickel, exhibit remarkable resistance to both corrosion and elevated temperatures. Consequently, they find widespread use in fuel cell applications.
Nickel 200 and 201 are two special metals that are also known for their corrosion and temperature resistance. They are commonly used in fuel cell applications.
Other special metals that are high-strength, lightweight, and corrosion-resistant are also suited for use in electrolyzers and contribute to efficient hydrogen production.
As for material properties, the thickness of bipolar plates significantly impacts the overall performance of fuel cells and electrolyzers. As these alloy plates are stacked, tight tolerances become paramount. Even the slightest inconsistencies are magnified exponentially with each layer. Imagine a scenario where precision falters—the fuel cell stack might resemble the leaning tower of Pisa, compromising its functionality. These tight tolerances are equally crucial during the secondary processing carried out by fuel cell parts manufacturers.
Beyond thickness, surface finishes play a pivotal role. Different applications and technologies necessitate specific bi-polar plate finishes. The impact of surface finishes on corrosion resistance alone underscores the importance of sourcing materials from suppliers with advanced surface control capabilities.
Enter precision re-rollers—they offer far greater control over surface finishes compared to direct sourcing from a melt mill. For instance, Ulbrich collaborates closely with customers, providing specialized, customized, and application-specific finishes. These finishes are typically measured using parameters such as RA, RY, and RZ, examining different aspects of surface peaks and valleys. Consistency across the material’s length and width ensures a uniform surface finish, resulting in predictable performance for engineers and fuel cell manufacturers.
While each application is unique, several other considerations come into play for each alloy. Factors like temper, finish, and gauge directly impact gas diffusion, electrical conductivity, longevity, and other key performance factors.
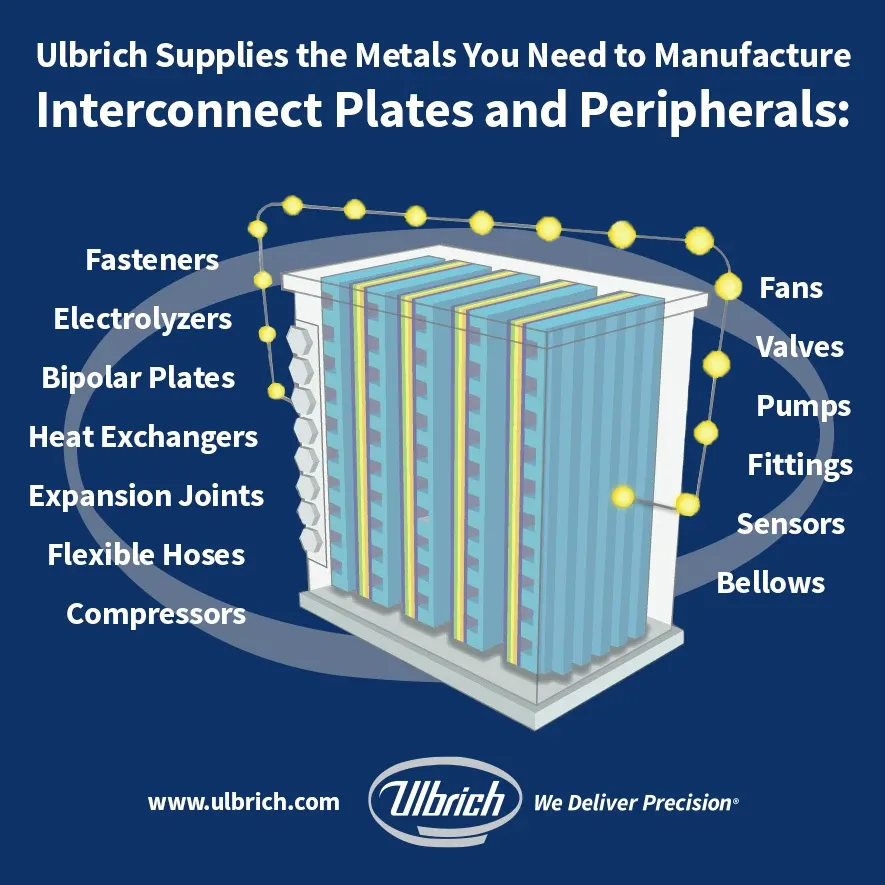
Coatings for Bipolar Plate Corrosion Resistance
Coating is often necessary to protect metallic bipolar plates from corrosion. The aggressive chemical environment within fuel cells can lead to degradation over time. Coatings, such as platinum, graphite, or ceramic, enhance corrosion resistance and extend the plates’ lifespan.
