4th Industrial Revolution Lean Principles
The Fourth Industrial Revolution, or Industry 4.0, is upon us. Today we are going to discuss how our Lean journey is related, and how it has prepared us to integrate emerging technology into our work and our lives as manufacturers.
Industry 4.0 brings with it a fascinating series of tools and technology. But like Lean, to focus exclusively on the tools would be to miss the point entirely. At Ulbrich, we think it’s better to focus on how both things can be integrated to improve and support our people and drive our values. If you’re in manufacturing – we think you should, too.
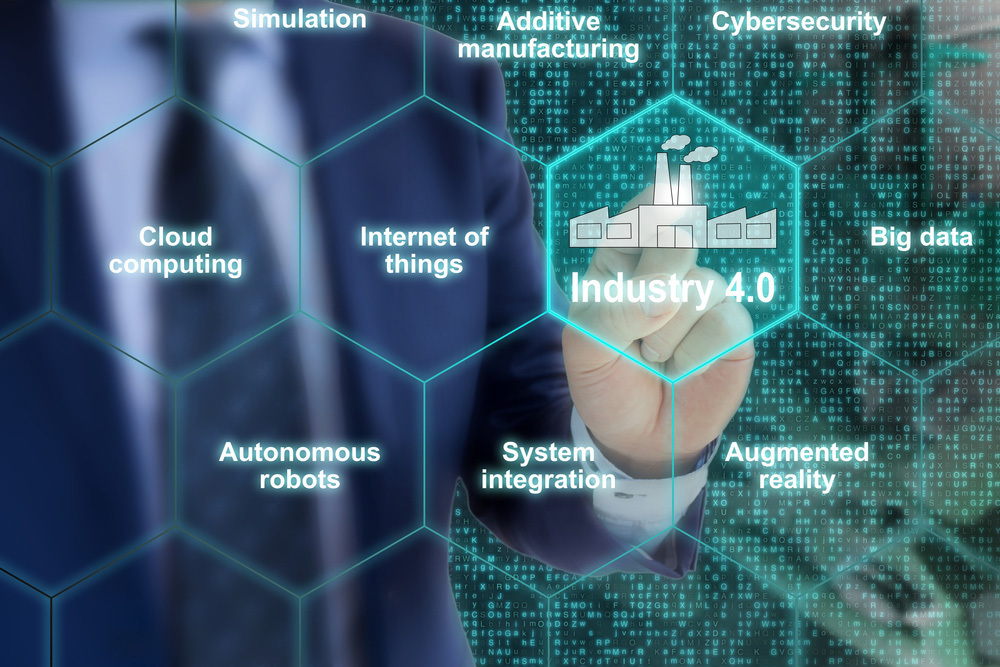
In Lean we have a term, “Jidoka”,which is often over-simplified to mean "respect for people". What Jidoka really means is people doing work worthy of their skills and intelligence, and machines assisting them by performing overly complex or burdensome tasks, as well as the mundane and repetitive. Technologies such as Artificial Intelligence, Augmented and Virtual Reality, and the Internet of Things represent man and machine working together to achieve greater performance. Industry 4.0 is a Lean enabler, respecting the distinction between work worthy of our people, and work that can be performed using machines or technology.
AI, AR/VR, and IoT enable and support the adoption of the 14 Principles of the Toyota Production System, which encompass the main tenets of Lean. We can see clear opportunities to develop and implement a long-term philosophy to eliminate waste, create better process flow, continue to grow and develop exceptional people, and become a learning organization at Ulbrich. Successfully implementing emerging technologies will require cross-functional teams to come together and work cooperatively to ensure proper, successful results. Our A3 teams do this every day to solve problems, improve processes, and make us safer. We know how to work together to assess our current condition and determine the best steps to build a path to our desired future state.
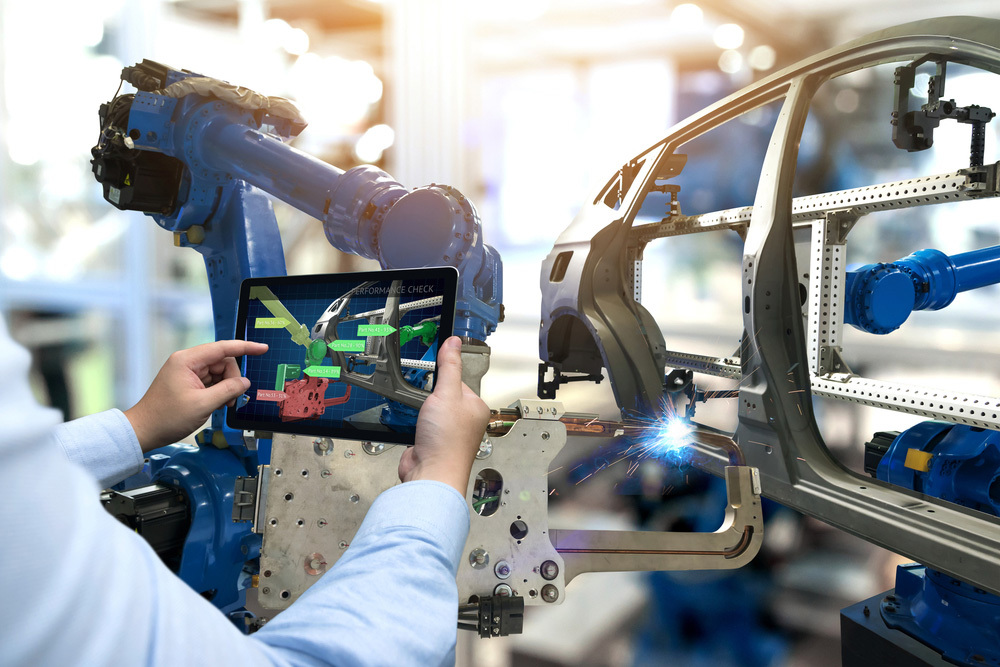
Proper integration of new technology will often require multiple iterations before final implementation is realized. In Lean we have a process of "Plan, Do, Check, Act," which we use in cycles to affect improvement, and achieve the results we want. Industry 4.0 enables fast feedback so learning can be incorporated into the next attempt. In Lean this is the “fail fast, often, and small” method of facilitating continuous improvement. It allows people to iterate bravely and confidently.
Always falling back on these principles, people at all levels of the organization will be empowered to make data driven decisions, consistent with the progressive role of leadership and supporting the power and spirit of Industry 4.0 and Lean. Rather than managers analyzing stale and possibly inaccurate data, the technology afforded to us can provide accurate and timely information to the people who execute the processes and put the decisions in their hands. This truly represents respect for people by directly providing them with the tools and information they need to be successful and entrusting them to do the things that they are best positioned to do.
Our Lean journey has prepared us in a unique and extraordinary way for the Fourth Industrial Revolution, and the tools and values that we’ve learned will integrate perfectly, because they are essentially the same.