Solar Energy
Solar adoption is on the rise, driven by declining costs and growing recognition of its environmental advantages. Beyond traditional applications, solar energy is making inroads into the transportation sector, with solar-powered vehicles and integrated panels for electric cars becoming increasingly common.
Government policies and incentives play a pivotal role in this growth, stimulating investments in solar initiatives. Technological innovations, such as perovskite solar cells and bifacial modules, are enhancing efficiency and reducing costs, making solar energy more accessible and affordable.
Additionally, the decentralization of solar power through peer-to-peer energy trading platforms and microgrids is empowering individuals and communities, democratizing energy production and distribution. Artificial intelligence (AI) algorithms are being employed to predict energy production, optimize solar panel positioning, and enhance system efficiency.
Recent breakthroughs include longer-lasting solar cells, printable solar panels on flexible surfaces, and even solar power plants that operate at night. As we move forward, solar energy continues to evolve, driving us toward a cleaner and more sustainable future.
Improving Solar Panel Performance with Power-Enhancing PV Ribbon
Photovoltaic (PV) ribbon, also known as solar cell ribbon or solar panel ribbon, is a crucial component in the manufacture of solar panels. It is a flat, thin strip of conductive material that connects individual solar cells together to form an electrical circuit within a solar panel. It collects current from photovoltaic cells and serves as the conductor that joins these cells, carrying the generated current to the distribution system.
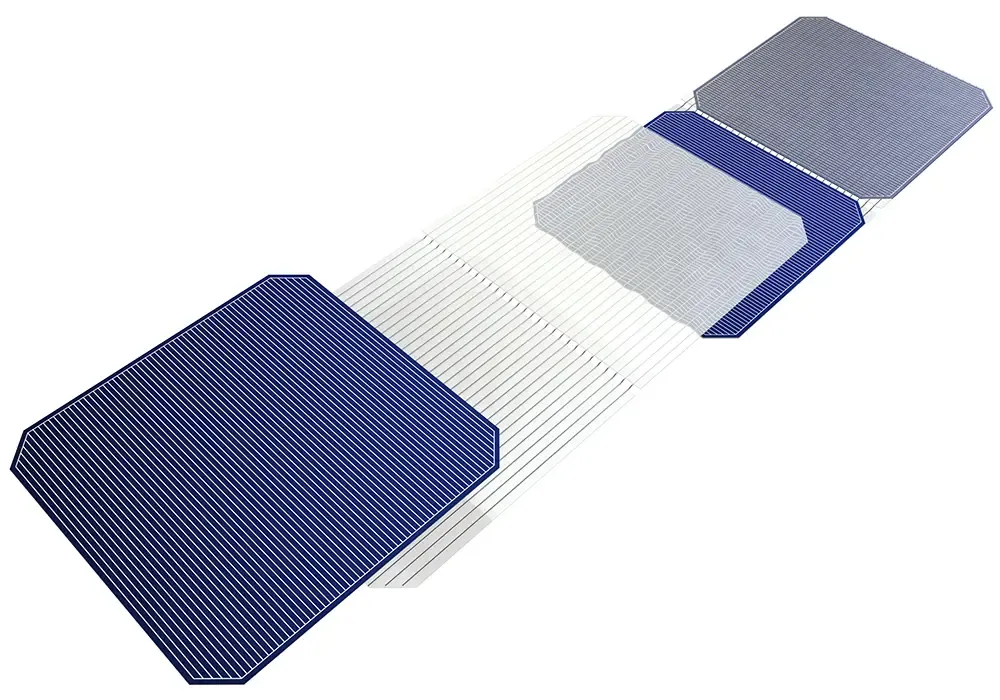
There are two main types of PV ribbon: Interconnect Ribbon, which carries the generated current from all the PV cells to the bus bar, and Bus Bar Ribbon, which carries the accumulated current from the interconnect ribbon to the junction box or electrical distribution system.
Copper is the primary material for PV ribbon due to its high conductivity. Aluminum is less common but used in some cases.
In terms of specifications, the yield strength is the minimum stress required to permanently deform the PV ribbon. Lower yield strength is preferred for thinner panels to avoid stress on the panels themselves. Higher elongation (ductility) withstands contraction and expansion cycles due to outdoor temperatures. Look for at least 20% elongation for reliability.
Standards such as SEMI PV18-0811 and SEMI PV19-0811 guide the specification and testing of photovoltaic connector ribbon characteristics.
PV ribbon is the backbone of solar panels, ensuring efficient energy collection and distribution. Its properties directly impact panel performance and longevity, making it a key factor in the advancement of solar technology.
Nuclear Power
The nuclear energy landscape has been evolving with notable trends. Over the past decade, nuclear power capacity has shown gradual growth, with new units connected to the grid or upgrades to existing reactors contributing to this increase. Despite a slight decrease in total global capacity in 2021 compared to 2020, electricity generation from nuclear energy actually increased by 4%.
The nuclear industry is now characterized by international commerce. Reactors under construction in one country often rely on components supplied from various other countries. For instance, a reactor being built in Asia may have components from South Korea, Canada, Japan, France, Germany, Russia, and more.
Nuclear energy provides about 10% of the world’s electricity from approximately 440 power reactors. It contributes significantly to low-carbon electricity, accounting for about one-quarter of the world’s total low-carbon power in 2020. Beyond electricity generation, nuclear technology plays a crucial role in medicine and industry. Research reactors are used for producing medical and industrial isotopes, as well as for training purposes.
Nuclear technologies are essential for achieving sustainable development. They help control disease, assist in medical diagnosis and treatment, and even power space exploration missions. Some countries heavily rely on nuclear energy. For instance, France gets around 70% of its electricity from nuclear power. Ukraine, Slovakia, Belgium, and Hungary generate about half of their electricity from nuclear sources. Japan, despite challenges, has historically relied on nuclear power for over one-quarter of its electricity.
Fusion Energy & Microreactors
Significant milestones have also been achieved in fusion energy as an alternative to today’s fission reactors. A fusion reactor creates energy by joining atoms, while fission creates energy by splitting them apart.

Fusion offers several advantages over fission as a potential source of nuclear energy.
First, fusion releases nearly four million times more energy than chemical reactions (such as burning coal, oil, or gas) and about four times more energy than nuclear fission reactions (at equal mass). This immense energy potential makes fusion an attractive option for providing baseload electricity to cities and industries.
Second, unlike fossil fuels and fission, fusion doesn’t emit harmful substances like carbon dioxide or other greenhouse gases into the atmosphere. Its major by-product is helium, which is inert and non-toxic.
Third, fusion reactors produce no high-activity, long-lived nuclear waste. The activation of components in a fusion reactor is anticipated to be low enough for materials to be recycled or reused within 100 years. This is in stark contrast to the long-lasting radioactive waste generated by fission reactors.
Fourth, fusion doesn’t use fissile materials like uranium and plutonium, reducing the risk of nuclear weapons proliferation. Finally, unlike fission reactors, a Fukushima-type nuclear accident is not possible in a tokamak fusion device. The precise conditions necessary for fusion are difficult to achieve and maintain, and any disturbance causes the plasma to cool within seconds, stopping the reaction.
In December 2022, scientists focused 2 million joules of laser energy onto a tiny target, causing hydrogen fuel to compress and release energy through fusion reactions. For the first time, more energy came out than what went in, demonstrating net energy gain. This breakthrough vindicated decades of effort by researchers.
Micro reactors are also gaining prominence due to their sustainability. These reactors offer enhanced process efficiency, a smaller footprint, and reduced capital costs. They find applications in various industries, including chemical processes. Micro reactors produced through additive manufacturing (3D printing) are on the rise. Their exceptional properties include flexibility, productivity, and efficiency. North America and Europe experience steady growth, driven by government initiatives and increased consumer awareness. Asia-Pacific, particularly China, leads the global micro reactors market due to robust domestic demand and supportive policies.
Fusion research continues to advance, and microreactors offer exciting prospects for sustainable energy. As we navigate the complexities of these technologies, collaboration and persistence remain key.
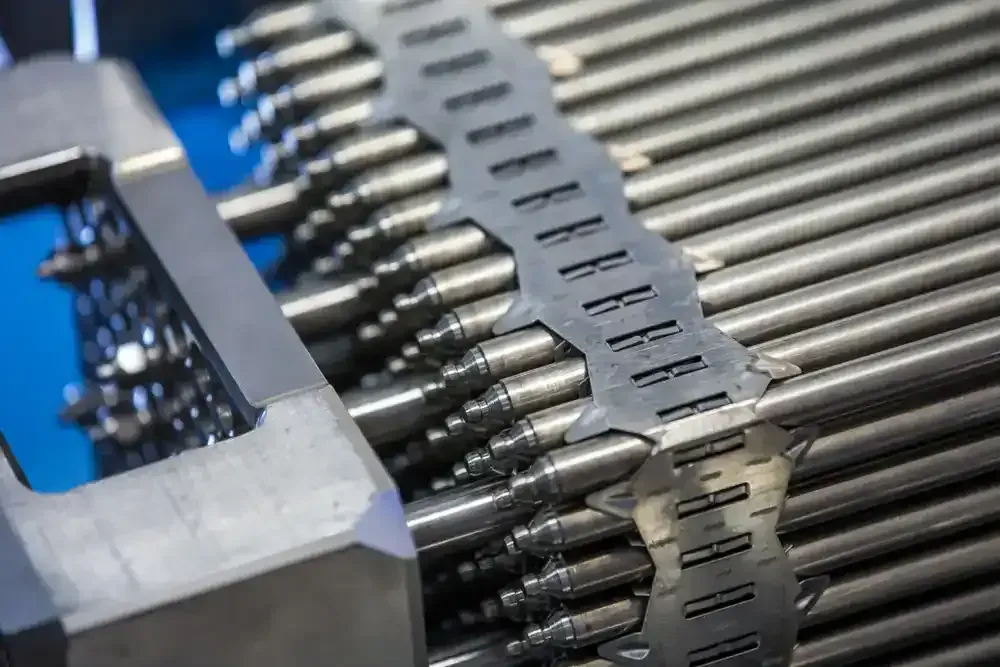
Common Alloys & Applications for Precision Metals in Nuclear Energy
There are three main categories of materials used for nuclear precision strip & wire. These materials are often used in close proximity to fissile material in the fuel fabrication process due to their suitability for highly corrosive and high-temperature environments. For strip & wire, these three commonly used nuclear energy materials are a nickel-chromium alloy, another nickel-chromium alloy with added titanium and aluminum, and a low-carbon, nitrogen-enhanced stainless steel grade. The melt chemistries of these materials are closely controlled, with a focus on lower Cobalt (Co) percentages than typical chemistries. This tight control is essential for nuclear reactors to function properly, and a lack of attention could have catastrophic consequences.
The first nickel-chromium alloy is precipitation hardenable and has high creep-rupture strength at high temperatures to about 1300 °F (700 °C). Its resistance to high temperatures and other properties make it ideal for use in nuclear fuel bundle assemblies and structures in both strip & wire form.
The second nickel-chromium alloy, with the addition of titanium and aluminum, is also precipitation-hardenable and has high creep-rupture strength at high temperatures to about 130.0°F (700°C). It also has excellent properties in cryogenic temperatures, superb corrosion and oxidation resistance, and high strength at temperatures up to 1300°F.
Whether an application uses the first or second nickel-chromium alloy depends on the design of the nuclear reactor. If you have questions about your use case, don’t hesitate to contact us.
The low-carbon, nitrogen-enhanced stainless steel grade is more resistant to general corrosion than conventional chromium-nickel austenitic stainless and offers higher creep, stress rupture, and tensile strength at elevated temperatures. The nitrogen in this stainless steel grade provides solid solution hardening, raising its minimum specified yield strength compared to other stainless steel grades. These properties make this stainless steel grade ideal for nuclear fuel bundles where strength and corrosion resistance are needed.
Other materials used in nuclear energy include a high melting point metal, a higher-chromium alloy with added cobalt and tungsten, and a commercially pure metal with a protective oxide layer for superior corrosion resistance.
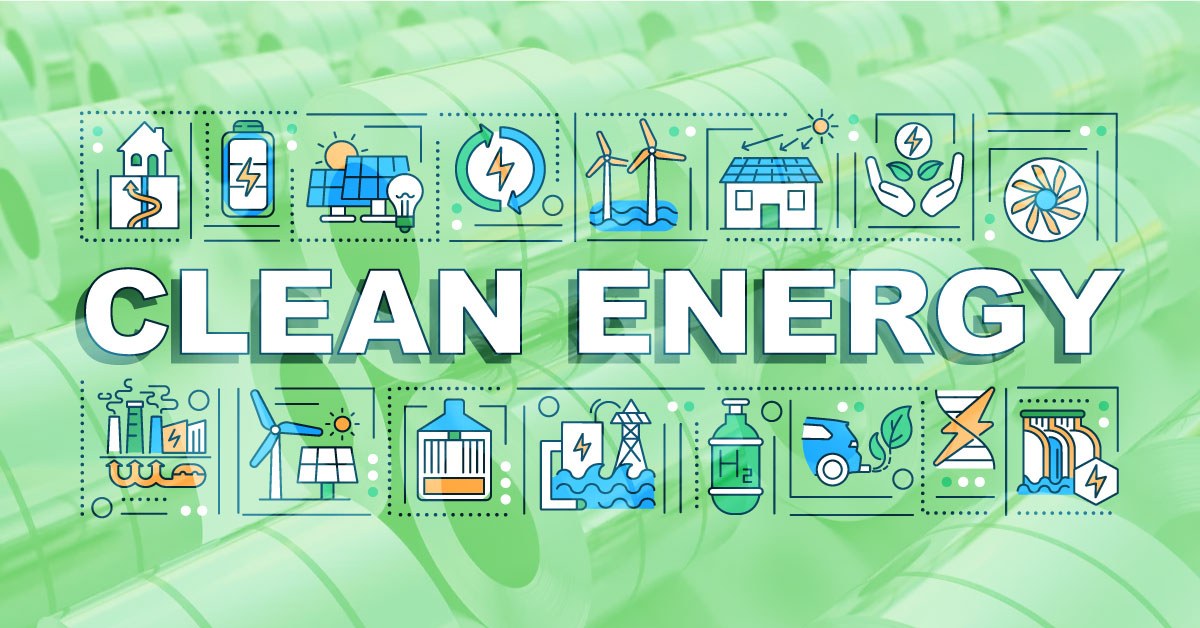
Your Development Partner for Precision Metals in Clean Energy Applications
As innovative green technologies continue to emerge, the demands placed on metals are reaching new heights. These materials must exhibit precision characteristics to meet the exacting requirements of clean energy applications. Simultaneously, manufacturing processes are evolving rapidly, necessitating materials that align not only with the end-use application but also with the production equipment.
Collaborating with a knowledgeable supplier—one who recommends suitable alloys, provides sample quantities, and iterates alongside you—can significantly enhance the journey toward a greener future.
At Ulbrich Stainless Steels & Special Metals, we take pride in our role as a leading supplier of high-quality materials for both legacy and cutting-edge technologies. We don’t just supply materials; we empower clean energy pioneers. From solar panels to nuclear energy plants, and from fuel cells to electrolyzers, our meticulously tested, rigorously crafted alloys play a crucial role in powering a greener future.
Contact us
to speak with one of our expert metallurgists about the needs of your clean energy application.